Project Management
At Orana Engineering, project management is about delivering high quality outcomes for our clients. Our experienced Project Managers co-ordinate all aspects of a project to ensure the client’s targets are consistently achieved. Managing the core elements of cost, quality and schedule, successful project management realises the right balance and manages conflicts between each one.
Also of great importance for successful project management is the understanding of the client’s needs and expectations. Orana Engineering’s Project Managers have a unique skillset to draw upon with their combination of site experience, practical backgrounds and engineering qualifications allowing them to truly understand our clients' needs and expectations and create outcomes that align with this, meeting all key HSEC, quality assurance, cost and schedule targets throughout the process.
In the role of Project Manager, Orana Engineering has the experience and resources to:
- Co-ordinate various work groups and organisations;
- Schedule and co-ordinate regular meetings;
- Manage project variations;
- Promote and enforce client HSEC requirements;
- Prepare and track project schedules;
- Communicate project matters to all relevant parties;
- Schedule permits and outages;
- Prepare project reports; and
- Track budgets, budget forecasting and cost control.
Engaging our project management services ensures that all aspects which effect the delivery of a project are the responsibility of our Project Managers, including resolving commercial issues, tendering and liaising with subcontractors, risk management and HSEC issues, commissioning and handover. Personnel have access to a wide range of tools, procedures and processes that have been developed and refined by Orana Engineering to ensure effective cost estimation, management of budgets and change management.
Our project management services are of value throughout all stages of a project, from concept design through to detailed design, construction and handover. An experienced Orana Engineering Project Manager adds value to a project by:
- Dedicating a resource to manage the project, freeing up the time of the client so they can focus on the day to day operational issues;
- Allowing clients to remain informed and be in control of the project without having to dedicate time to managing the details;
- Providing the potential to achieve the highest quality outcome by engaging a practical Project Manager that has the time, expertise and experience to do the job right. Orana Engineering’s Project Managers are skilled engineers with hands on site experience;
- Seamlessly integrating additional services as required such as Client Engineer, design drafting, drawing revisions and drawing management giving clients one point of contact for any mechanical, electrical, structural or control systems engineering services requirements; and
- Offering the confidence of an experienced project management service with a proven track record.
An added advantage of being a smaller organisation is that for larger projects (i.e. >$2.5M), we can act on behalf of the client in the role of Project Manager and/or Client Engineer without a conflict of interest, as Orana Engineering do not tend to pursue design works for larger engineering projects.
Orana Engineering has a proven track record ensuring outcomes are consistently achieved and has project managed projects with values in excess of $20M. Our reliable Project Managers are technical experts and bring a depth of knowledge and experience to every project.
Contact Orana Engineering for further information about our project management services or to request a no obligation proposal. Our Capability Statement is also available for download providing more information about the services Orana Engineer offers.
Orana Engineering Project Management
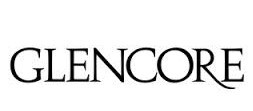
UG Conveyor Installations - MG Mechanical Installation
Detailing the installation of mechanical equipment and conveyor structures is one of the final steps for completing a maingate drive-head design. Installations designed by Orana Engineering for Glencore’s Oaky No.1 underground coal mine included detailing drive arrangements, transfer stations, take-up units, maintenance equipment and the overhead structures supporting the carry belt.
Mechanical design must consider a number of factors, including meeting the required operating capabilities, allowing for unimpeded access along travel roads and maintaining minimum belt curves. Often equipment is relocated from previous installations with minor modifications in transfer angle and number of drives. Orana Engineering has developed unique methods for completing this type of design, enabling us to keep total costs down for our clients.
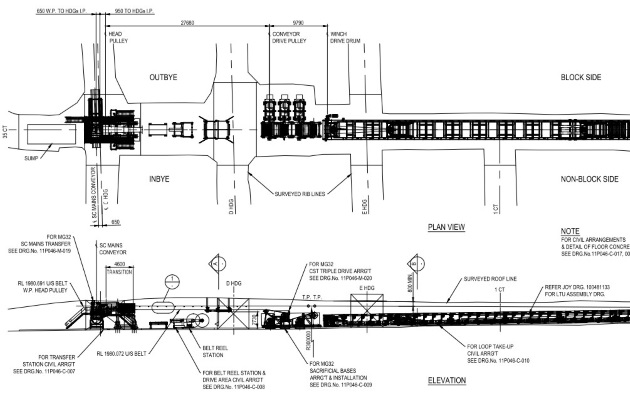
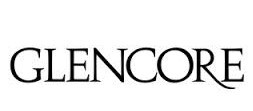
Village Kitchen Upgrade
The Village Kitchen at Glencore’s Hail Creek Mine camp was scheduled for upgrade with Orana Engineering engaged to provide engineering support for electrical, civil and building works, including a new shed. A site visit was conducted to determine the scope of the upgrade and to collect site information comprising photos, drawings, measurements and location of water and gas services.
From the information gathered, Orana Engineering provided engineering design and project management of the Village Kitchen upgrade including a new shed distribution board, concrete slab, layout and connection of services to the new shed and prepared a detailed scope of work document for tendering purposes.
Orana Engineering design drafters produced RPEQ certified GA and concrete drawings showing details of services to be relocated, a slab and loading dock drawing, a new single line diagram for the distribution board, and revisions to existing distribution board drawings.
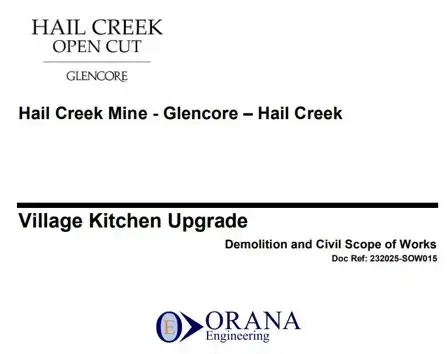
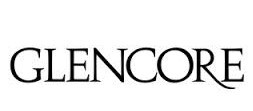
Rajant Network
Glencore planned to install the CAT MineStar Terrain Office system at its Oaky Creek Coal Mine to support GPS positioning and live maps in CHPP stockpile dozers. As part of the upgrade, mine infrastructure and dozers required hardware installation to connect the dozers to the site network and enable communication with MineStar servers. In line with other Glencore sites, it was chosen to implement a Rajant wireless network to cover stockpiles and provide connectivity between dozers and the network.
Orana Engineering was engaged to provide electrical and Operational Technology (OT) engineering design, configuration and drafting support for the CAT MineStar GPS implementation including preparation of three new virtual servers for various applications. Orana Engineering electrical engineers developed a scope of work which provided an overview of the onsite electrical installation works required to be carried out by others with supply, installation, testing and commissioning project managed by an Orana Engineering electrical and control systems engineer.
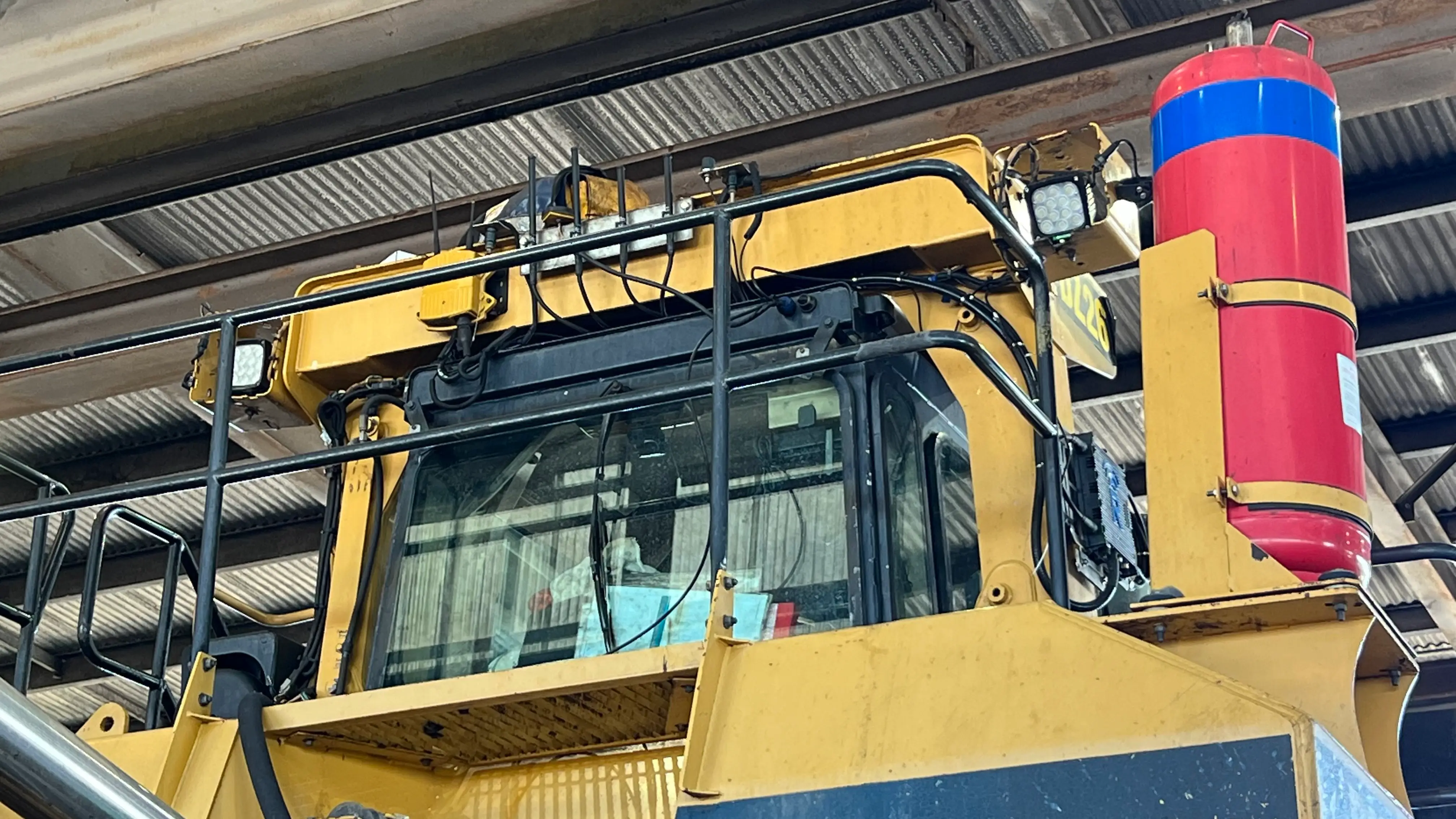
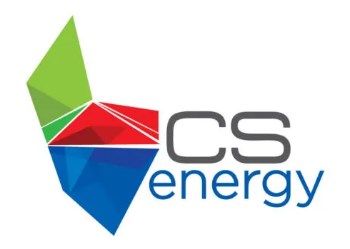
Ash Water Return Pipeline Replacement
Ash slurry at CS Energy’s Kogan Creek Power Station is pumped to various locations around site via a pipeline originally installed for delivery of service water from the power station to the crusher area. With proposed pumping equipment capable of higher pressure output, a project was set up to review the engineering calculations and potential risks.
Orana Engineering was engaged to conduct concept design investigations considering options for repair or replacement of the pipeline. Outcomes from the review were provided to CS Energy summarising options considered and proposing the use of carbon steel (potentially lined for corrosion resistance) as the optimal replacement for fibreglass piping. Advantages and disadvantages of carbon steel were also presented such that the client was fully apprised of its properties.
As only limited drawings of the existing pipeline were available, Orana Engineering design drafters produced pipeline general arrangements for information.
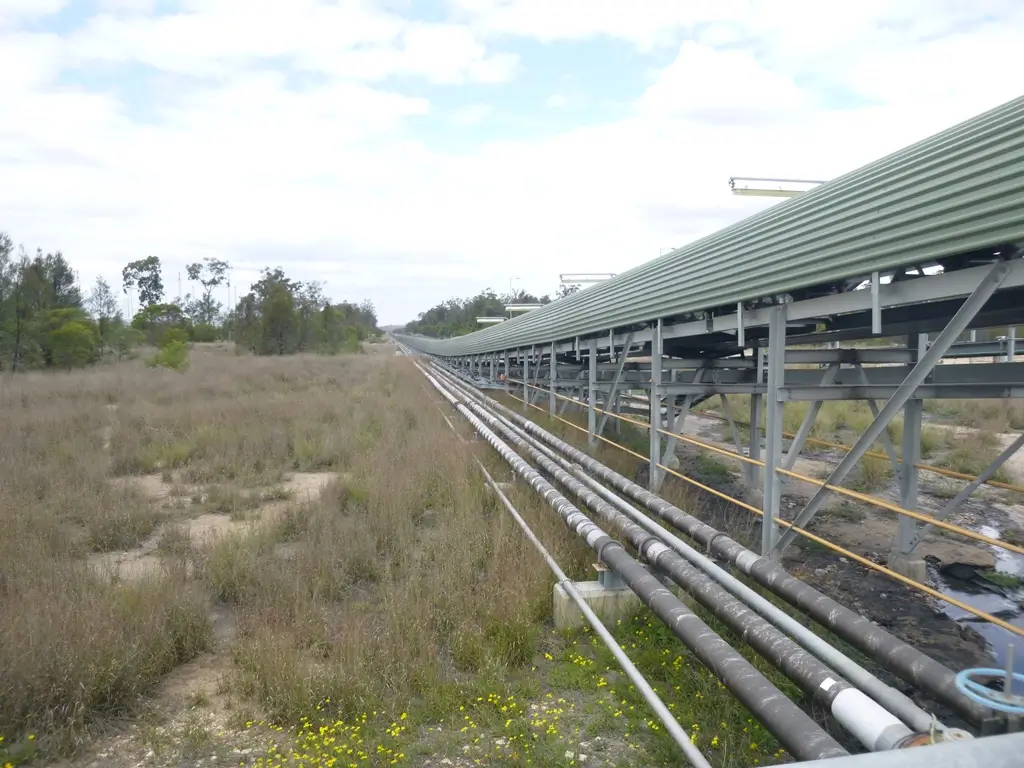
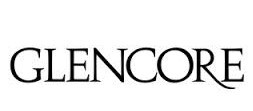
TLO Bin Support Repairs
Orana Engineering assisted Glencore's Clermont Coal with an engineering review of the structural integrity of head end support stools connected to its train load-out (TLO) bin ring beam as material build-up at the top of the bin cone had resulted in corrosion of several lower stools connected to the ring beam. Orana Engineering presented recommendations for temporary stiffening solutions and a repair methodology to restore conveyor supports to original design capacity.
Following the initial review, Clermont Coal requested that Orana Engineering undertake a further structural review of the TLO bin to analyse the effect of scaffold arrangements to be constructed on the bin and to confirm overall structural integrity with the additional applied loads.
Orana Engineering design drafters developed a concept design 3D model of proposed bracing including finite element analysis (FEA), and RPEQ certified detailed drawings for TLO column repairs were also delivered to the client.
