Control Systems Engineering
Control Systems Engineering involves using computer processors to automate and monitor the operation of processes, equipment and machinery. A control system accepts data from the field (e.g. a tank’s level) or from an operator (via an HMI (Human Machine Interface)) and based on the logic configuration (i.e. algorithm) configured by the Control Systems Engineer, the control system may execute an action (e.g. such as starting up a pump to drain the tank). Control systems also assist the operator by continuously monitoring the operation and bringing to the operators attention information that requires action. Control systems also capture historical data, providing valuable plant data which may be used for fault finding or assessing plant productivity and efficiencies.
Orana Engineering specialises in Control Systems Engineering with broad experience including PLC (Programmable Logic Controller) and SCADA (Supervisory Control and Data Acquisition) configurations through to configuration of DCS (Distributed Control System) for larger scale operations. We design, test, commission and improve control systems for coal, metalliferous, oil and gas clients as well as industrial and commercial clients.
Our control system configurations focus on:
- Providing full diagnostics, so operators don’t need to look for the problem, it is brought to their attention;
- Capturing historical data, essential for fault finding and benchmarking for operational improvements;
- Consistency, so it is easier for operations and maintenance personnel to become familiar with how to operate and maintain the system; and
- Modular programming, so the system is adaptable to operational changes.
Explore the case studies below for more information on Control Systems Engineering by Orana Engineering.
Orana Engineering Control Systems
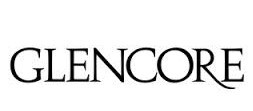
Rajant Network
Glencore planned to install the CAT MineStar Terrain Office system at its Oaky Creek Coal Mine to support GPS positioning and live maps in CHPP stockpile dozers. As part of the upgrade, mine infrastructure and dozers required hardware installation to connect the dozers to the site network and enable communication with MineStar servers. In line with other Glencore sites, it was chosen to implement a Rajant wireless network to cover stockpiles and provide connectivity between dozers and the network.
Orana Engineering was engaged to provide electrical and Operational Technology (OT) engineering design, configuration and drafting support for the CAT MineStar GPS implementation including preparation of three new virtual servers for various applications. Orana Engineering electrical engineers developed a scope of work which provided an overview of the onsite electrical installation works required to be carried out by others with supply, installation, testing and commissioning project managed by an Orana Engineering electrical and control systems engineer.
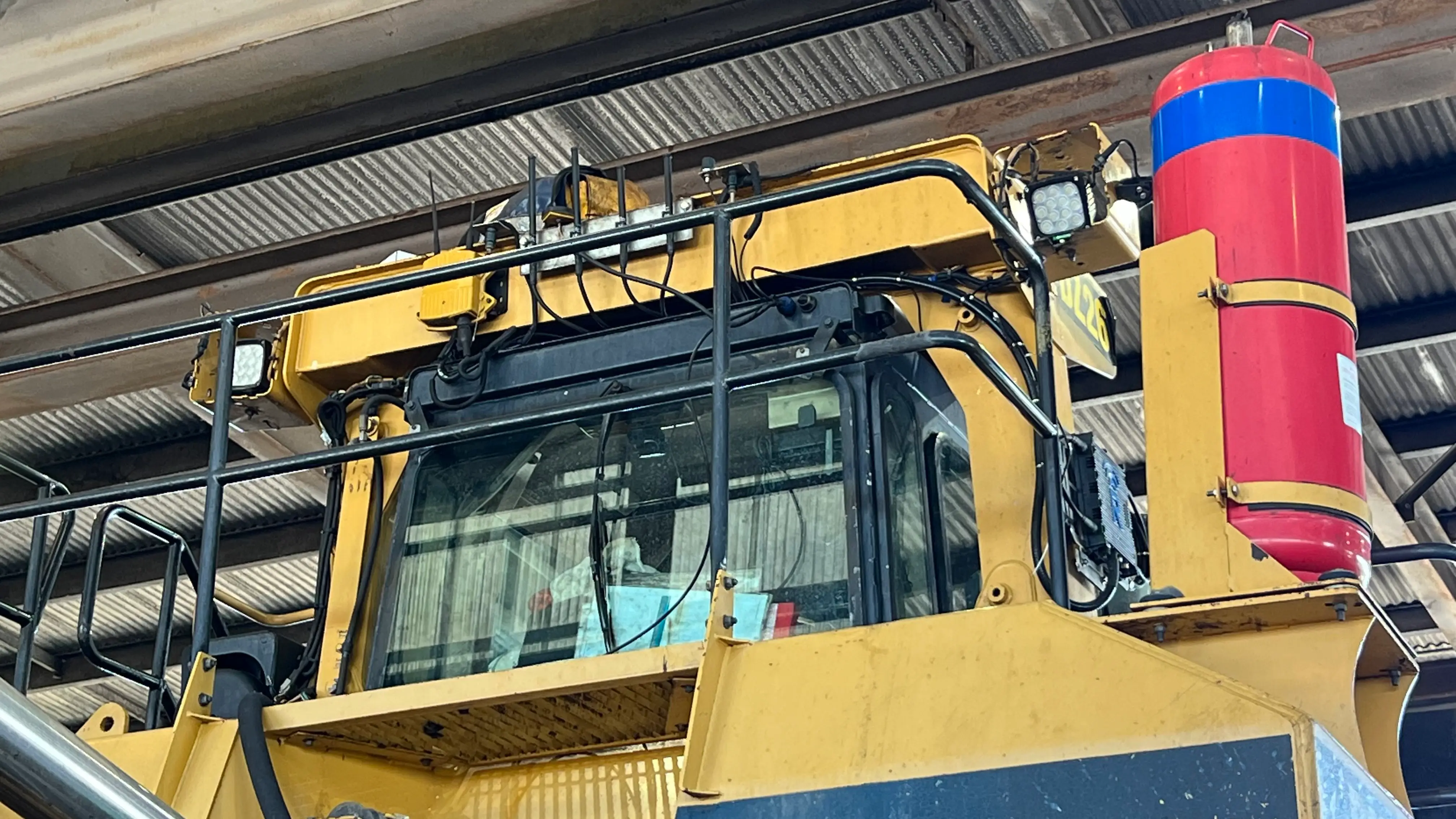
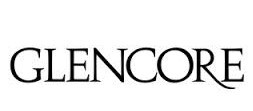
Clarified Water Upgrade
Orana Engineering was consulted by Glencore’s Collinsville mine to assist with an upgrade of its CHPP washdown water distribution system. The CHPP clarified / raw water is supplied from either an anti-pollution pond or the raw water Sunwater pipeline, with the wash water distribution network delivering water to the yard area, CHPP washdown sprays, lime / flocculant dosing or conveyors for spray bars and washdown.
Following hydraulic modelling, Orana Engineering’s mechanical engineers delivered a design with improved flow and pressure, (increasing capacity from 375 to 700 cubic meters per hour) while structural engineers produced SpaceGASS modelling of pipe supports and 3D modelling of the discharge structural steel pipe rack. Additionally, a Functional Specification or Function Description was produced for integration of the design into the plant's control system.
Project deliverables included an Equipment Register, Scope of Supply, detailed Construction and Installation Scope of Work for Tender, Functional Description and detailed design drawings.
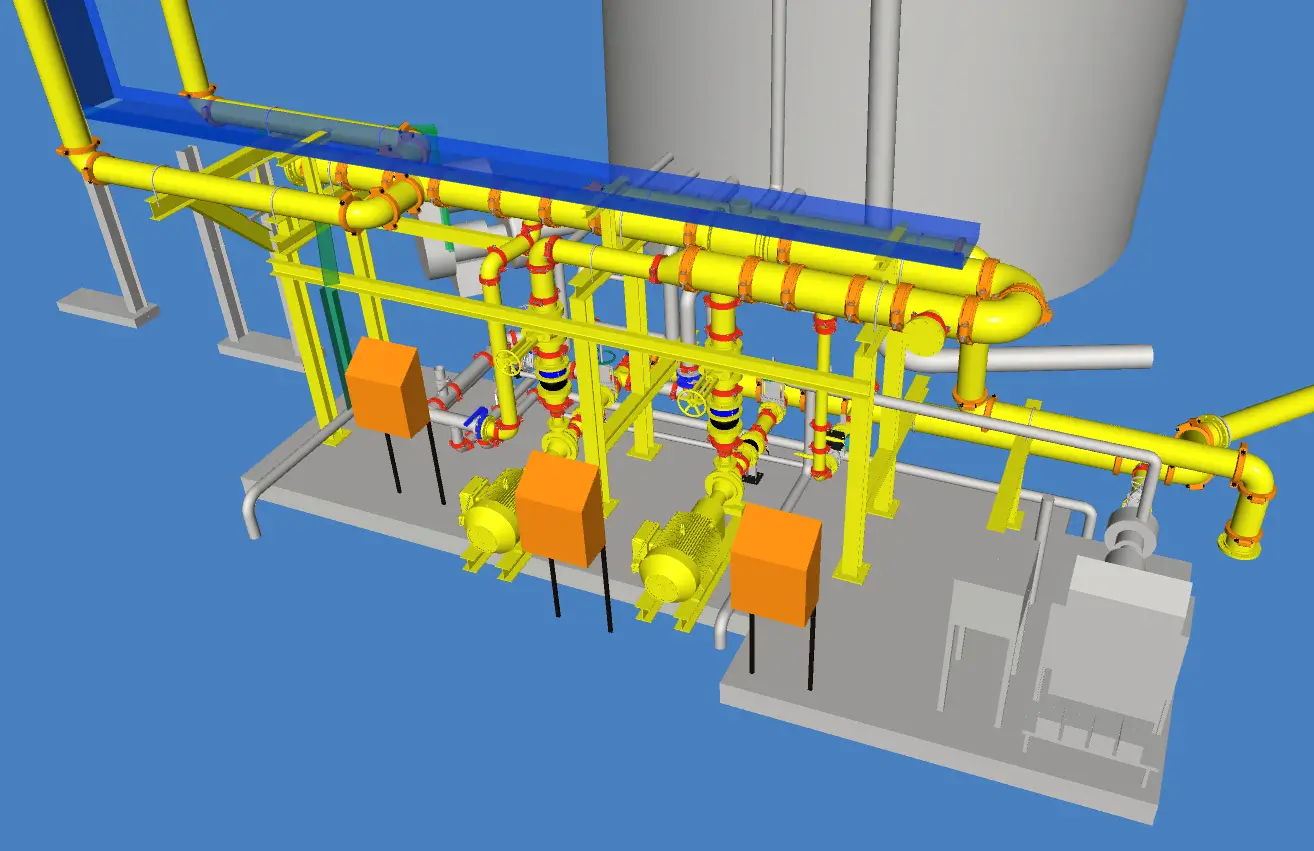
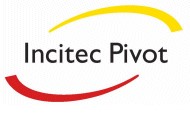
Gas Turbine No.1 Protection Relay Upgrade
Incitec Pivot was looking to replace an existing turbine generator pole slip relay unit at its Phosphate Hill Power Station. Existing pole slip relays had become obsolete and were at the end of their expected life. Pole slip relays perform a critical protection function for turbine generators and operation of a generator without its pole slip relay would pose an unacceptable risk. Consequences of relay failure on turbine generators would be multiple gas turbines being unserviceable and resulting in power shortages across the site.
The project scope involved replacement of Multilin 489 protection relay with new Multilin 889 for a 4.5MW gas turbine generator as well as integration of pole slip protection and a synchronisation check facility into the Multilin 889.
Orana Engineering’s input for the project included electrical engineering design, protection configuration, on site project management and commissioning.
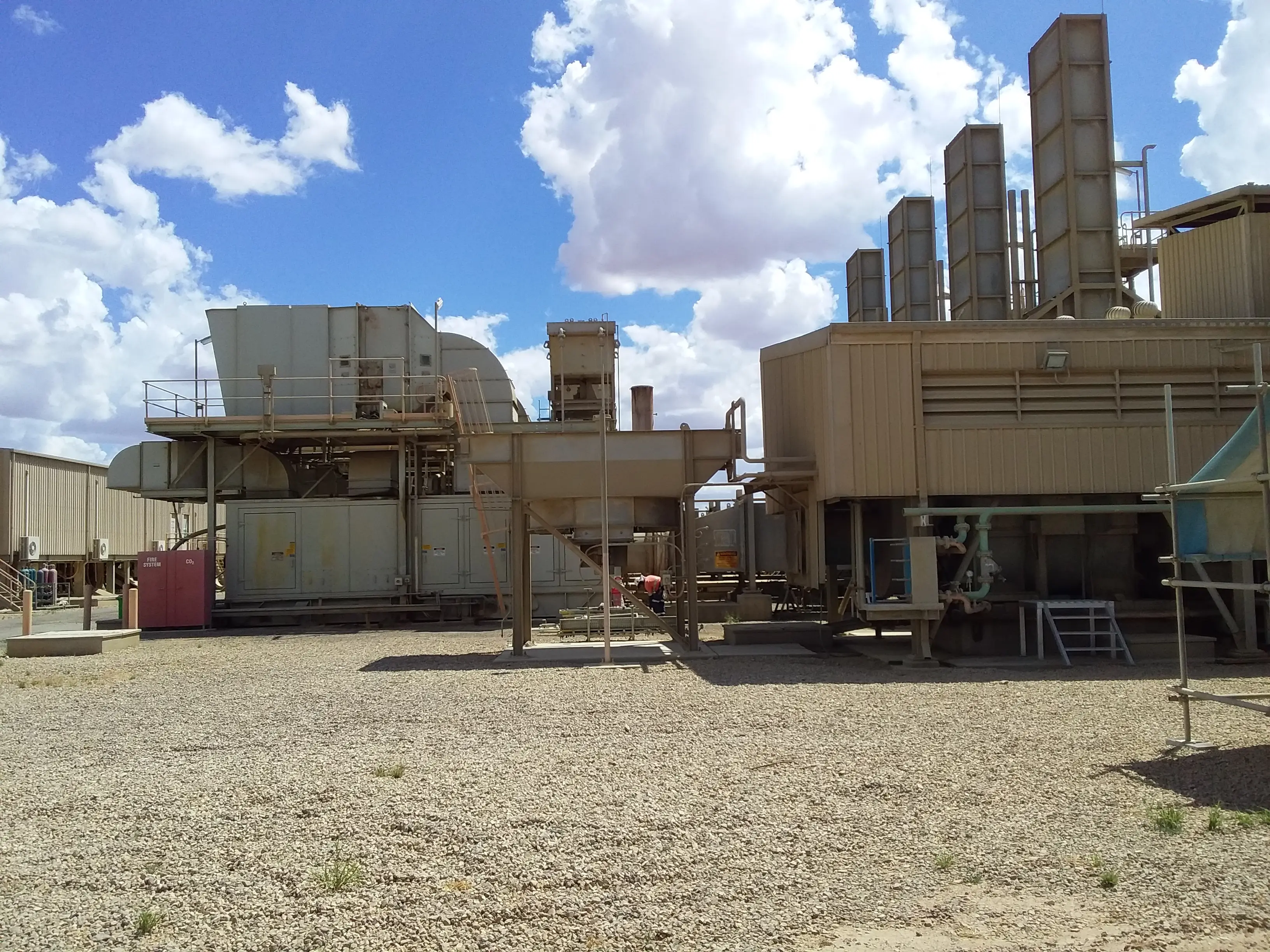
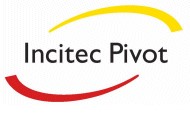
Acid Unloading Leak Detection & CCTV Upgrade
To reduce the likelihood of potential spills in the sulphuric acid unloading area at its Phosphate Hill site, and to prevent consequential environmental and health and safety impacts, Incitec Pivot sought assistance from Orana Engineering with an upgrade of existing acid unloading leak detection and CCTV systems.