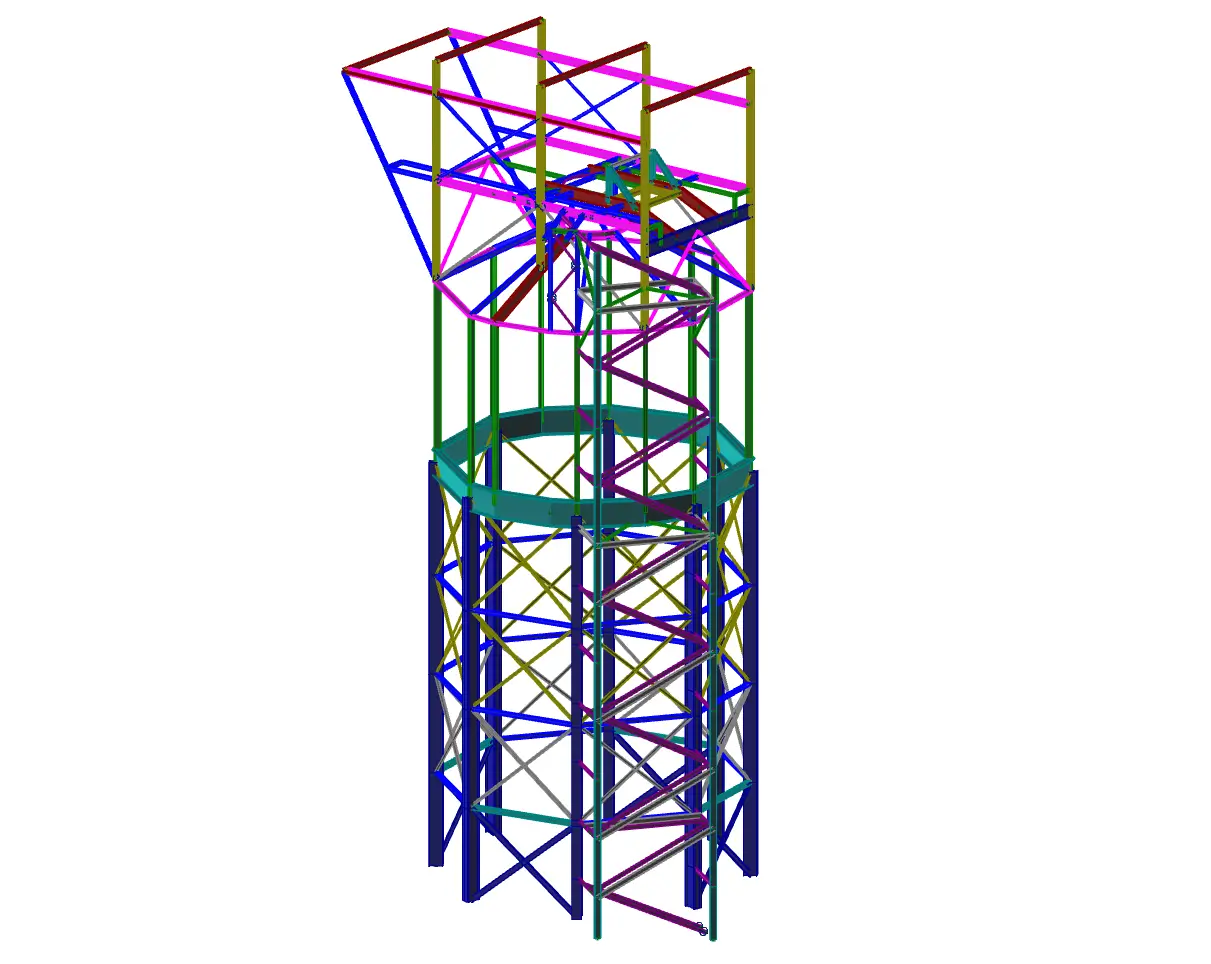
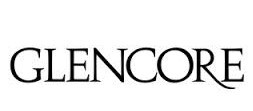
IBC Stand for Pump Suction Height
Glencore’s Hail Creek Coal Mine engaged Orana Engineering to develop the engineering design for a stand to elevate a 1,000 litre IBC from ground level, enabling the content to gravity feed to the pump suction during a major upgrade project.
Design considerations by Orana Engineering included the process and materials relevant to the IBC location, raw material requirements and painting specifications based on site standards, positioning and fit of the IBC with existing equipment and infrastructure once elevated on the stand. Height requirements for gravity feed to pump suction connection and allowance for differential grouting of feet to account for concrete falls were also taken into account.
Orana Engineering design drafters generated a 3D model of the proposed design using AutoCAD Advance Steel for client review before developing a Navisworks Model of the IBC stand and completing engineering checks for load.
Final deliverables to the client included arrangement and fabrication detail drawings of the stand with RPEQ supervision.
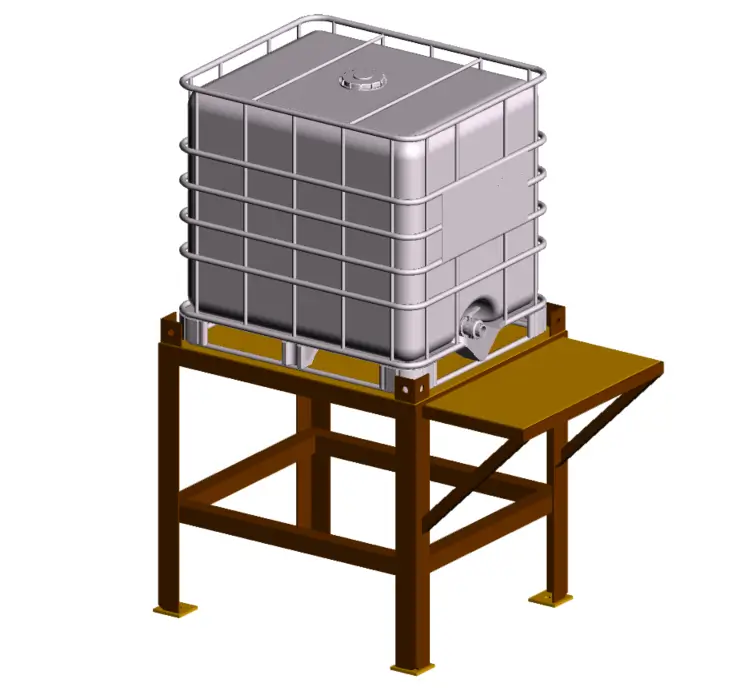
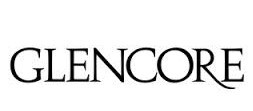
Light Poles Review
Orana Engineering was contacted by Glencore’s Oaky Creek Coal Mine to undertake a structural review of lighting towers situated at the Tieri township sporting oval. Existing tower bases had been buried for approximately 20 years and were displaying evidence of corrosion to anchor bolts and baseplates.
Orana Engineering conducted a review of client-supplied documentation and photographs and gathered additional information to determine repair requirements. Following the review, a letter of recommendation was provided to the client outlining repairs required for continued operation of the lighting towers, with RPEQ structural supervision.
Additional support was provided by Orana Engineering with a further review of lighting towers within the Tieri Aquatic Centre and Shopping Centre. In this instance Orana Engineering was also able to capture 3D data from light poles using its Faro 3D laser scanner. The client was presented with recommendations for tests or further analysis required.
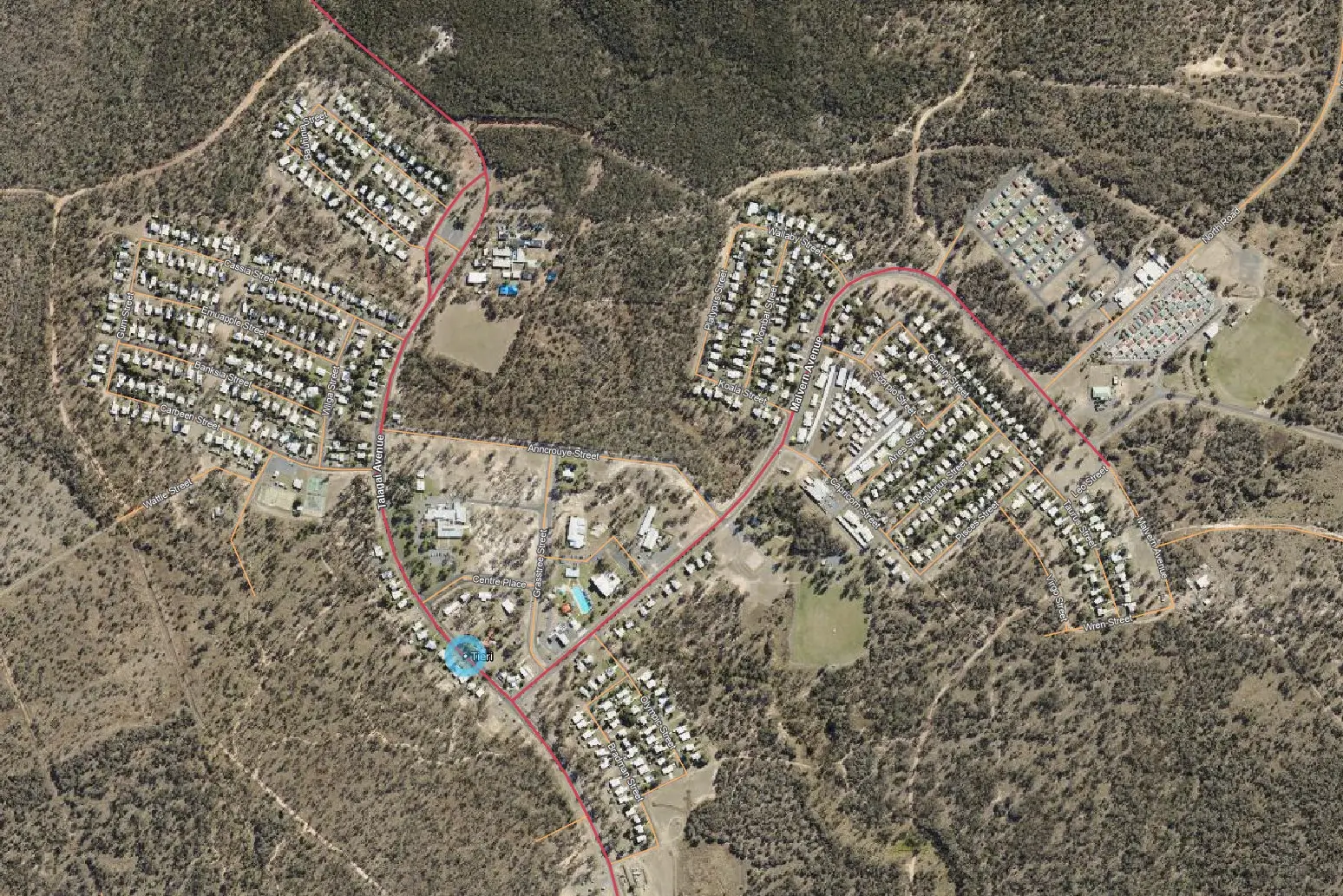
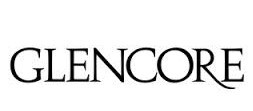
Filter Press Installation
A filter press initially planned for Glencore’s Clermont Coal Mine was relocated for installation at Collinsville Coal Mine in a trial capacity to assist in reducing the amount of tailings produced from the wash plant.
Orana Engineering was engaged to provide engineering and drafting support for the filter press installation scope of work, to assess suitability of the Clermont detailed design for construction at Collinsville and to plan and implement arrangements for the installation.
Considerations to ensure a smooth installation at Collinsville included concrete design and a structural analysis. Calculations were also undertaken to determine design wind and earthquake loads for the site to Australian Standards AS/NZS1170.2 and AS1170.4.
Orana Engineering design drafters produced a new site plan showing set-out of the filter press slab with new and existing underground services detail incorporated, with RPEQ Supervision.
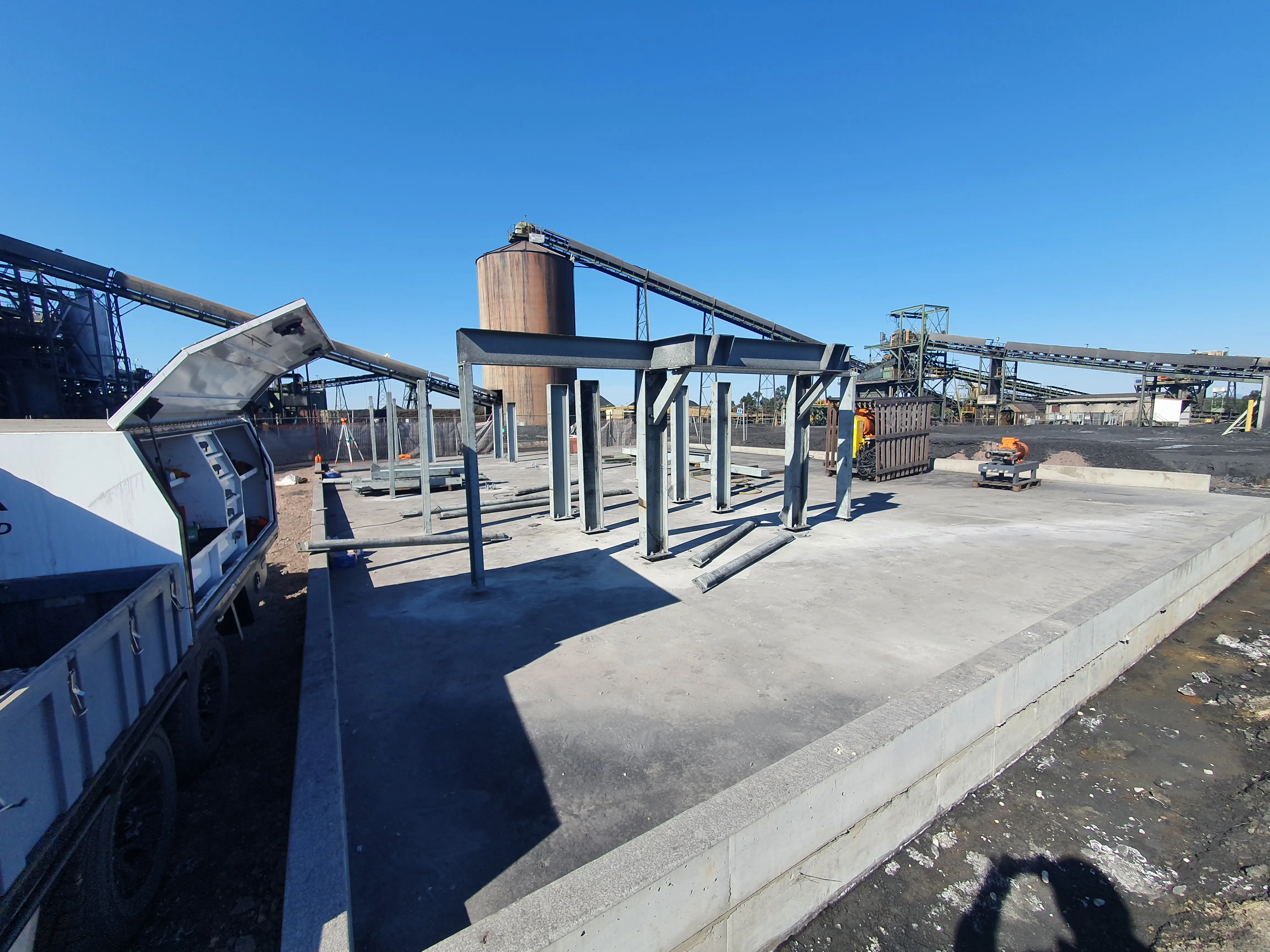
.jpg)
Fire Hydrant Extension
Personnel at Origin Energy’s Darling Downs Power Station contacted Orana Engineering seeking assistance in reviewing regulatory requirements of fire protection systems (detection, alarms, hydrants, emergency exits) relevant to areas of the site not fully protected by existing systems due to distance or obstruction.