In consultation with Phosphate Hill site stakeholder personnel, Orana Engineering conducted an evaluation of available mitigation scenarios before recommending electrical and control methods which were considered to be the most cost effective resolution. Orana Engineering drafting personnel also produced detailed design drawings for the acid unloading leak detection and CCTV upgrade works.
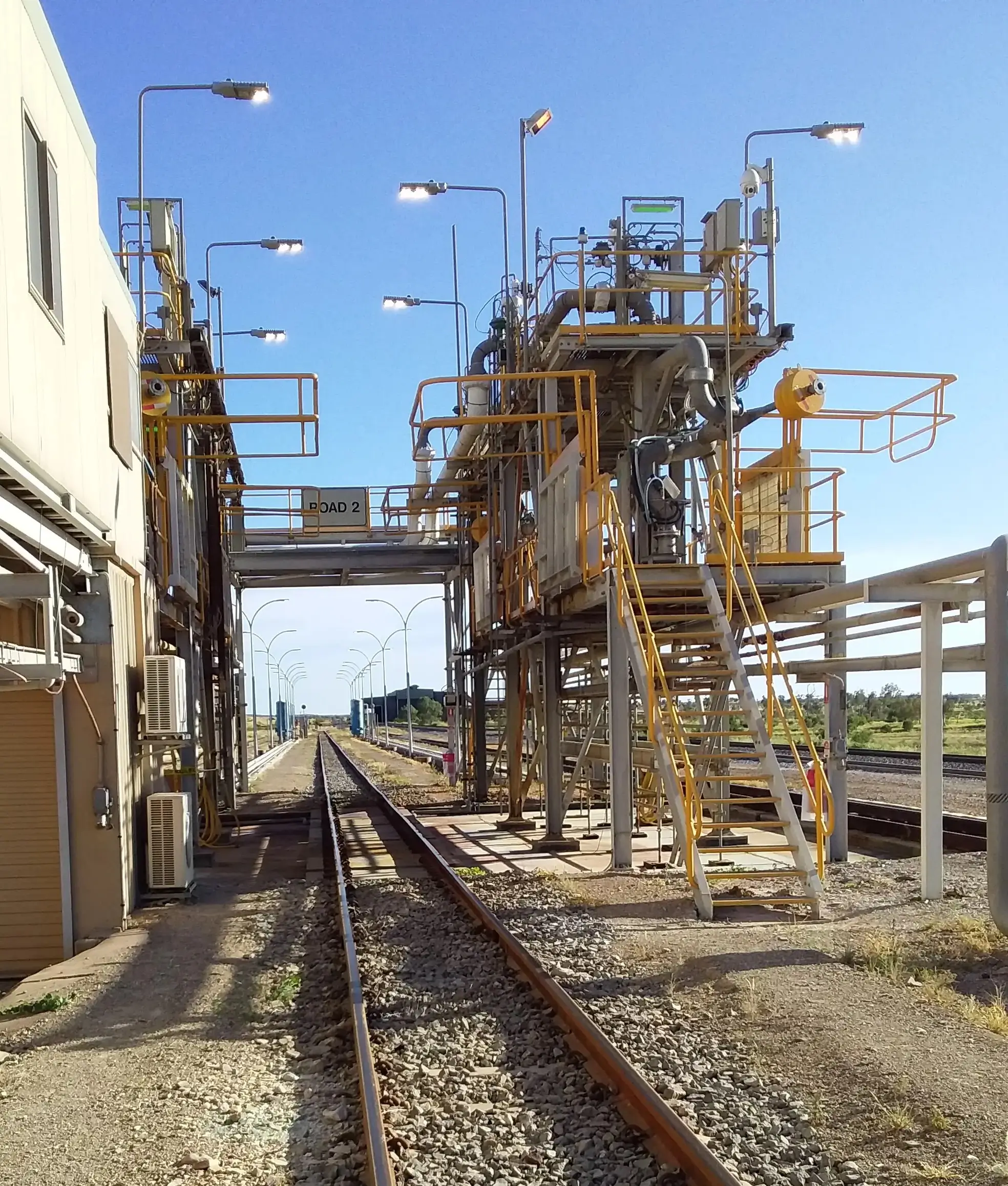
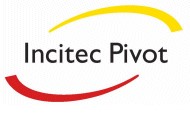
Airport Lighting
Incitec Pivot’s Phosphate Hill site contacted Orana Engineering to request assistance with evaluation of its Monument Aerodrome runway and apron lighting system following a review of potential electrical hazards.
An assessment of the airport lighting installation was undertaken by Orana Engineering electrical engineering personnel with findings presented to the client in report format. Review considerations included reference to CASA and Australian Standards and outlined a high level risk assessment conducted to quantify electrical safety risks.
Following client consideration of recommendations, Orana Engineering provided front end loading (FEL 3) documentation for replacement of existing runway and taxiway lights, series isolation transformers and the existing lighting control system. A scope of work was then prepared with the tender process managed by Orana Engineering on behalf of the client for the appointment of a specialist airport lighting contractor to complete design and construction of the lighting and control system upgrades.
_1.webp)
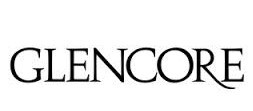
Terminal Dam MCC
The Terminal Dam pump station at Glencore’s Oaky Creek coal mine is critical in supplying the mine and township of Tieri with raw water. The existing pump station had been in service for over 30 years during which time the electrical reticulation equipment had regular maintenance but no significant upgrades. Obsolete components, changes in Standards and degradation of the equipment all signaled that the HV supply, LV MCC and LCU’s was apporaching its end of service.
At the request of Oaky Creek Coal, Orana Engineering undertook offsite electrical and control system engineering and design drafting for a Terminal Dam HV upgrade and MCC replacement. An update of the Electrical Installation SOW for the modification at Terminal Dam was prepared prior to attending site to complete the configuration and assist with project management of installation and commissioning works.
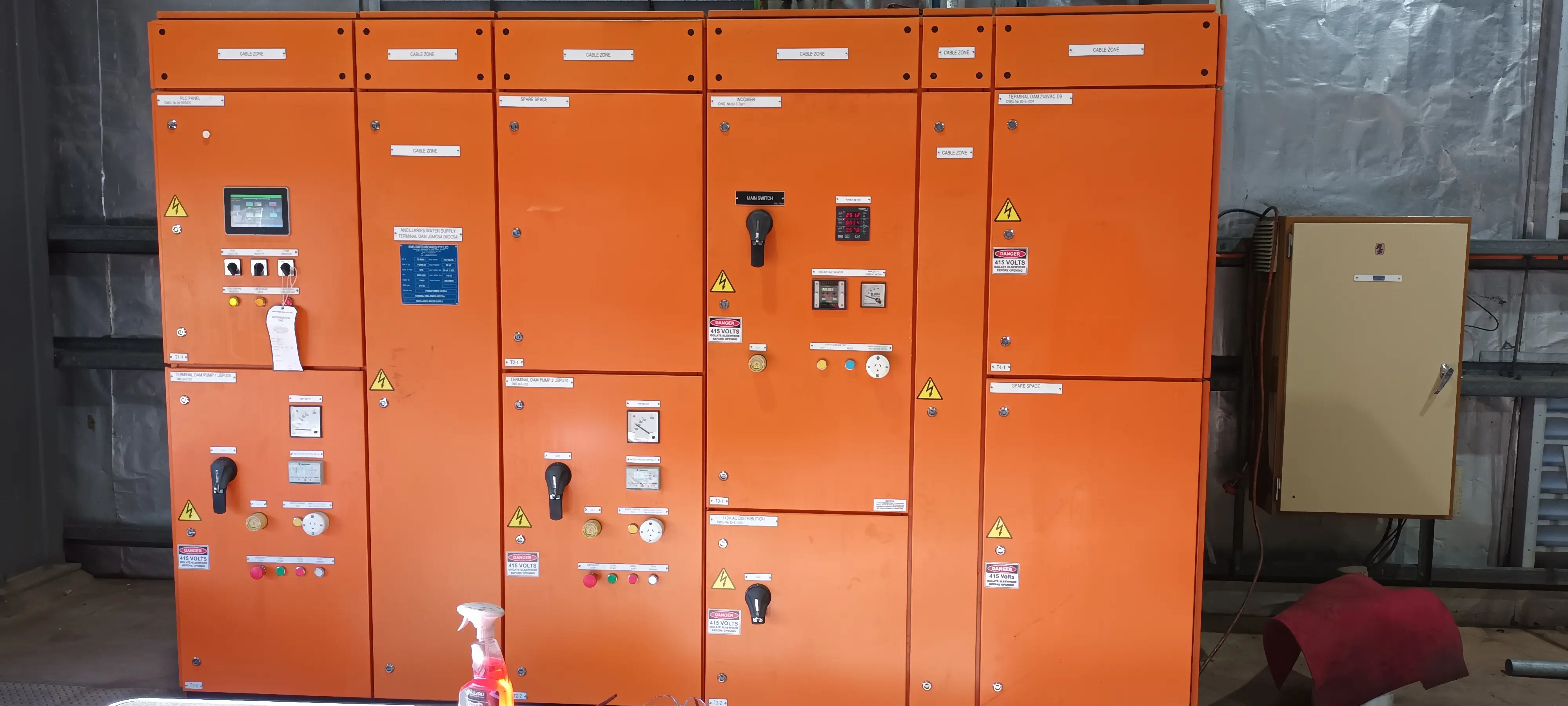
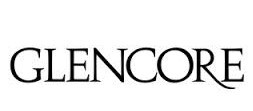
Fire Pumps Automation
The main plant raw water boost pumps at Glencore’s Oaky Creek Coal were supplied via a starter panel which required replacement due to water inundation and for improved functionality, reliability and compliance.
At the client’s request, Orana Engineering provided a report outlining preliminary design checks completed and provided a high-level summary of installation works required to the pump starter panel for a new MCC already on site.
Multiple upgrades were required to electrical equipment as well as associated civil / structural works. A preliminary concept sketch was prepared giving an overview of proposed upgrades. An Orana Engineering Electrical Engineer was appointed to assist with onsite commissioning of the raw water boost pumps and to provide offsite assistance with DCS configuration.
Deliverables to the client included electrical engineering and design drawings to IFA/IFC, a scope of work and a bill of materials.
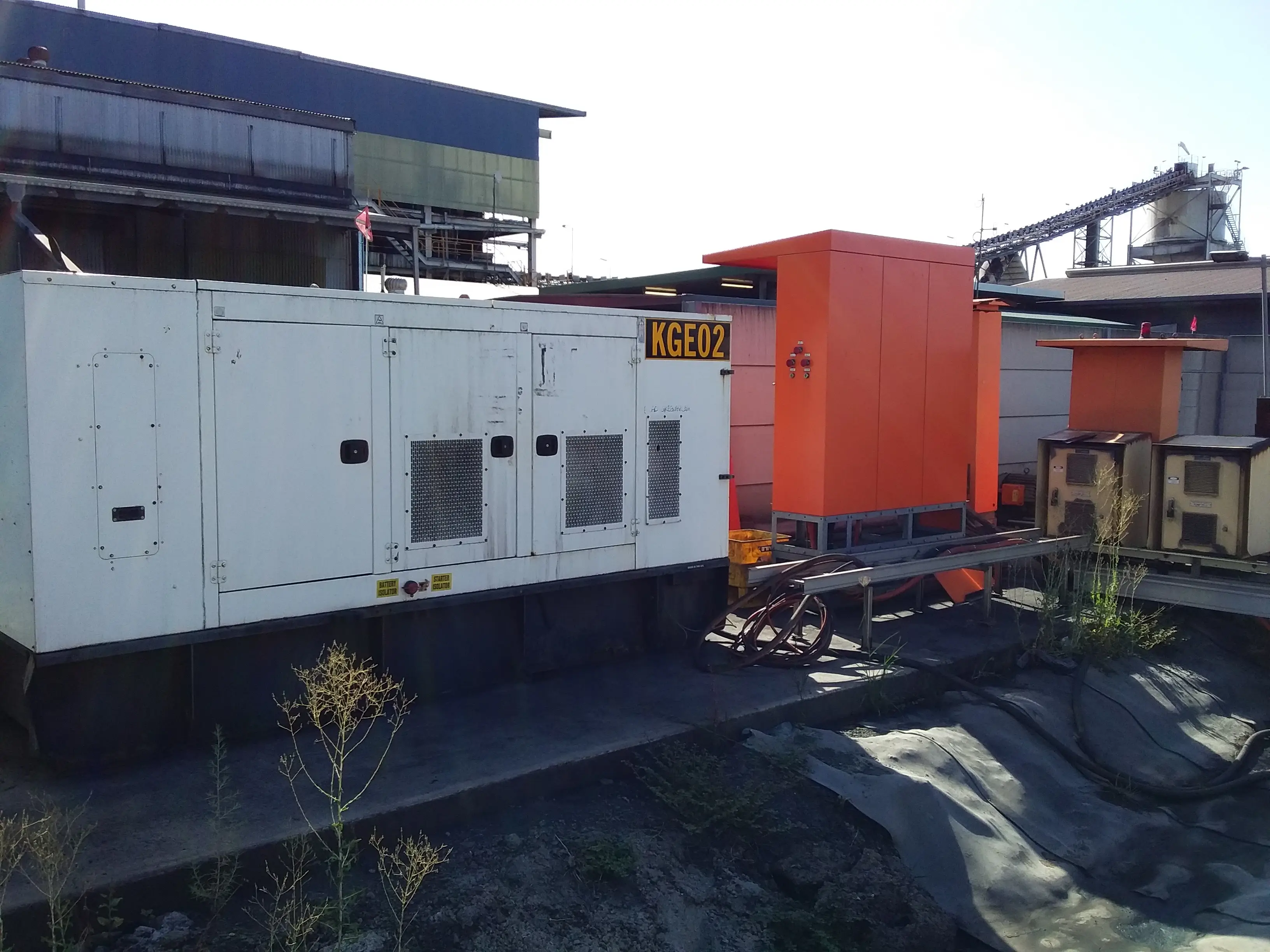
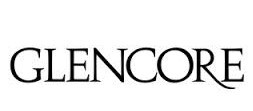
Main Sub Upgrades
The main substation at Glencore’s Oaky Creek Coal is essential for surface operations. Site personnel had highlighted multiple projects for implementation to collectively improve the integrity and reliability of the main sub. For each of the projects there were common elements and beneficial outcomes for executing them concurrently.