Orana Engineering’s design was required to tie into the existing potable water fire line to supply a new fire hydrant / hose reel, while meeting operational fire-fighting requirements compliant with Australian Standards
Orana Engineering completed mechanical engineering, calculations and hydraulic modelling for review by a third party Fire Systems Designer and verification by an RPEQ Fire Engineer. Orana Engineering also undertook pipework design and drafting with RPEQ sign-off.
Deliverables to the client comprised a scope of work document, a testing / commissioning plan, budget estimate cost proposal for installation and building certification, and provision of a drawing set for the fire water extension.
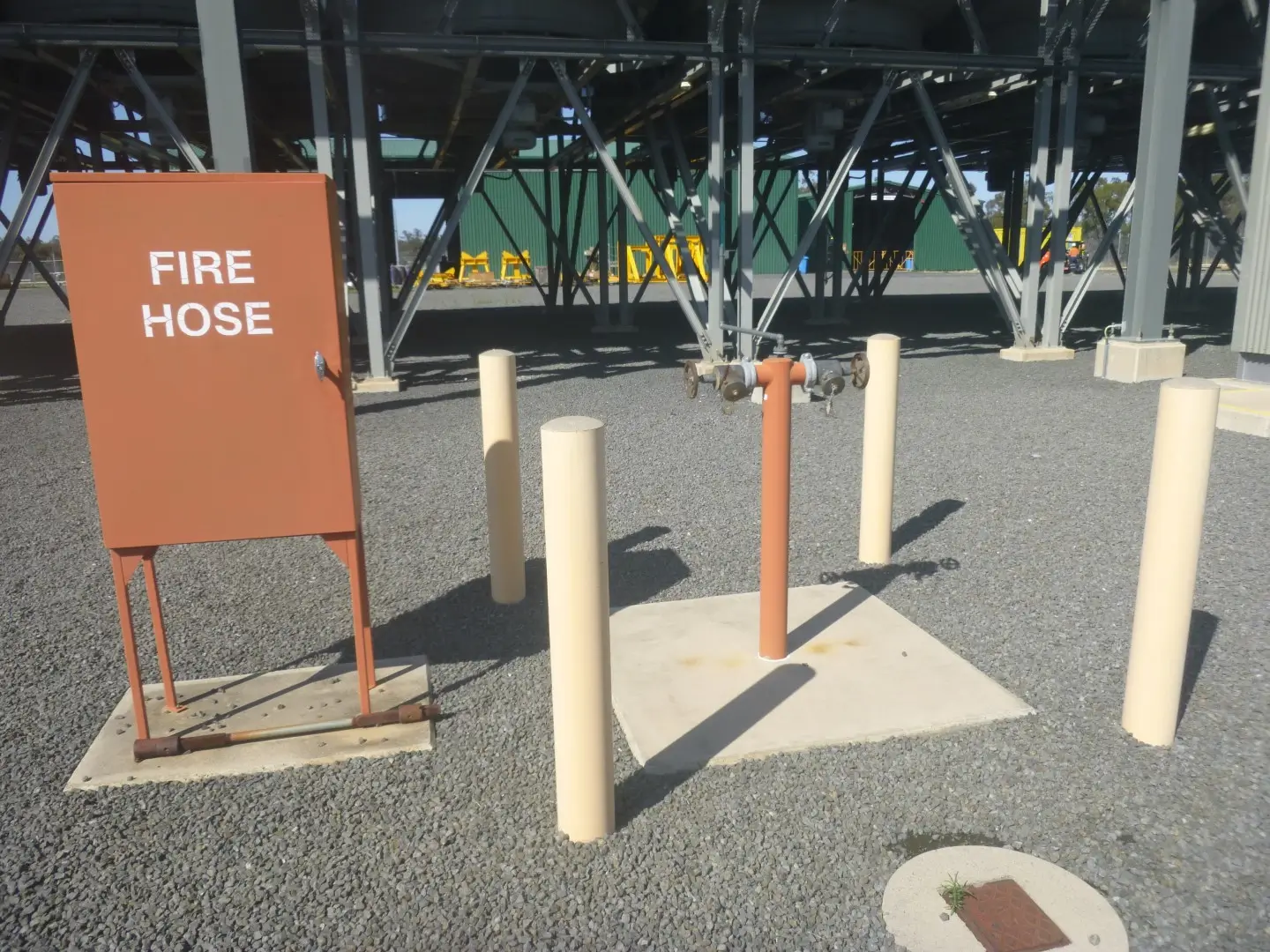
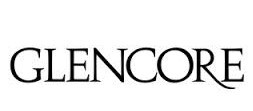
Clarified Water Upgrade
Orana Engineering was consulted by Glencore’s Collinsville mine to assist with an upgrade of its CHPP washdown water distribution system. The CHPP clarified / raw water is supplied from either an anti-pollution pond or the raw water Sunwater pipeline, with the wash water distribution network delivering water to the yard area, CHPP washdown sprays, lime / flocculant dosing or conveyors for spray bars and washdown.
Following hydraulic modelling, Orana Engineering’s mechanical engineers delivered a design with improved flow and pressure, (increasing capacity from 375 to 700 cubic meters per hour) while structural engineers produced SpaceGASS modelling of pipe supports and 3D modelling of the discharge structural steel pipe rack. Additionally, a Functional Specification or Function Description was produced for integration of the design into the plant's control system.
Project deliverables included an Equipment Register, Scope of Supply, detailed Construction and Installation Scope of Work for Tender, Functional Description and detailed design drawings.
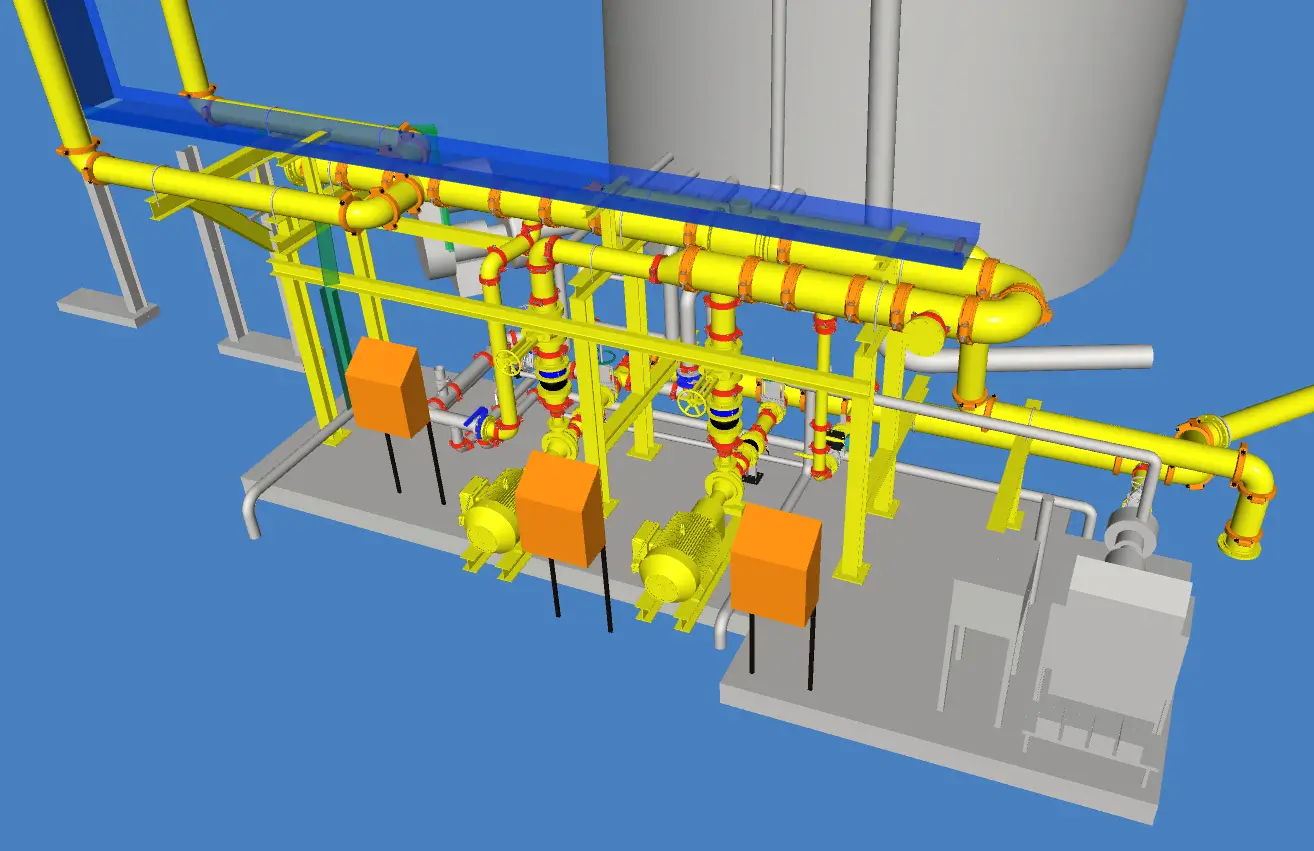
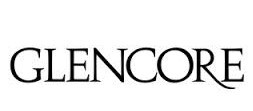
C22147 Water Destruction
Glencore’s Collinsville Open Cut mine utilises sprinklers to partially destroy Acid Mine Drainage (AMD) water generated. Existing sprinklers were effectively moving the AMD water, but at a slow rate. Orana Engineering was contacted for assistance in designing a system to increase the existing sprinkler arrangement from 67 to 200 units, capable of dewatering up to 9.45ML per day, while utilising a minimum of pumps and nozzles.
Orana Engineering mechanical and electrical engineers gathered data and undertook hydraulic modelling in developing a sprinkler design to increase water surface area while decreasing maintenance and failure rates of existing nozzles.
3D modelling of the design was presented to the client along with RPEQ supevised detail design drawings.
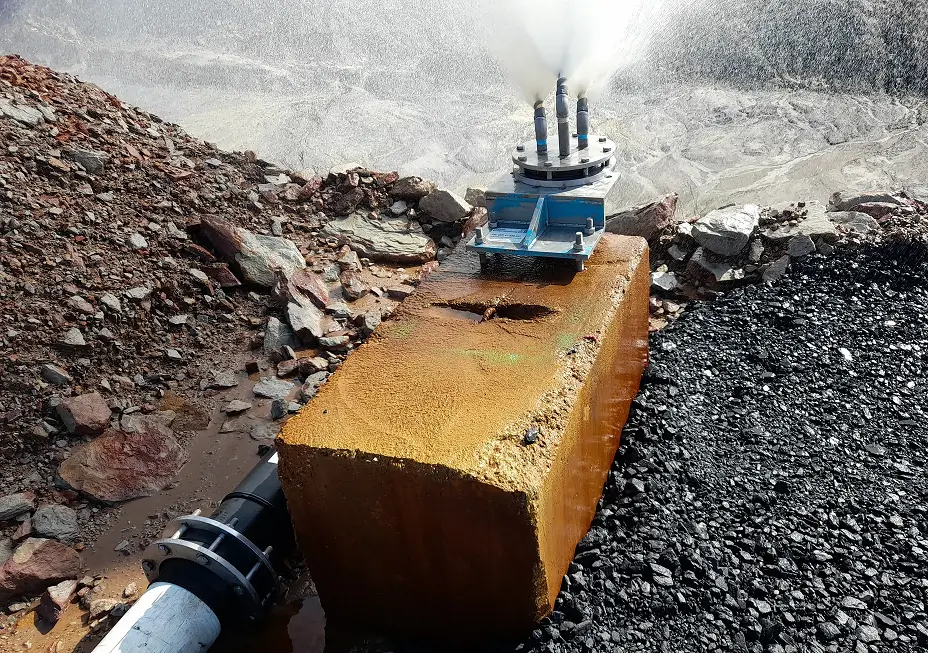
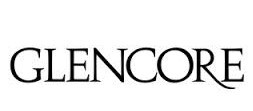
Anti-Pollution Pond Access
At the request of Glencore’s Collinsville Open Cut Mine, Orana Engineering provided a concept design for upgrade of aging infrastructure associated with the sites anti-pollution pond.
Orana Engineering provided a detailed design for installation of permanent handrail and barrier systems along the access pathway to mitigate hazards. The walkway bridge was identified as having inadequate support structure and was included in the proposed design, along with relocation of the existing pump pontoon and level sensors.
Orana Engineering design drafters produced 3D modelling for the installation which was provided to the client along with a general arrangement drawing of the new pontoon access, a fabrication detail drawing of the steelwork support and a civil and access ramp detail drawing, with RPEQ supervision.
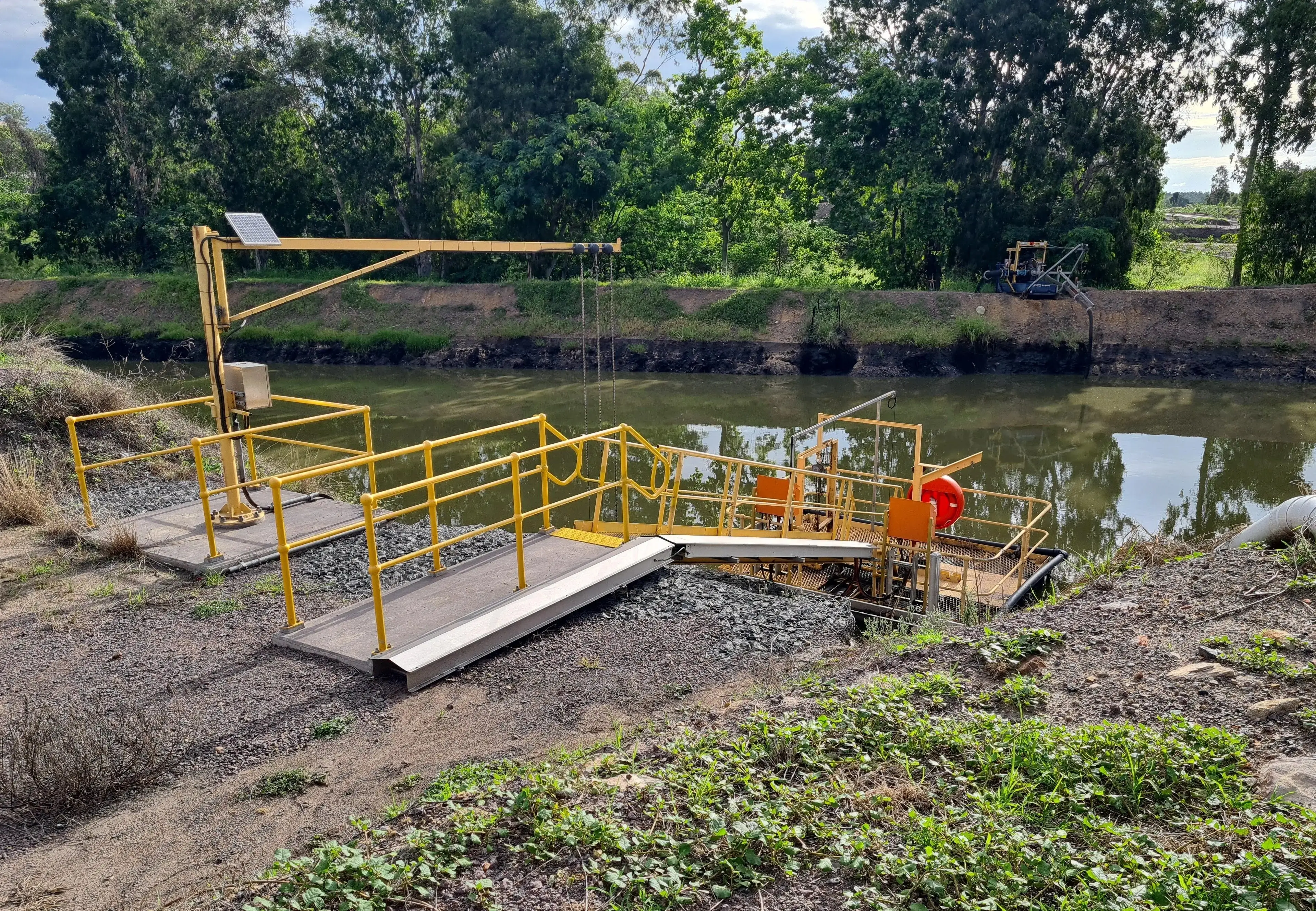
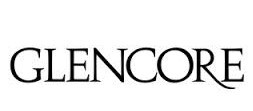
Chain Feeder Modifications
The CPP chain feeder at Glencore’s Clermont Coal Mine required repair and the assistance of Orana Engineering was sought with development of an appropriate methodology and associated detailed design drawings.