Given the critical nature of the projects and the importance of success, Orana Engineering developed a project management and design scope for provision of a dedicated Electrical / Control Systems Engineer from its Engineering Team.
Projects under the scope consisted of safety and reliability upgrades for OCC Main 66 / 11kV substation including automated racking of circuit breakers, interlocking of transformer tap changers and parallelling control, cable pit sump pump control.
Work undertaken included detailed design, PLC and DCS configuration, protection relay configuration, racking controllers, and commissioning whilst also mananging the client's drawing management system.
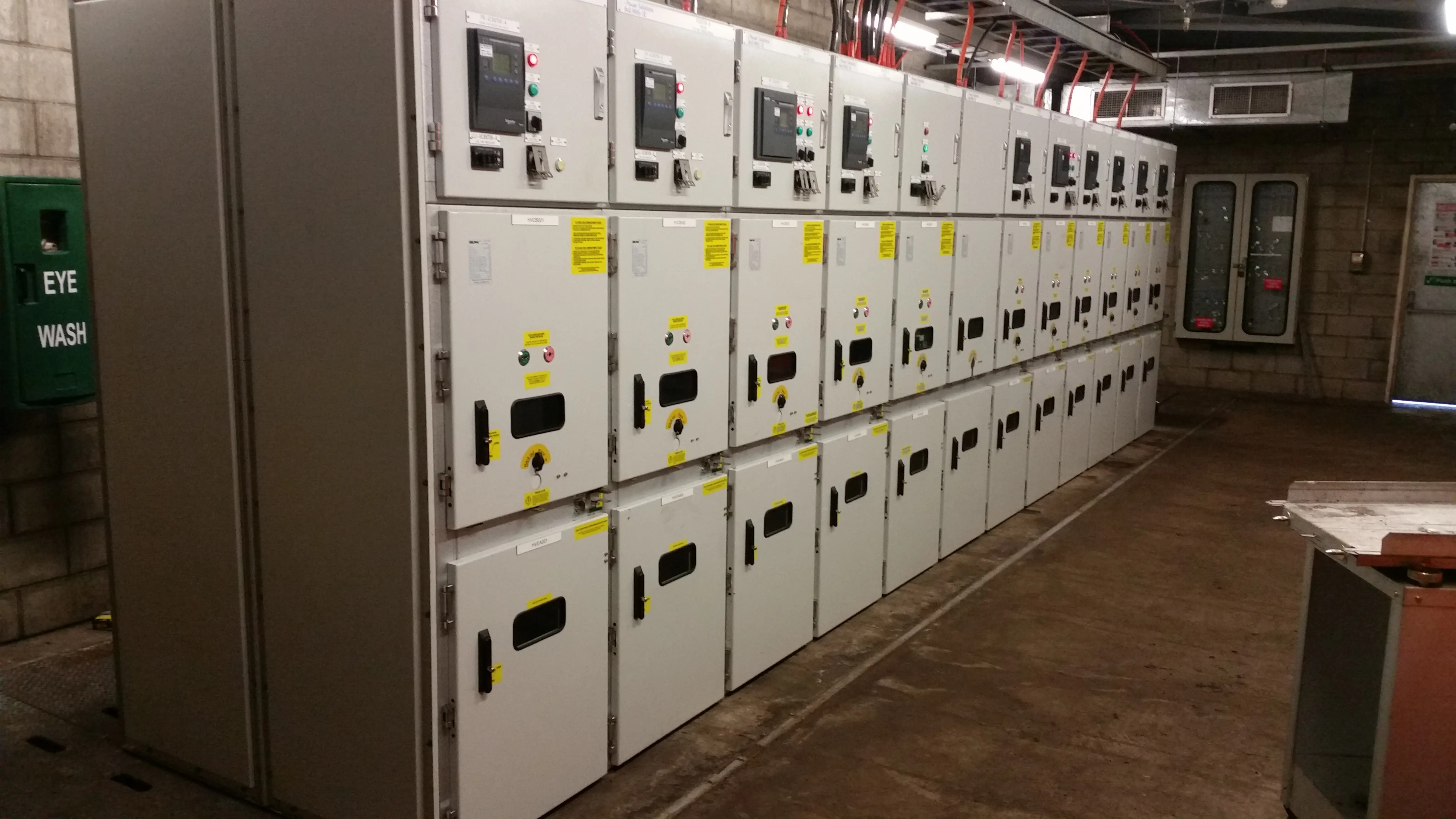
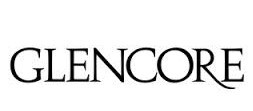
Conveyor Counterweight Design
Orana Engineering was approached by Glencore’s Oaky Creek Coal CHPP personnel to supply a cost estimate for development of modified winch systems for its CV15 and CV16 take-up towers.
The scope of work included provision of mechanical, structural and electrical engineering and design drafting for inclusion of electric take-up winches to facilitate lowering of conveyor counterweights during maintenance activities.
Structural and civil checks were conducted to account for expected force changes caused by additional sheaves and electrically driven winching effects on the structures when compared to the existing gravity take-up applications. The installation was configured and commissioned into the DCS control system by Orana Engineering's control systems engineers.
In addition to mechanical and electrical detailed design drawings, Orana Engineering provided equipment recommendations and specifications, bill of materials and a Safety In Design Report upon finalisation of the design development cost estimate.
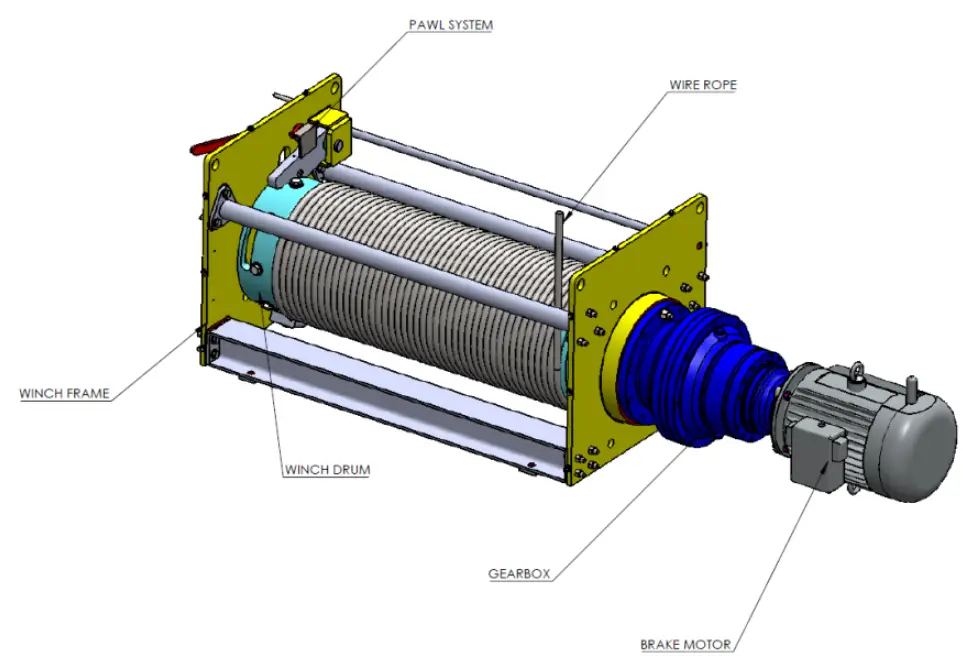
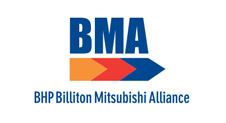
Reagents Tank Farm Rectification
Due to the existing system not being compliant to site standards, BMA Saraji Mine had constructed a new reagents system for the supply of diesel and MIBC into their CHPP. Following construction, several attempts were made to wet commission the system however these were unsuccessful due to multiple problems identified by the client.
Orana Engineering was requested to undertake a complete design review of the reagents system, to outline problems with the design and to provide a scope of work to rectify these such that wet commissioning could be completed.
At the conclusion of the review a bill of materials for the commissioning scope of work was provided, detailing procurement specifications for required mechanical equipment and spares.
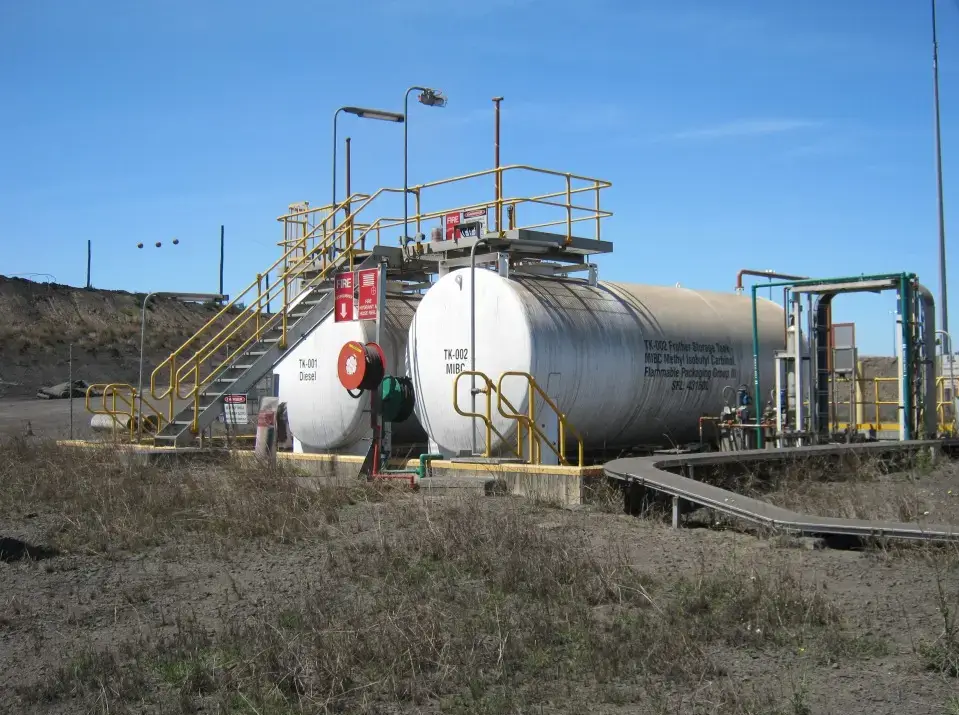
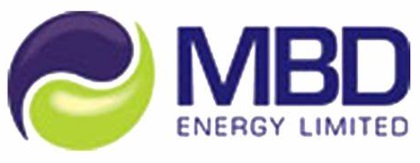
10M TAGS Sled
At James Cook University, MBD Energy operates a research facility investigating methods of cultivating and harvesting algae. To facilitate greater control of the algae agitation sleds, Orana Engineering was engaged to design and commission mechanical, electrical and control systems that would enable agitation sled velocity and frequency of travel to be automated.
The system was designed and implemented by Orana Engineering utilising Allen Bradley Powerflex VVVF drives and a Controllogix’s PLC with an RSView SCADA interface.
Orana Engineering was able to help MBD Energy improve the efficiency and quality of their research results by providing technical knowledge and assistance through our control systems, electrical engineering and mechanical engineering services.