Steel plates had been installed to cover the chain feeding system, which over time had been degraded by the dozer feeding the system chipping away at concrete footings. This caused exposure of the steel plate edge which subsequently caught on the dozer bucket. The result was a build-up of material around the chain, causing downtime to reinstate plates and clean up material.
Orana Engineering’s basis of design was for repair of the existing reclaim feeder concrete and development of suitable protection to reduce future wear damage and deterioration from dozer contact. Existing concrete footing drawings were revised to reference new concrete and steel detail and then issued for client review prior to finalising, with RPEQ supervision.
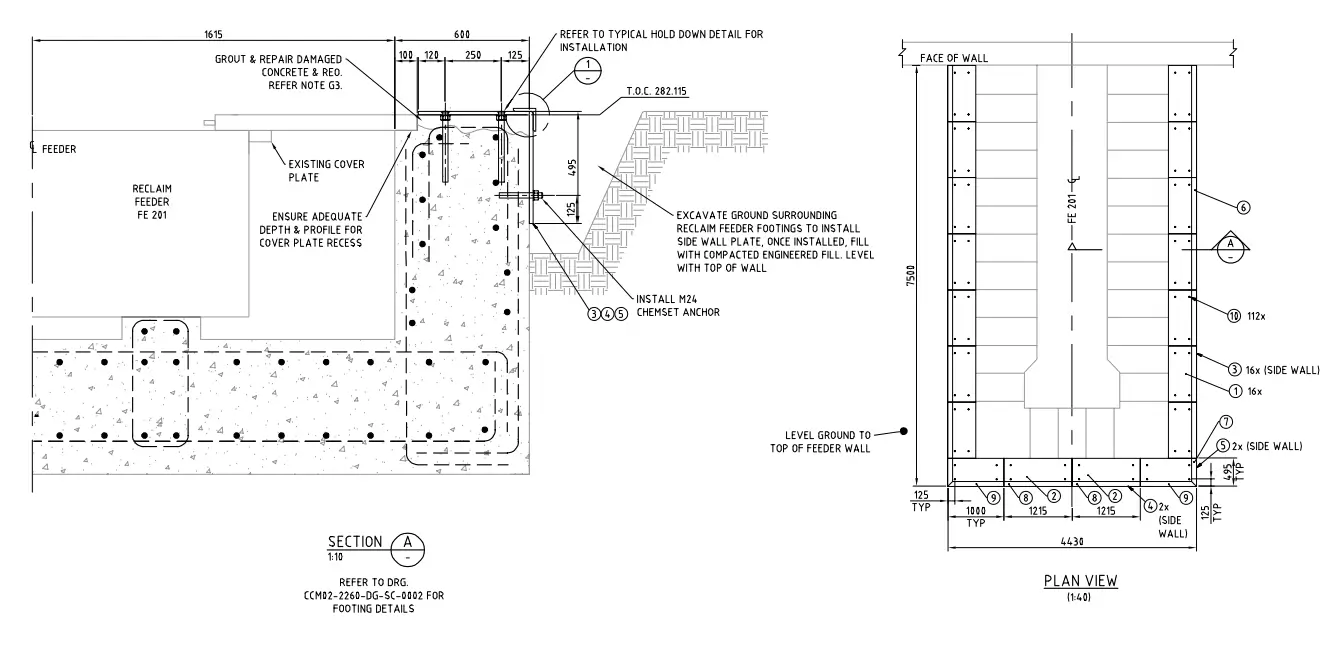
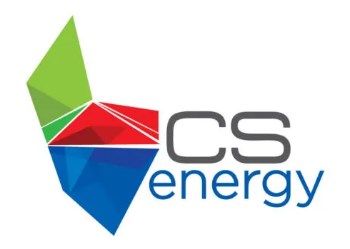
Sewage Treatment Plant Concrete Slab
CS Energy engaged Orana Engineering to provide engineering and drafting support in documenting the scope for onsite civil, electrical (earthing) and mechanical (shade sail and drain piping) supply and installation at its Kogan Creek Power Stations Sewage Treatment Plant.
The basis of design was provision of detailed design engineering of a bunded concrete slab to house two 22kL aerated tanks and a 20 foot container. The slab design was to include an effluent drainage system with a new discharge pipe to be connected to the existing underground wastewater drainage network. It was planned to remove existing tanks and pumps and the design scope prepared by Orana Engineering was to include details for filling and capping the residual drainage pipes and holes.
Design drawings generated by Orana Engineering personnel to support the scope of work included a general arrangement, a detailed drawing and a revised layout drawing.
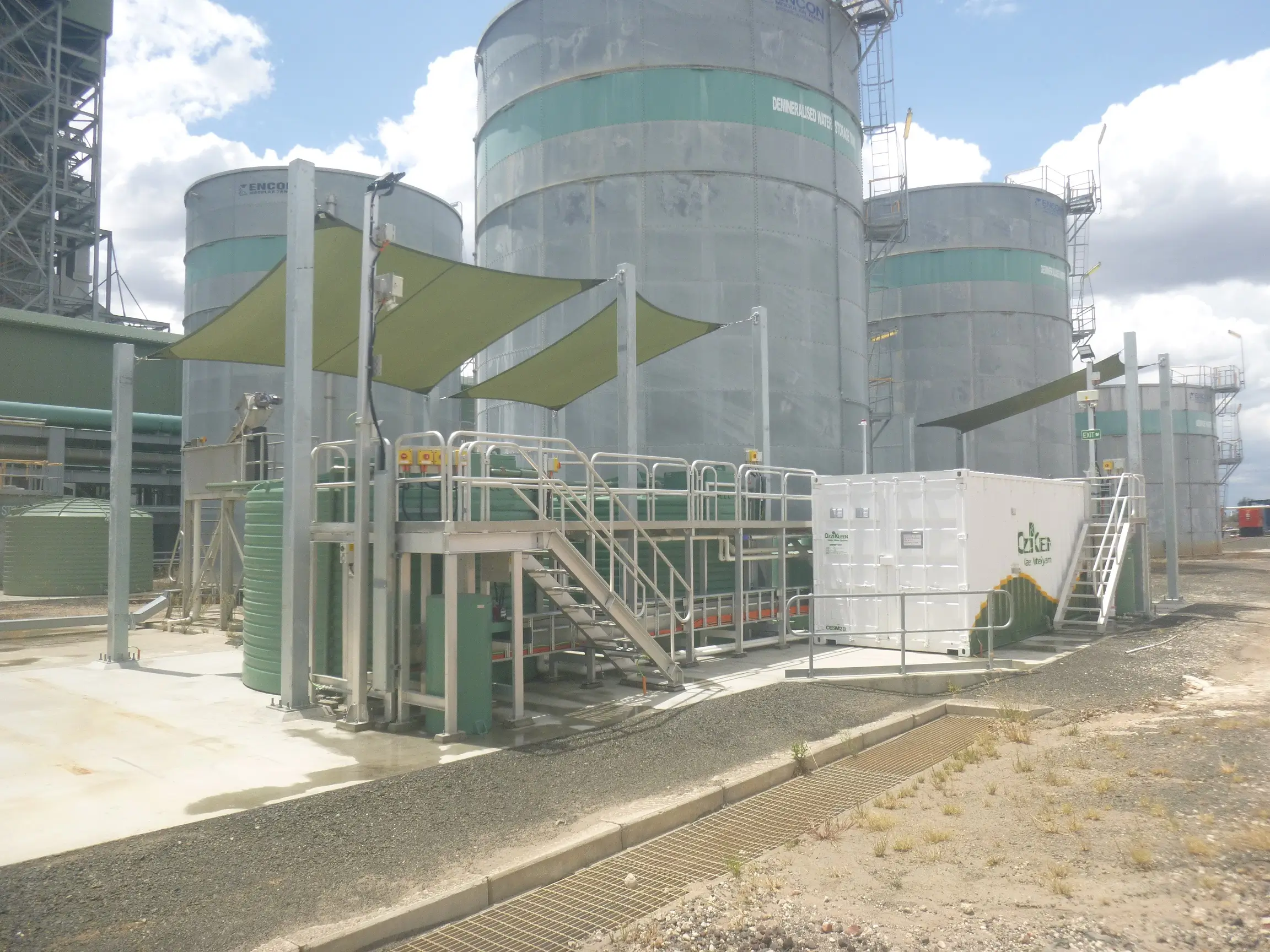
.jpg)
Oily Water Pond
Origin Energy’s Talinga Gas Plant oily water system treats water created during the gas compression process. Effluent from the system is pumped into the water-gathering network, delivering water to the main water treatment plant.
Orana Engineering was engaged by Origin Energy to evaluate the oily water system and conducted a high level assessment of options to reduce the risk of uncontrolled release of contaminated water from the wetlands system that was controlled by interim means.
Outcomes were presented to the client summarising options to reduce or eliminate identified risks. Orana Engineering subsequently provided detailed mechanical and electrical design and drafting for the approved option.
Deliverables for the project included a basis of design document, detailed design and a revison of the Wetland Operations & Maintenance Manual.
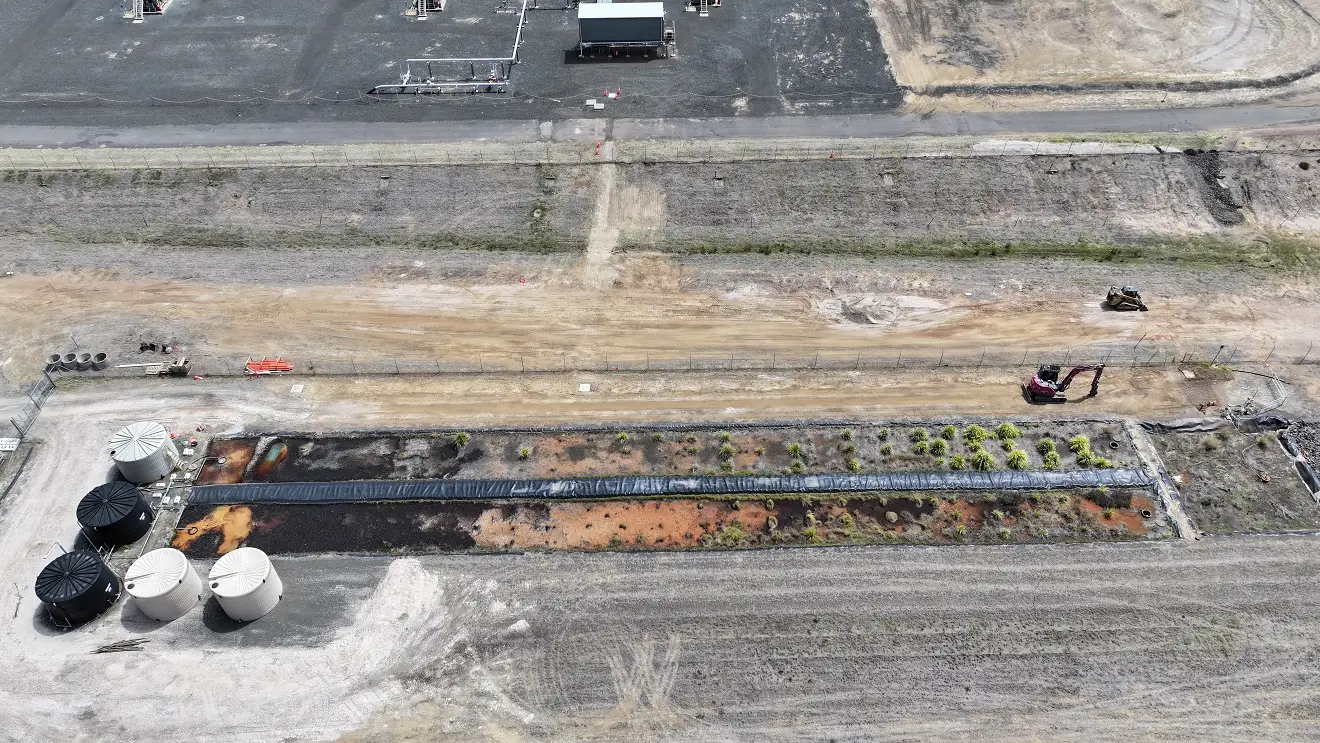
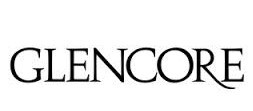
Warehouse Delivery Area
Glencore’s Collinsville Open Cut Mine engaged Orana Engineering for assistance with engineering design of a new concrete slab to allow for driving, loading / unloading of forklifts and delivery trucks at its warehouse building. The design accounted for tie-ins to existing slabs and a surrounding security fence with cantilevered sliding gates on western and eastern sides of the area.
Orana Engineering’s involvement comprised gathering of additional site data and drawings on existing slabs, reviewing geotechnical and ground survey data for conditions in the area, liaison with the client and plumbers etc to confirm area runoff and underground services, as well as engaging vendors of precast concrete barriers, sliding gates and mesh fencing.
Preliminary sketches for client review and discussion were produced by Orana Engineering’s design drafting personnel, followed by concrete general arrangement and detail drawings and a structural detail drawing ‘issued for construction’ with RPEQ Supervision.