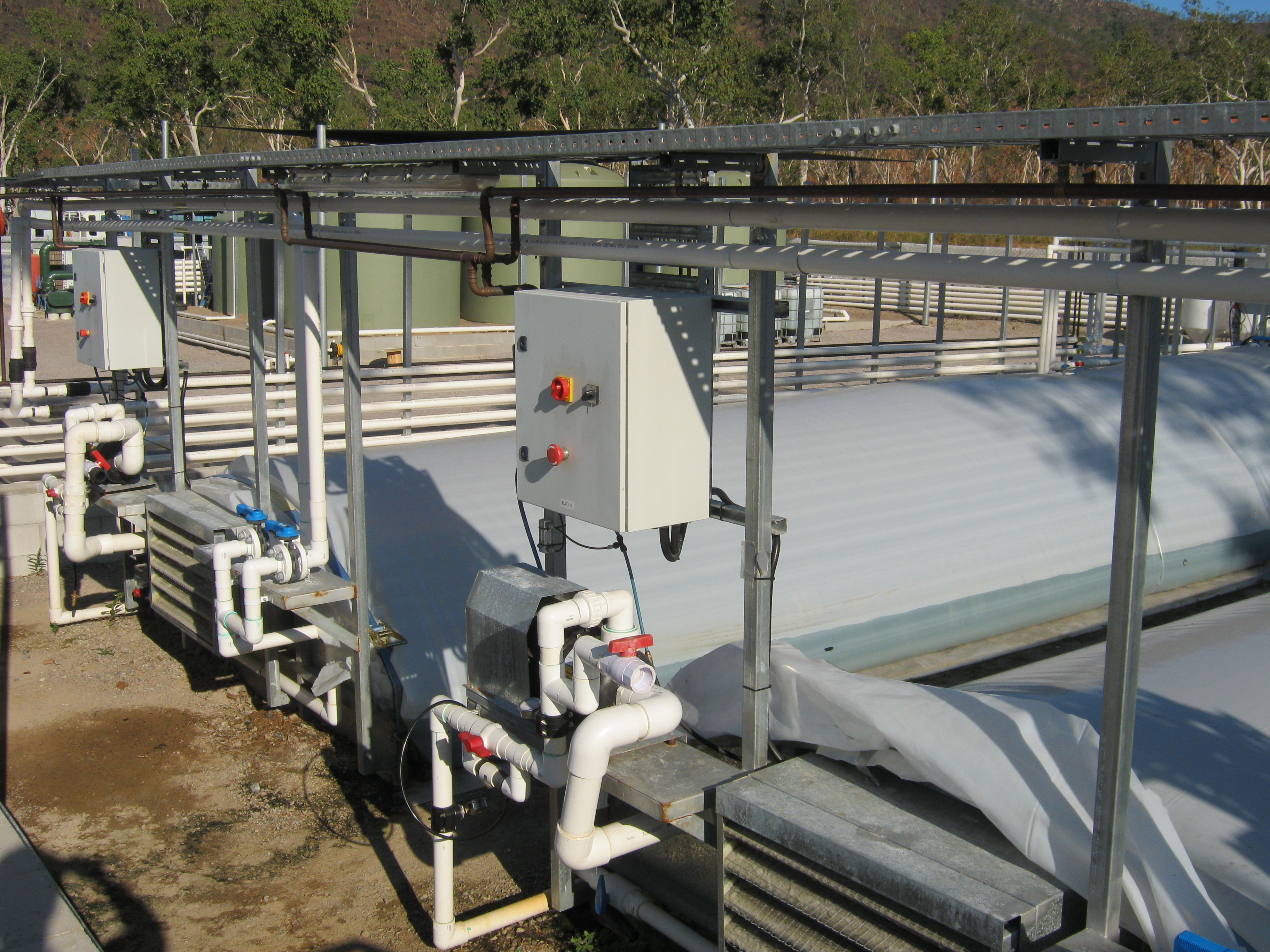
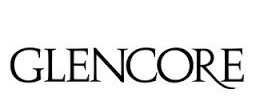
22M Flyover Conveyor
Oaky Creek Coal engaged Orana Engineering to perform electrical and control system design aspects of a 22M Flyover Conveyor to provide an interface between two existing conveyor systems.
Orana Engineering’s brownfield engineering expertise was drawn upon to resolve complexities in interfacing two different coal streams, powered from separate substations and controlled from independent process control systems. Should one system need to be shutdown it was necessary that the other system was not impacted.
The electrical engineering scope included powering the conveyor and transfer systems and providing lighting designs and power distribution. Control system engineering included selection and specification of instrumentation, specification of control system hardware and development of a functional specification.
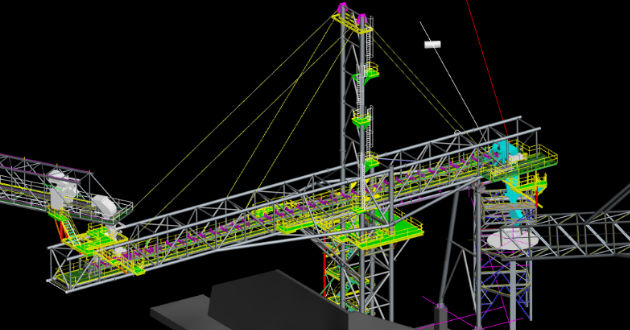
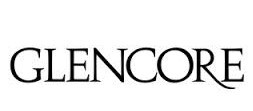
MIBC & Diesel Upgrade
The purpose of the Reagent System Upgrade at Oaky Creek was installation of new reagent storage tanks, discharge / delivery pumping systems and automated flow control distribution manifolds for the delivery of each reagent to the nominated process connections.
Orana Engineering performed mechanical, electrical and control systems design, drafting and engineering for the project. The primary deliverables included scope of works, construction drawings, functional specification, BOM, spares lists and equipment / instrument data sheets.
Orana Engineering managed the onsite commissioning of the system and provided a system handover to operations for implementation. An Operation & Maintenance Manual and Hazardous Area Dossier were provided on project completion.
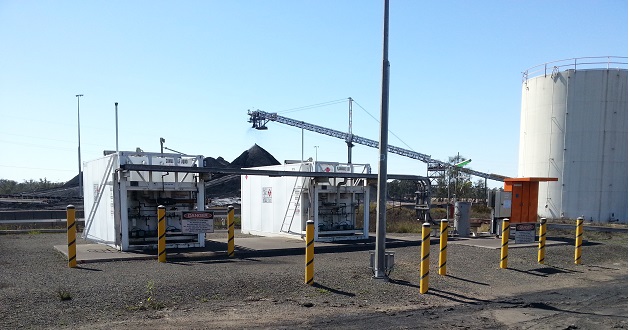
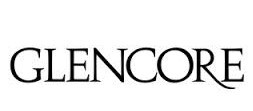
Onsite Accommodation Camp Services
Orana Engineering was engaged by Oaky Creek Coal to assist in design and construction of onsite camp accommodation, including an HV substation for power and potable water supply.
The brief included mechanical, electrical and control systems design, drafting and engineering for the project. Deliverables included scope of works, construction drawings, functional specification, drawing and equipment registers, commissioning and operating spares lists and equipment and instrument data sheets.
Orana Engineering provided PLC configuration and commissioning assistance for pump control, acted as Client Representative during construction, managed onsite commissioning of the system, and provided a handover to operations for implementation.
Operation & Maintenance Manuals for potable water storage and the HV substation were provided upon completion.
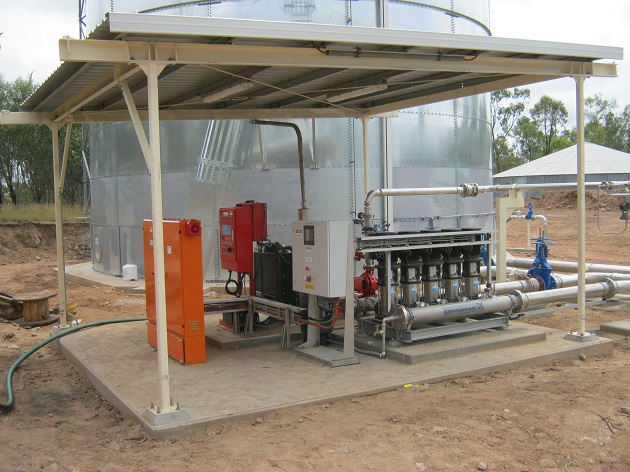
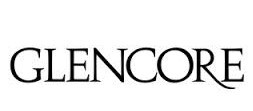
Sewage Treatment Plant Refurbishment
To increase productivity and maintain compliance with legislative standards, Glencore Oaky Creek Coal employed the services of Orana Engineering to design and manage the electrical aspects of an upgrade to their existing sewage treatment plant.
The project was managed on-site by others, with Orana Engineering providing electrical engineering, design, project management and construction / commissioning assistance.
Upon completion of installation, Orana Engineering updated all drawings to reflect any changes made, thus providing Glencore Coal with as-built drawings which will make any future maintenance or fault-finding work more efficient and cost effective, as well as providing legislative compliance.
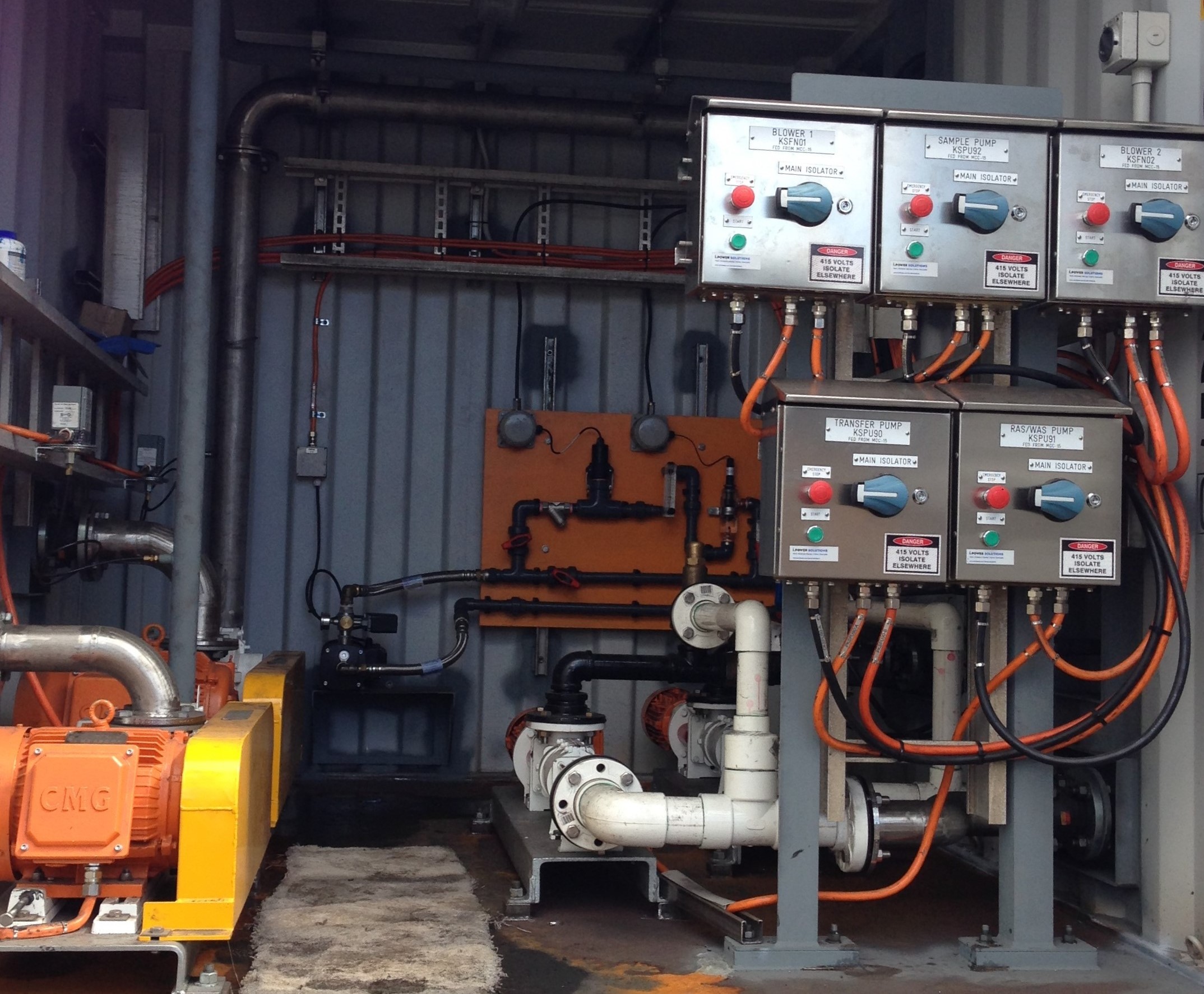
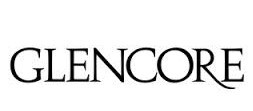
Site DCS Support
The CHPP at Oaky Creek Coal utilises a Yokogawa Distributed Control System for control and monitoring of their operation. The system incorporates Yokogawa’s OPC server and Exaquantum data historian. OCC utilises multiple Programmable Logic Controllers for specific operational purposes, with a number of PLC's interfaced back to the DCS for control and monitoring functions.
Since 2005, Orana Engineering has provided 24/7 support for Oaky Creek’s control system. Day to day support is provided by remote access, which is cost effective and highly responsive. Additionally, onsite support for hardware solutions and commissioning of larger projects is provided as required.
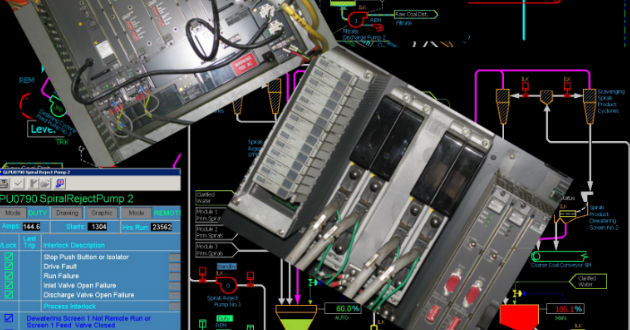
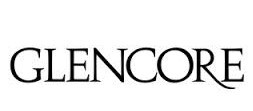
Yokogawa DCS Upgrade
Since 2005, Orana Engineering has provided 24/7 support for Glencore's Oaky Creek Coal control systems. At the CHPP a Yokogawa DCS installed in 1998 is used as the primary control system. With existing CentumCS Unix software no longer supported by Yokogawa, it was essential to complete an upgrade to the CentumCS3000 system.
Orana Engineering developed conversion tools to allow configuration data to be extracted from the CentumCS Unix platform and imported into the CentumCS3000 environment. These tools provided efficiency and accuracy for the conversion and delivered a significant cost saving.
The quality of conversion tools and simulation programs developed by Orana Engineering resulted in highly efficient site commissioning, completed without plant downtime.
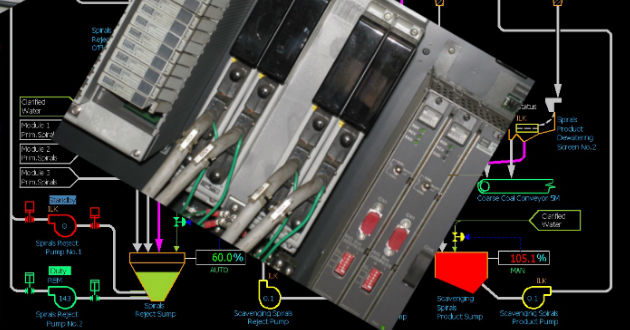