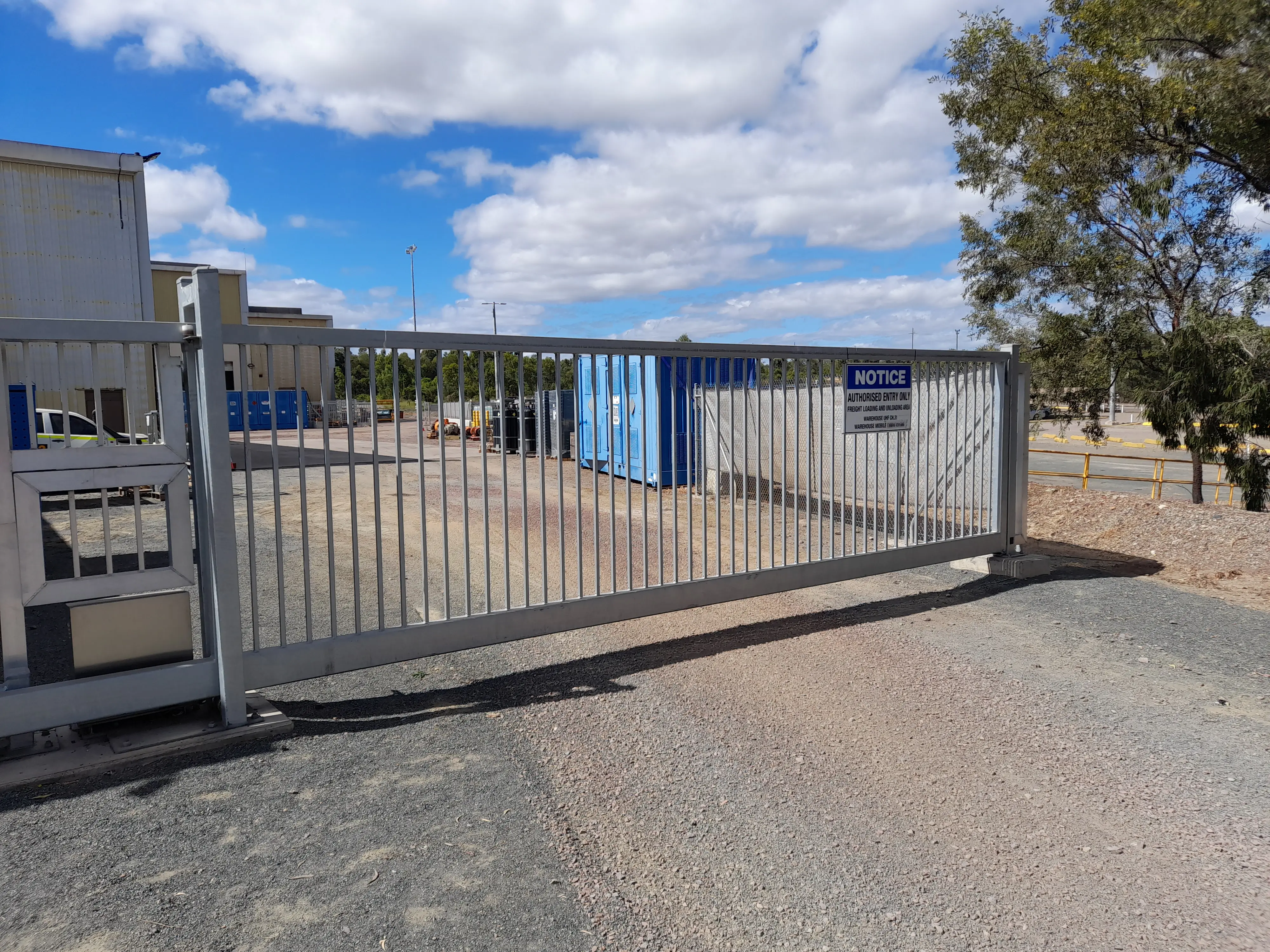
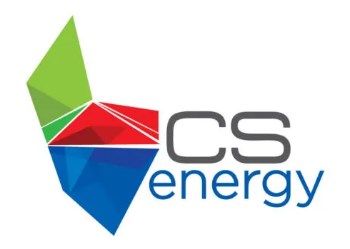
Boiler Structural Brace
CS Energy’s Kogan Creek Power Station was experiencing intermittent lateral vibration in the structural bracing of two of its boilers. The assistance of Orana Engineering was sought in conducting a structural and vibrational engineering review of the affected plant to determine the source of the issue. The review included SpaceGASS modelling of the local structure surrounding the bracing to assess loading and determine member sizing. A modal vibration analysis was completed to determine the natural frequencies of the plant and structural bracing.
Following review, the option of installing cables for the bracing was discounted and it was recommended that new bracing for structural members be installed and connected to the midpoint on either side using a custom designed clamped fitting (to avoid welding to existing loaded brace) and installing a new cleat at the main structural member. The design solution increased the lowest natural frequency vibration mode shape for the structures and also reduced visible deflection.
Orana Engineering deliverables for the project included a Boiler Structural Beam Plan Arrangement and detail drawing ‘issued for construction’.
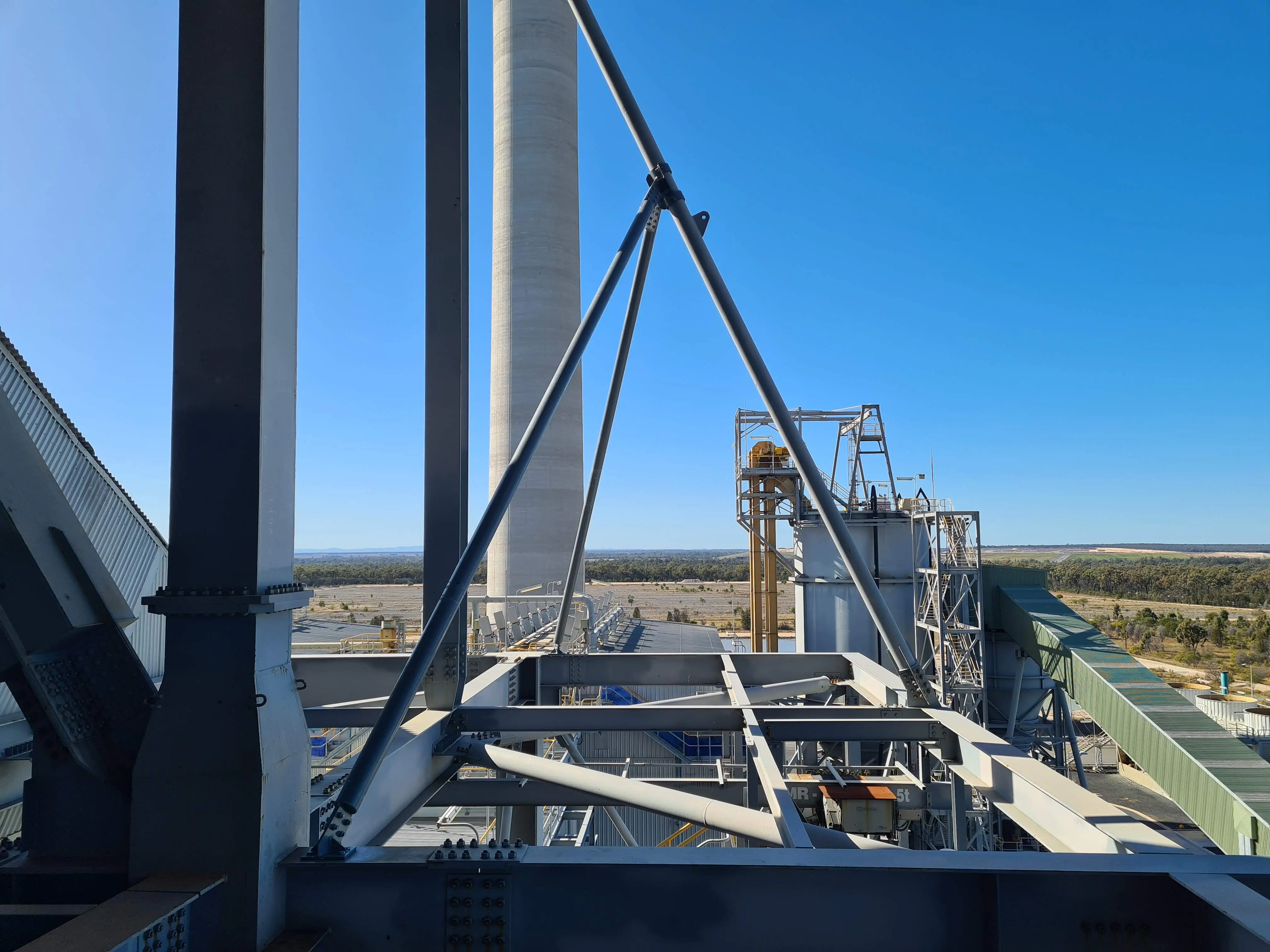
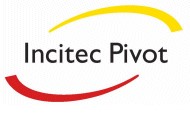
HV Tripping Supplies
Incitec Pivot’s Phosphate Hill site required replacement of tripping supplies for HV switchboards within its Ammonia Plant, Central Services, Phosphoric Acid Plant, Granulation Plant and Beneficiation Plant.
The switchboards had a dedicated 110VDC tripping supply with battery backup to power the HV protection relays and provide tripping supply power to HV circuit breakers. Without this back-up supply, circuit breakers would not open in the event of an electrical fault which could result in a catastrophic switchroom fire.
Existing tripping supplies were approaching end of life and with component failure likely to increase it was proposed to replace the tripping supplies during suitable shutdowns.
Orana Engineering was engaged to complete engineering design and to provide design drawings ‘issued for construction’. The Orana Engineering-assigned project manager had responsibility for vendor engagement, liaison with site planning and procurement personnel and site attendance during installation, commissioning and construction stages.
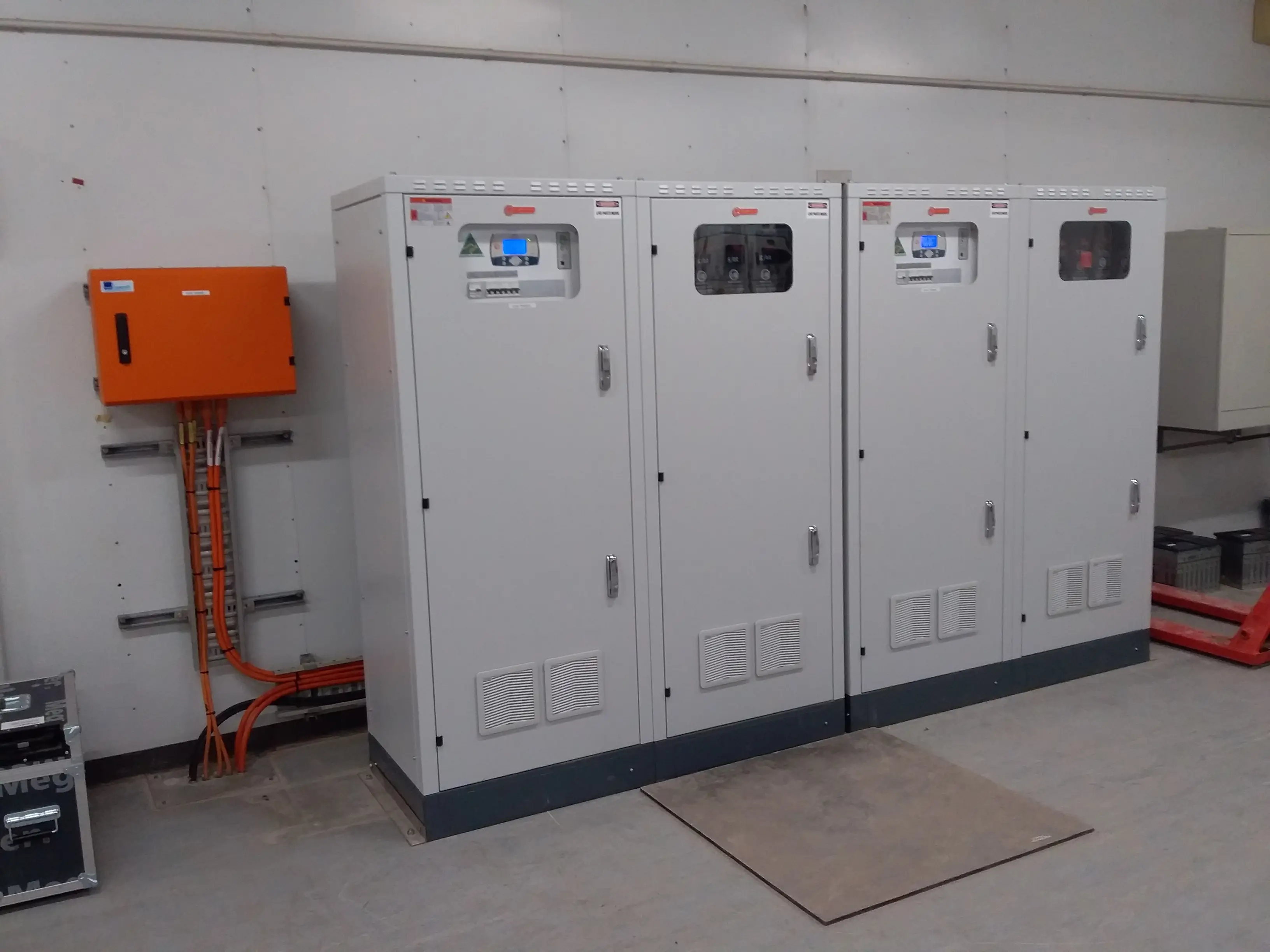
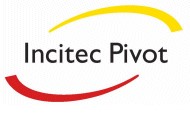
Gas Turbine No.1 Protection Relay Upgrade
Incitec Pivot was looking to replace an existing turbine generator pole slip relay unit at its Phosphate Hill Power Station. Existing pole slip relays had become obsolete and were at the end of their expected life. Pole slip relays perform a critical protection function for turbine generators and operation of a generator without its pole slip relay would pose an unacceptable risk. Consequences of relay failure on turbine generators would be multiple gas turbines being unserviceable and resulting in power shortages across the site.
The project scope involved replacement of Multilin 489 protection relay with new Multilin 889 for a 4.5MW gas turbine generator as well as integration of pole slip protection and a synchronisation check facility into the Multilin 889.
Orana Engineering’s input for the project included electrical engineering design, protection configuration, on site project management and commissioning.
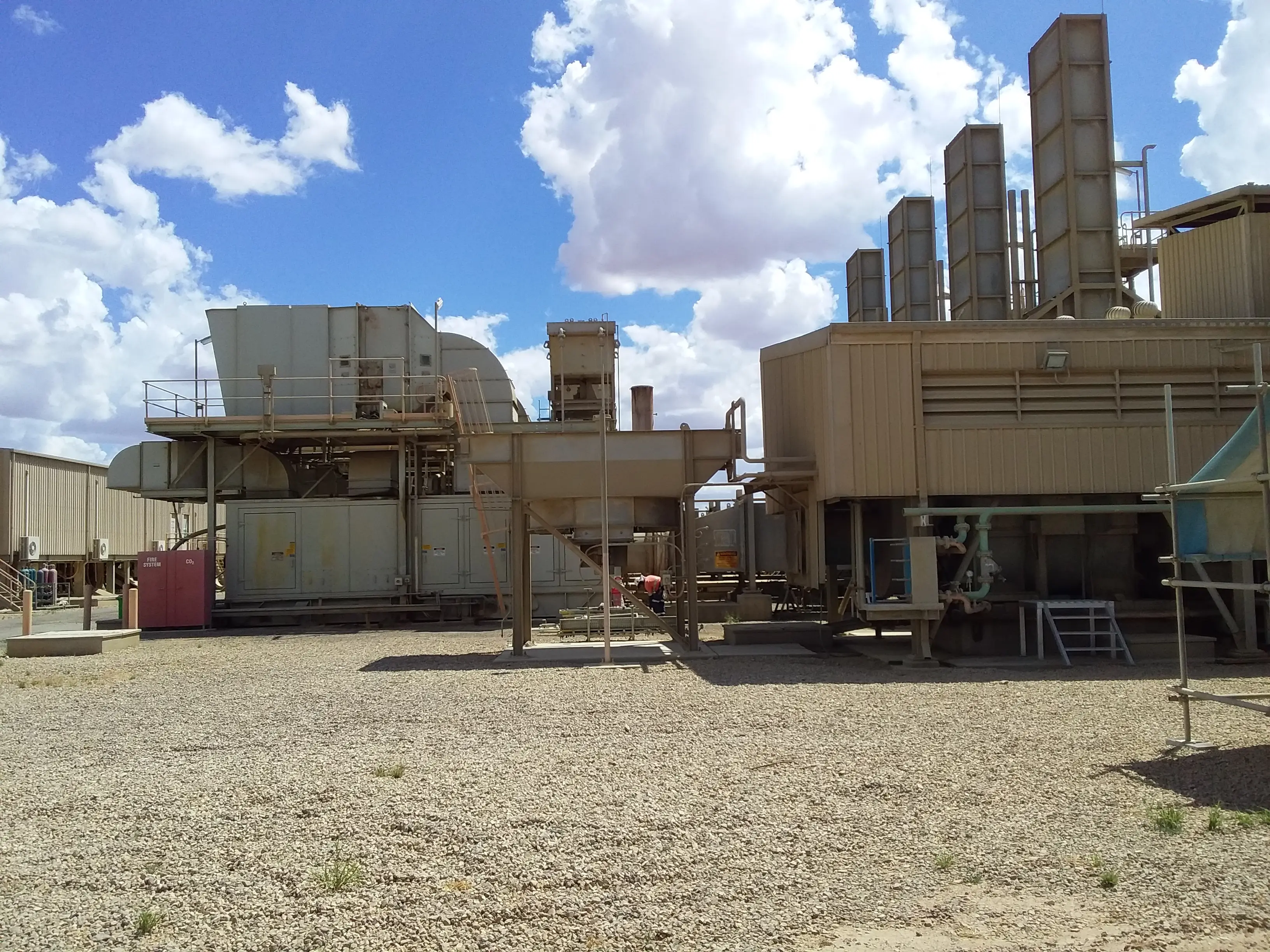
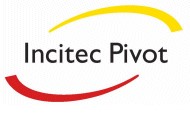
Acid Unloading Leak Detection & CCTV Upgrade
To reduce the likelihood of potential spills in the sulphuric acid unloading area at its Phosphate Hill site, and to prevent consequential environmental and health and safety impacts, Incitec Pivot sought assistance from Orana Engineering with an upgrade of existing acid unloading leak detection and CCTV systems.
In consultation with Phosphate Hill site stakeholder personnel, Orana Engineering conducted an evaluation of available mitigation scenarios before recommending electrical and control methods which were considered to be the most cost effective resolution. Orana Engineering drafting personnel also produced detailed design drawings for the acid unloading leak detection and CCTV upgrade works.
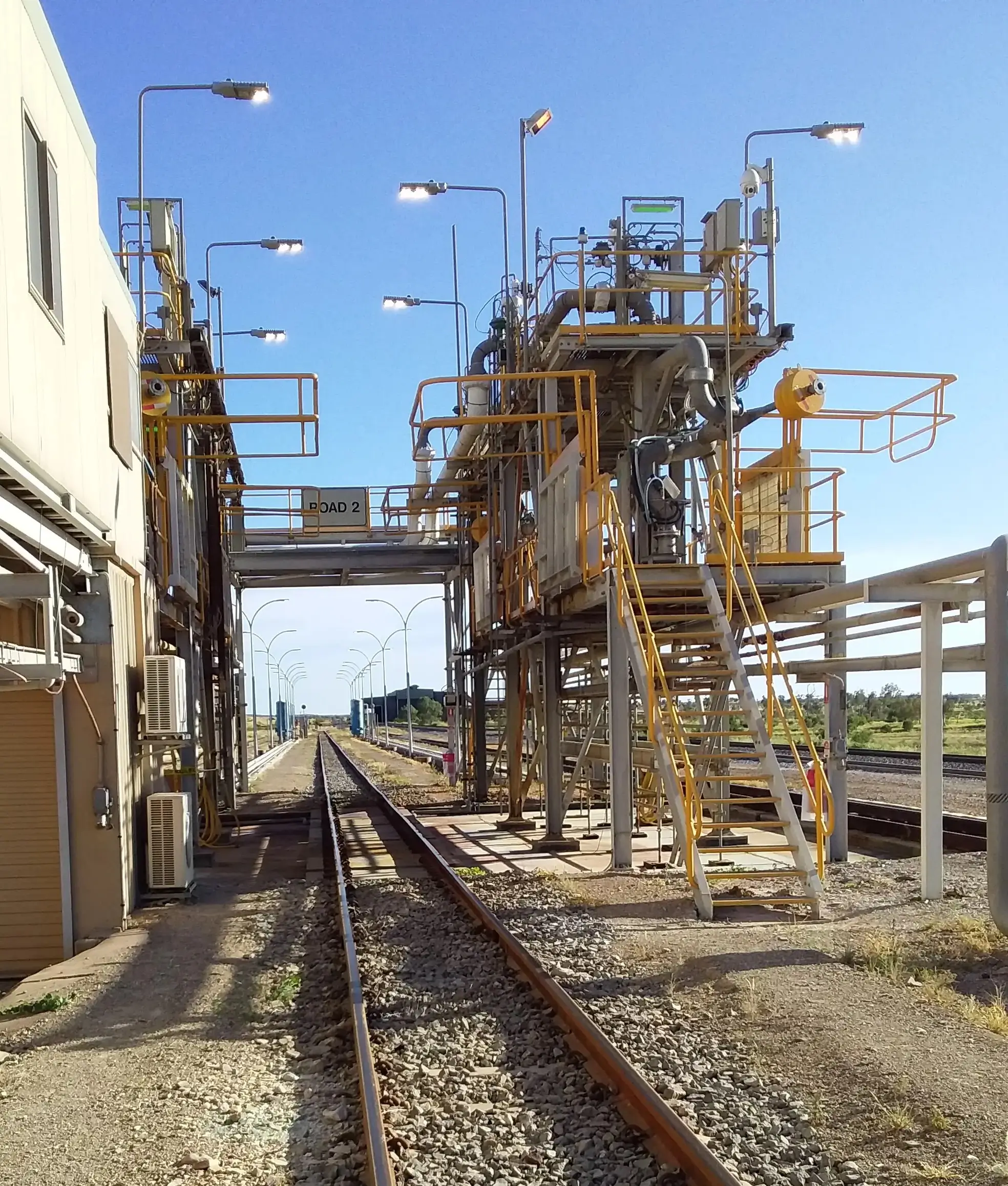
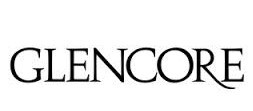
Terminal Dam MCC
The Terminal Dam pump station at Glencore’s Oaky Creek coal mine is critical in supplying the mine and township of Tieri with raw water. The existing pump station had been in service for over 30 years during which time the electrical reticulation equipment had regular maintenance but no significant upgrades. Obsolete components, changes in Standards and degradation of the equipment all signaled that the HV supply, LV MCC and LCU’s was apporaching its end of service.
At the request of Oaky Creek Coal, Orana Engineering undertook offsite electrical and control system engineering and design drafting for a Terminal Dam HV upgrade and MCC replacement. An update of the Electrical Installation SOW for the modification at Terminal Dam was prepared prior to attending site to complete the configuration and assist with project management of installation and commissioning works.
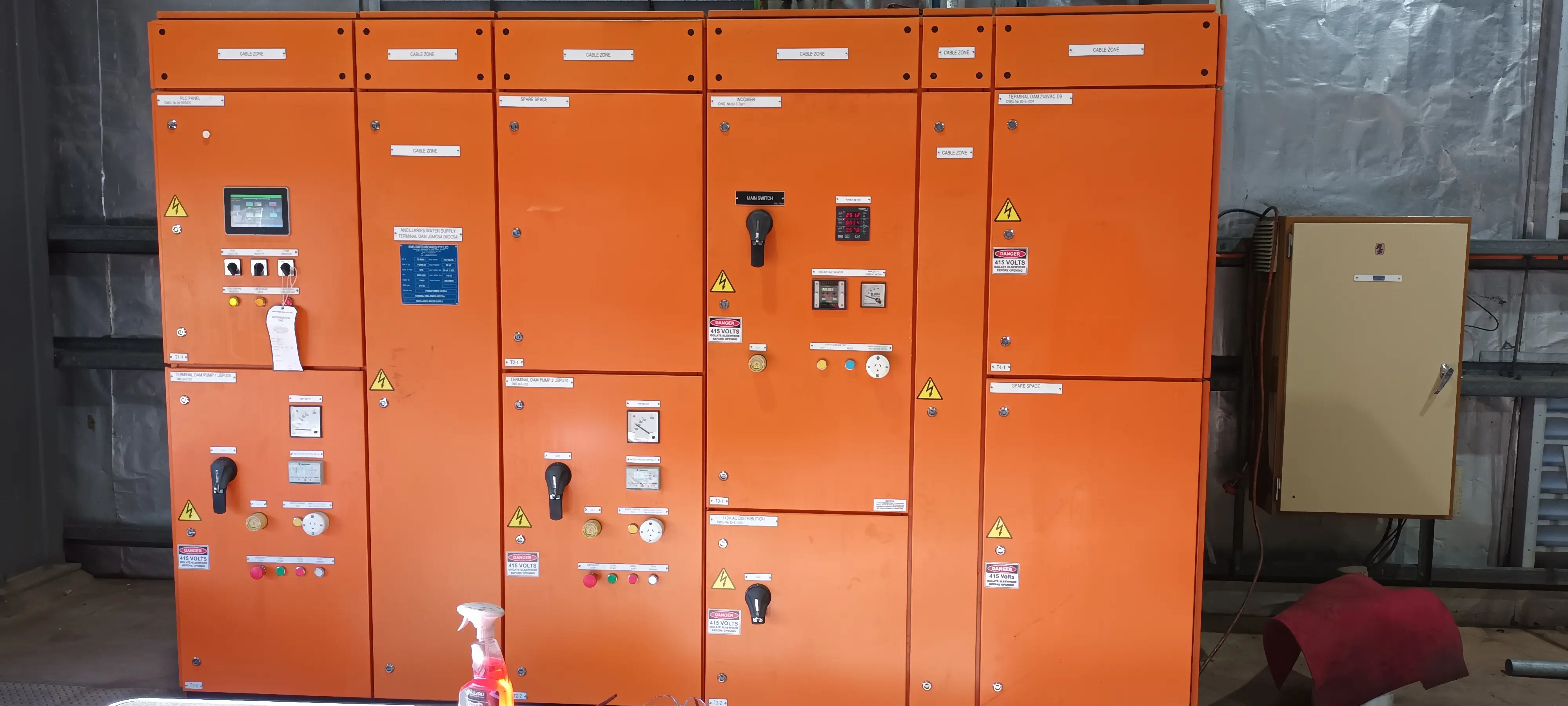
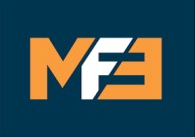
Brine Concentrator Drain Pump System
Orana Engineering was invited by MFE to provide an estimate for subcontract works for the Veolia Water brine concentrator drain pump system at Kenya Water Treatment Plant.
Brine concentrators at the plant periodically release high temperature and corrosive wastewater to floor sumps to control or monitor processes. The PVC pipework from floor sumps had become unserviceable due to the pipeline material not being rated for high temperatures. The existing drainage pipeline needed to be replaced with a durable system capable of withstanding high temperature corrosive wastewater.
Orana Engineering’s involvement in the project encompassed provision of engineering support (hydraulic, mechanical, civil and electrical design) and drafting support including revision of existing drawings and generation of new hydraulic, mechanical, civil and structural drawings with RPEQ supervision.
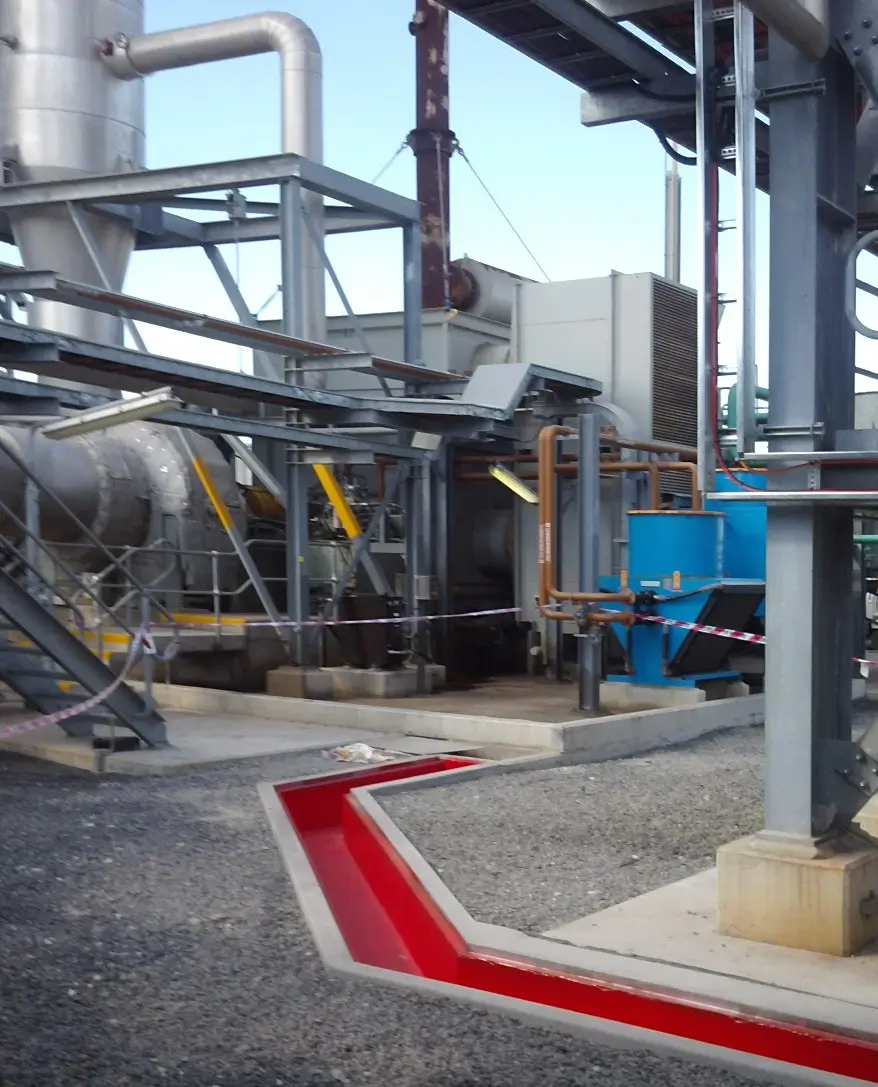
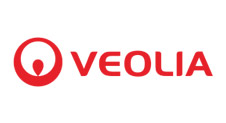
Brine Concentrator Engine Bay Crane
Veolia’s Kenya Water Treatment Plant contacted Orana Engineering for assistance with engineering design and drafting of a manual pull-along crane utilising existing support beams and able to travel in both long and cross travel directions. It was proposed for the fabricated cranes to be installed in each of the treatment plant’s three brine concentrator engine bays.
A member of Orana Engineering’s mechanical engineering team attended site to inspect existing infrastructure, take measurements and gather information. Upon return to Orana Engineering’s Chinchilla office the site data was reviewed, structural engineering calculations performed and information provided to the drafting office for translation to general arrangement and detailed design drawings suitable for fabrication purposes.
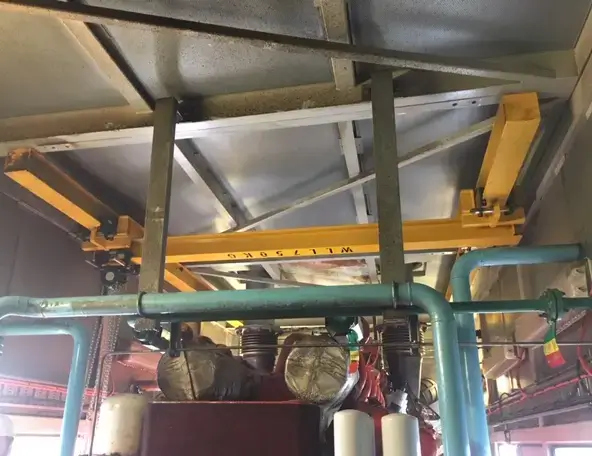
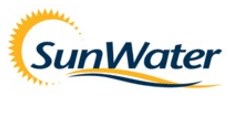
Culgoa Weir Gates
Orana Engineering was contacted by Sunwater to design a frame capable of supporting two hydraulic over-shot gates to be installed on the existing Culgoa Weir structure. The purpose of the gates was to allow water flow downstream when open. Hydraulics were to be driven via a power pack on the back of a utility vehicle.
Orana Engineering undertook mechanical design of the gate frame including reviews of weir flow calculations and load scenarios. Structural design aspects involved calculations, selection of member sizes, bolting details and connections as well as modelling of the frame in SpaceGASS with applied load cases and AS4100 analysis.
Orana Engineering designers produced a 3D model of the frame and gate arrangements and drawings suitable for handover to a fabricator for installation.
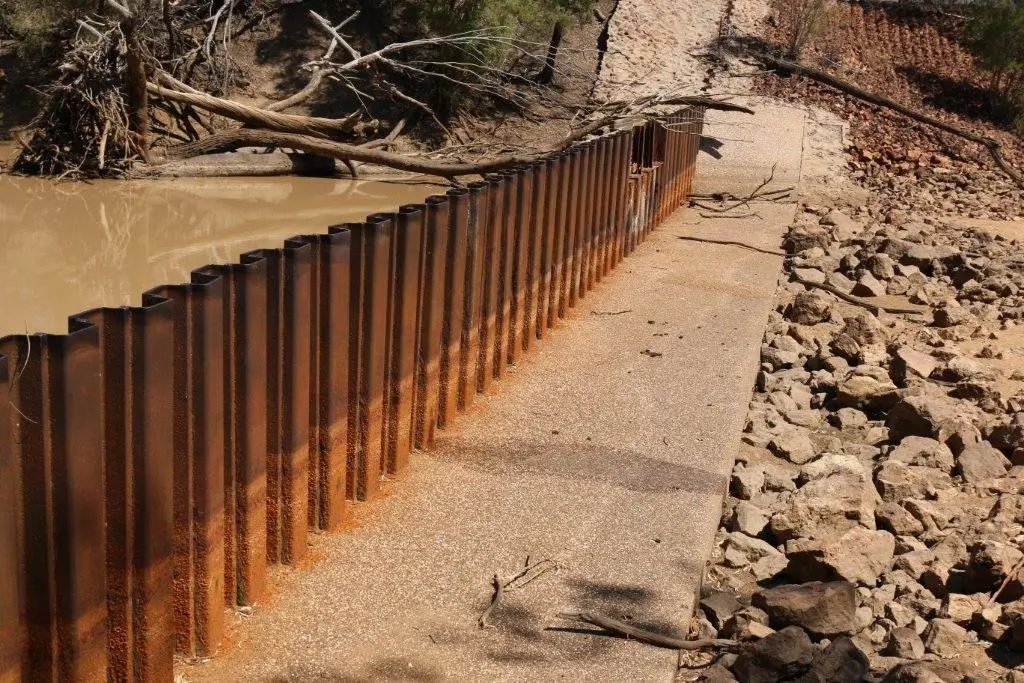
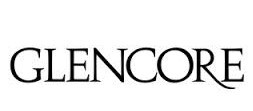
Main Sub Upgrades
The main substation at Glencore’s Oaky Creek Coal is essential for surface operations. Site personnel had highlighted multiple projects for implementation to collectively improve the integrity and reliability of the main sub. For each of the projects there were common elements and beneficial outcomes for executing them concurrently.
Given the critical nature of the projects and the importance of success, Orana Engineering developed a project management and design scope for provision of a dedicated Electrical / Control Systems Engineer from its Engineering Team.
Projects under the scope consisted of safety and reliability upgrades for OCC Main 66 / 11kV substation including automated racking of circuit breakers, interlocking of transformer tap changers and parallelling control, cable pit sump pump control.
Work undertaken included detailed design, PLC and DCS configuration, protection relay configuration, racking controllers, and commissioning whilst also mananging the client's drawing management system.
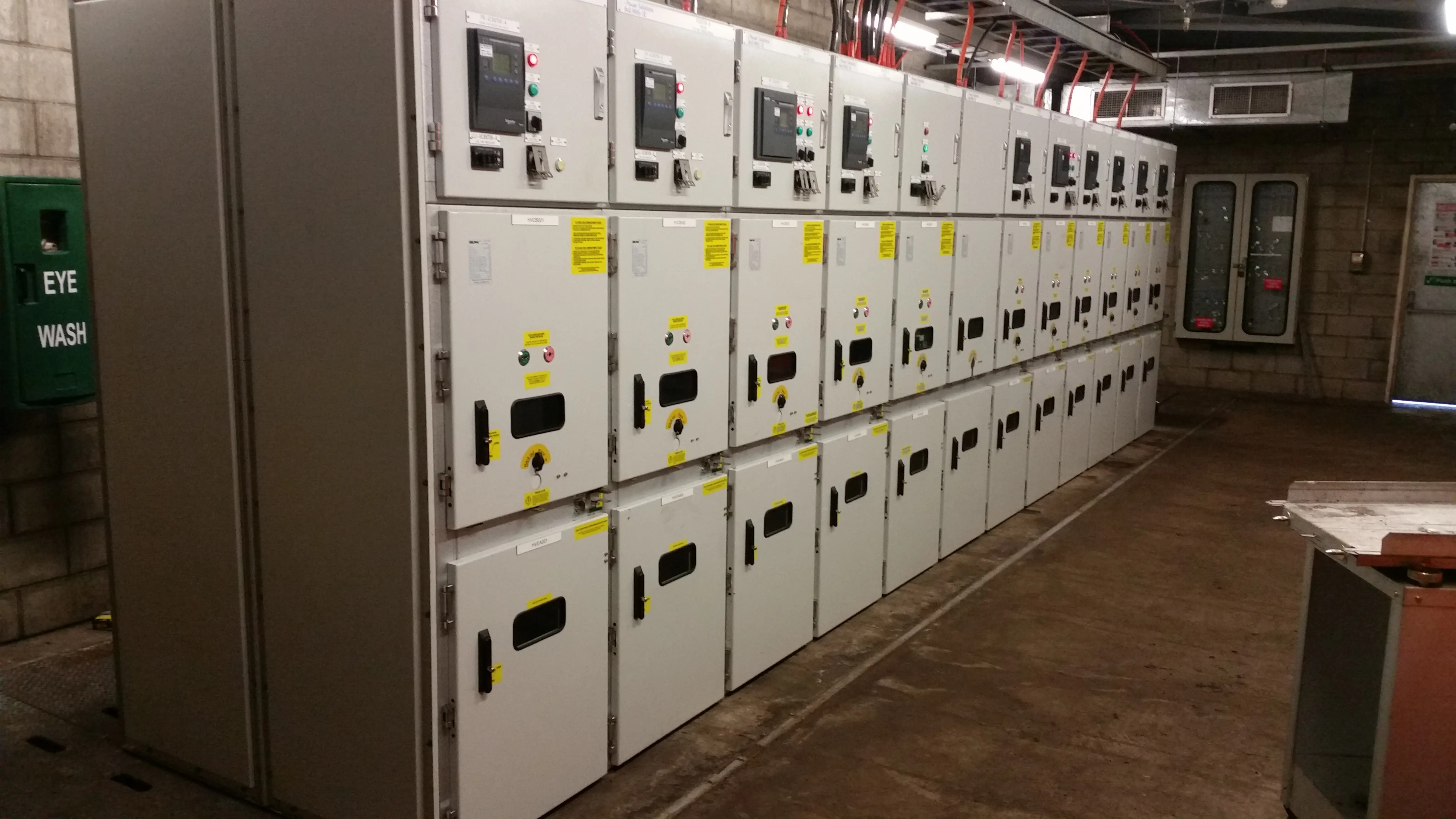
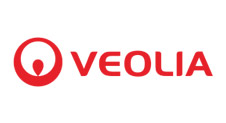
Brine Concentrator Stair Tower Rescue Lift Points
Veolia Water’s Kenya Water Treatment Plant contacted Orana Engineering to provide engineering and design drafting assistance in relation to installation of fall-arrest rescue anchor points to the brine concentrator stair tower.
Orana Engineering mechanical personnel undertook a review of applicable codes and standards in order to identify key safety considerations in the use of fall arrest systems. Calculations were performed on existing structural members locally to determine beam capacity for the addition of lugs at 6 points as identified by the client.
Deliverables for the project included an RPEQ supervised design for manufacture and installation of the lugs, revision of existing client drawings to reflect design changes and creation of a new drawing including both general and detailed information for new lug locations.
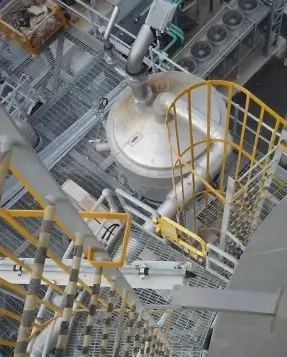
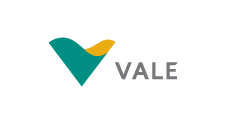
Telehandler Bin Design
At the request of Carborough Downs Coal, Orana Engineering initiated the design of a new bin for collection of used coal samples within the CHPP. Up until that point practice had been to transport samples to the bin by wheelbarrow, with the barrow then lifted (rather than levered) and the contents tipped into the bin.
Carborough Downs requested that Orana Engineering design a bin to enable wheeling of the barrow into the bin such that the contents could be tipped without the need to lift the barrow. Once full the bin would be collected via a telehandler and emptied onto the rejects pile.
Orana Engineering designers prepared a high level 3D model of the proposed telehandler bin, a 3D design of the lifting and pivot mechanism and bin fabrication, detail and assembly drawings with RPEQ Supervision.
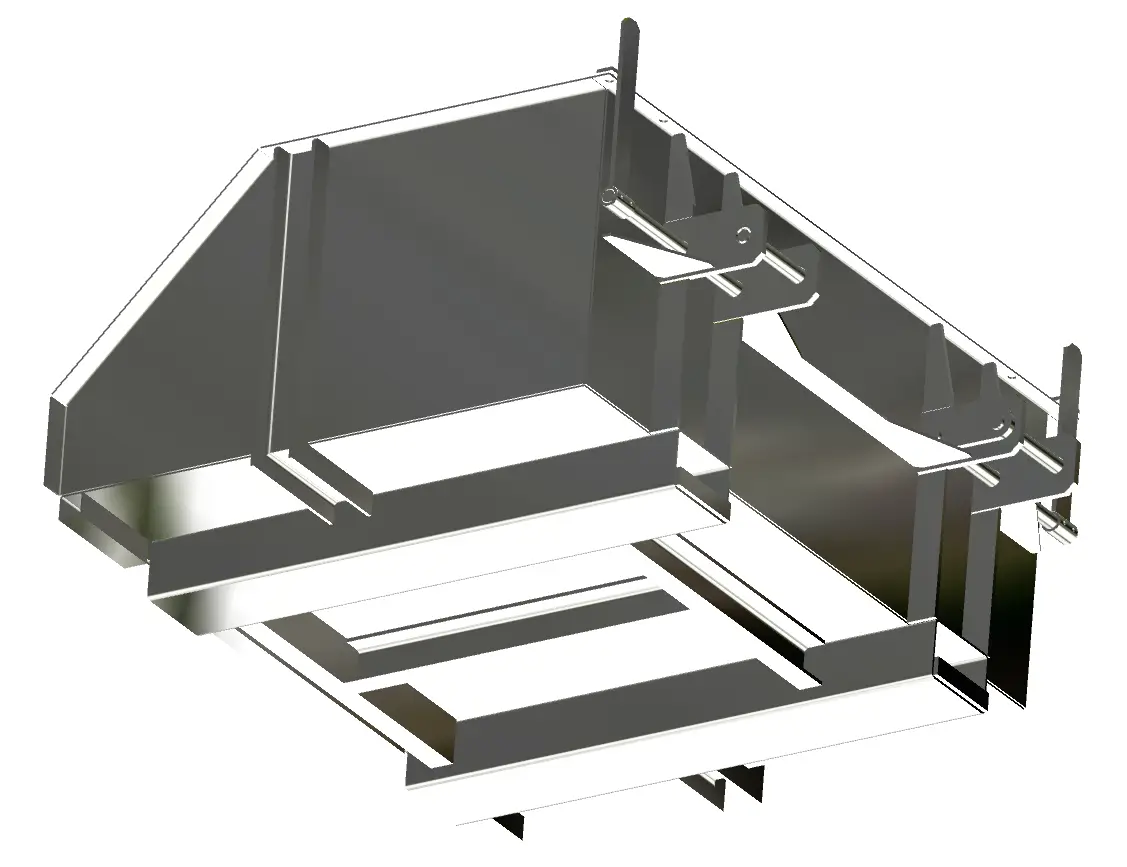
.jpg)
GCB Enclosure
Origin Energy sought assistance from Orana Engineering in providing a concept design for shade shelters to be retro-fitted to existing GCB enclosures at its Uranquinty Power Station in southern New South Wales. The objective of the shelters was to reduce rainwater contact with GCBs and the design to be such that shelters could be lifted off for periodic maintenance of GCBs.
A third party undertook 3D scanning of the existing cover structures and provided resultant scan data for 3D modelling by our design team. SpaceGASS modelling of the structures and analysis of compliance to Australian Standards was also conducted prior to provision of the new enclosure concept to Origin Energy for review. Upon receipt of design approval, Orana Engineering developed and issued a scope of work for supply and installation of the GCB enclosure shelters.
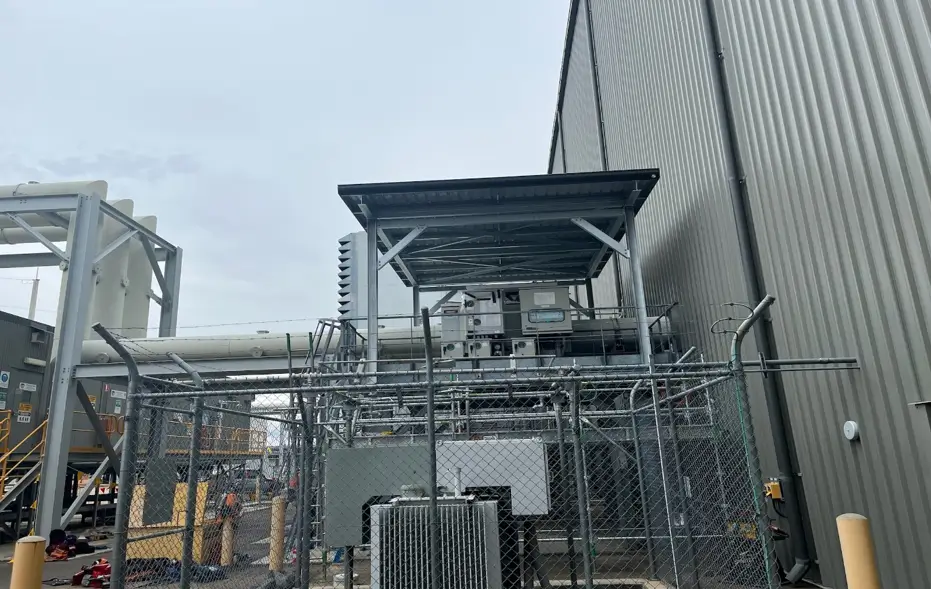
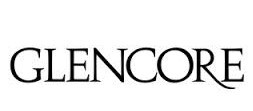
Secondary Spirals Monorail Design
At the request of Glencore Collinsville Coal Mine, Orana Engineering performed engineering design and drafting for a new monorail to be installed within the CHPP secondary spirals area. Orana Engineering’s assistance with the project included SpaceGASS modelling of the area and completing initial engineering and analysis for the proposed monorail while considering any effects on the existing structure and performing calculations and structural design checks to Australian Standards AS4100, AS1170 and AS1418.18.
Lifting vendors were consulted for monorail trolley and chain block options which ensured the most appropriate selections for the Collinsville application.
The designers at Orana Engineering produced a 3D model which was issued to the client for review and feedback. The monorail was fabricated and installed by others to Orana Engineering detailed design drawings and then load tested with subsequent deflection results meeting the requirements of Australian Standards.
.webp)
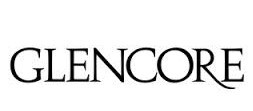
Filter Line Upgrade
Process Engineering personnel at Glencore’s Collinsville Coal mine contacted Orana Engineering for engineering support on various projects associated with an upgrade of the piping in its ultrafine circuit. These included incorporation of tee-offs to in situ lines, and additional pipe runs.
Orana Engineering utilised existing 3D scan data to model a new pipe route and to provide concept general arrangement drawings to the client. With this information site personnel had sufficient data to liaise with vendors regarding new equipment selection.
Orana Engineering’s estimate also allowed for detailed design of RPEQ supervised drawings to allow the piping to be fabricated and installed.
Additionally, Orana Engineering conducted a structural assessment of the horizonal belt filter (HBF) to support a proposed viper roller unit.
_1.webp)
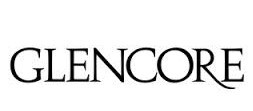
CHPP Structural Repairs - CBN302
Glencore's Collinsville Coal Mine engaged Orana Engineering to develop a deconstruction safe work methodology for demolition and deconstruction of the CBN302 reject bin, along with appropriate risk assessment documentation based on the deconstruction methodology.
Key considerations were ensuring that the bin and structure supporting the conveyor head end were maintained in a safe and stable condition during deconstruction and that the risks of stored energy in the curved bin shell plates was managed through the steel thermal cutting process (avoiding steel plate spring-back hazards).
Orana Engineering’s basis of design determined the necessary steps to safely remove the redundant CBN302 reject bin.
Detailed design and engineering provided by Orana Engineering included 3D modelling of the reject bin and structural steelwork to assist in preparing the methodology images.
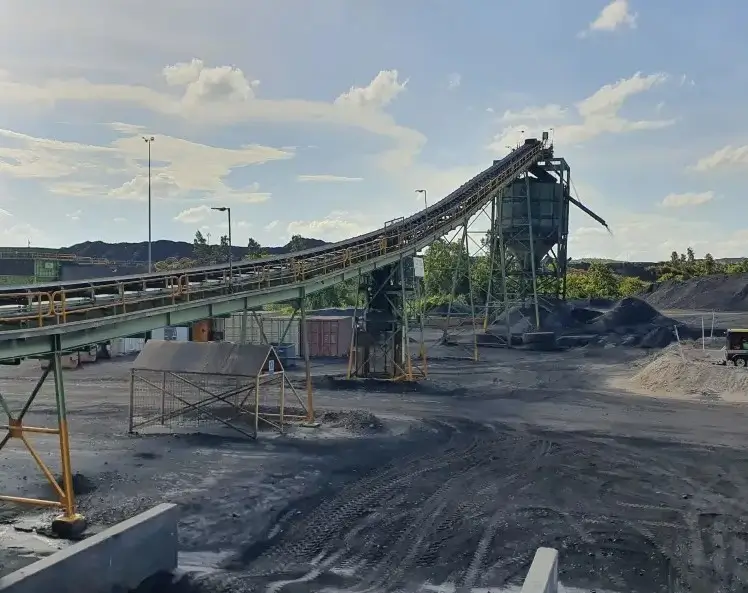
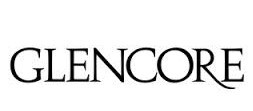
CHPP Structural Repairs - Clevis Plates
The CHPP Structural Supervisor at Glencore’s Collinsville Coal Mine requested the services of Orana Engineering in completion of a structural review and provision of a replacement methodology for the CCV101 Trestle Clevis Plates.
Orana Engineering’s consultation included a structural review of documents and existing drawings, identification of load-bearing elements and weak points, analysis of existing design and indication of necessary modifications. Additionally, the review included development of a strengthening plan and methodology utilising temporary bracing and support systems to lift the structure for trestle clevis plate replacement and avoid working under suspended loads using props.
Outcomes from the project included a letter of recommendation with instructions for the trestle clevis plates replacement works, including notes and methodology, mark-ups of site photos and drawings to illustrate the proposed replacement methodology.
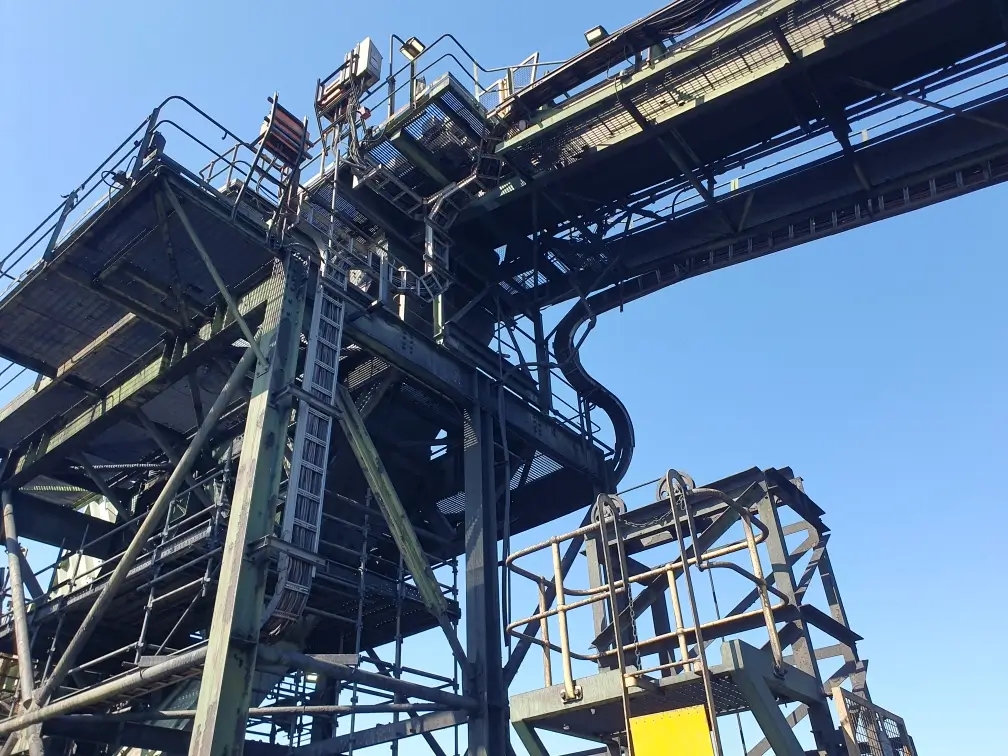
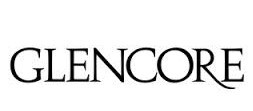
Rotary Breaker Facility Upgrade
The layout of the Rotary Breaker Reject Facility at Glencore's Collinsville Open Cut Coal Mine required loaders to be fully articulated to access and remove material from the reject bin. Orana Engineering provided a proposal for re-orientation of the facility 90 degrees, allowing loaders to drive directly into the bin area for removal of material.
The aim of proposed changes was a reduction in safety risks posed by awkward positioning of the facility. The design scope included modifying the existing reject chute to reduce blockages and other operational issues. The new design allowed for greater clearance of reject material and with the chute supported off the side wall of the facility to ensure structural integrity.
Orana Engineering designers prepared a 3D model considering limited vehicle interactions, optimising loading operations and minimising risks of structural damage. IFC drawings and project management were provided to complete the installation through to commissioning.
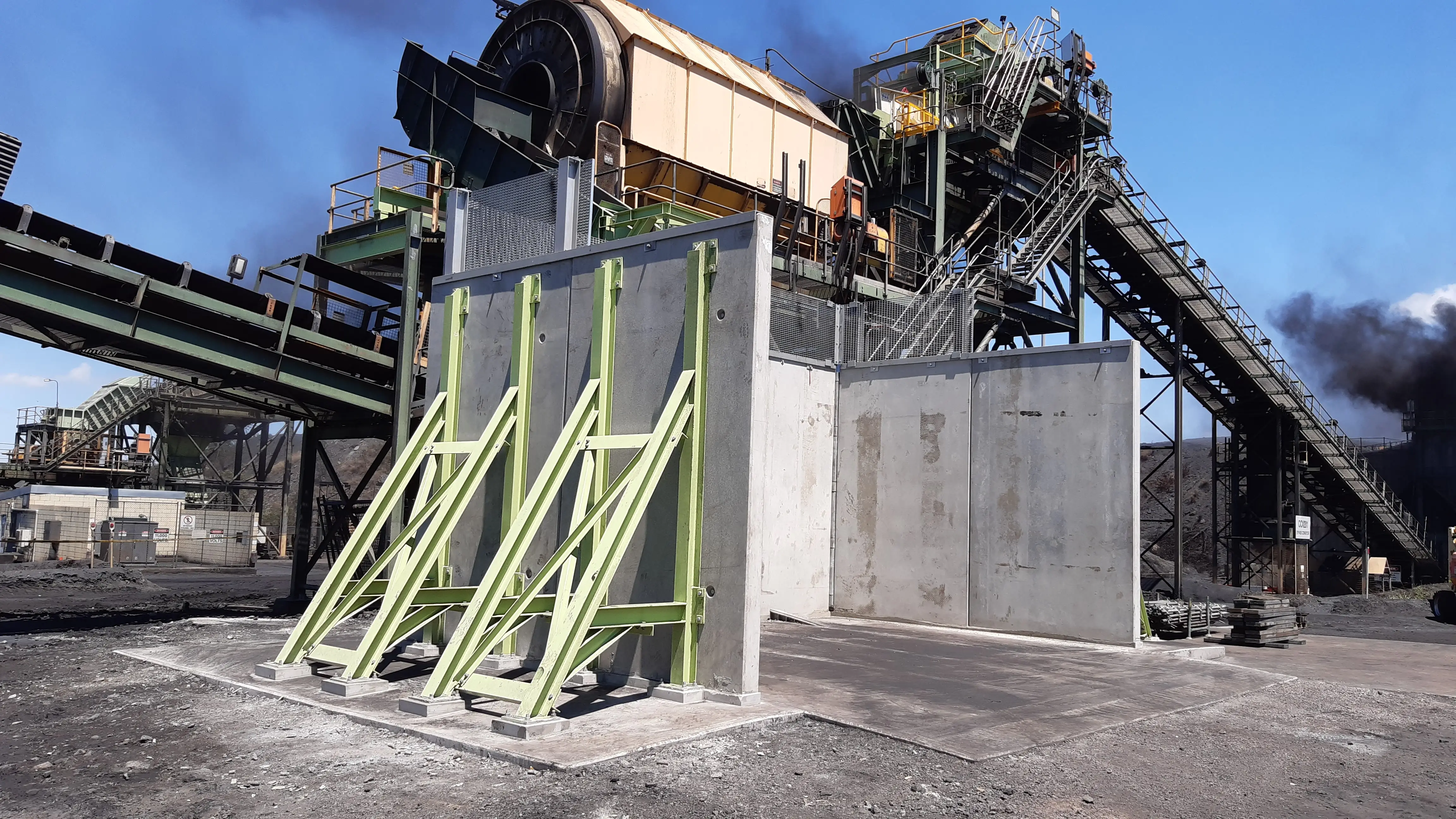
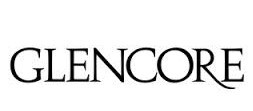
Skip Rotator
Glencore’s Ernest Henry Mine proposed to install a skip rotator to enable periodic maintenance and refurbishment of its underground ore hoist skips. The skip rotator was to consist of a removable access platform, a two-part skip cradle, plus a pneumatic drive motor and brake assembly supplied by the compressed air system. It was envisaged the rotator would enable ore skips to be rotated without the use of a 20T mobile crane and a 32T forklift which was the established method.
Orana Engineering was requested to provide mechanical and structural design and drawings of sufficient detail to allow fabrication, installation and operation of the skip rotator. In addition, Orana Engineering mechanical design personnel generated a model of the skip rotator using Autodesk Inventor which provided the client with a 3D overview of the design.
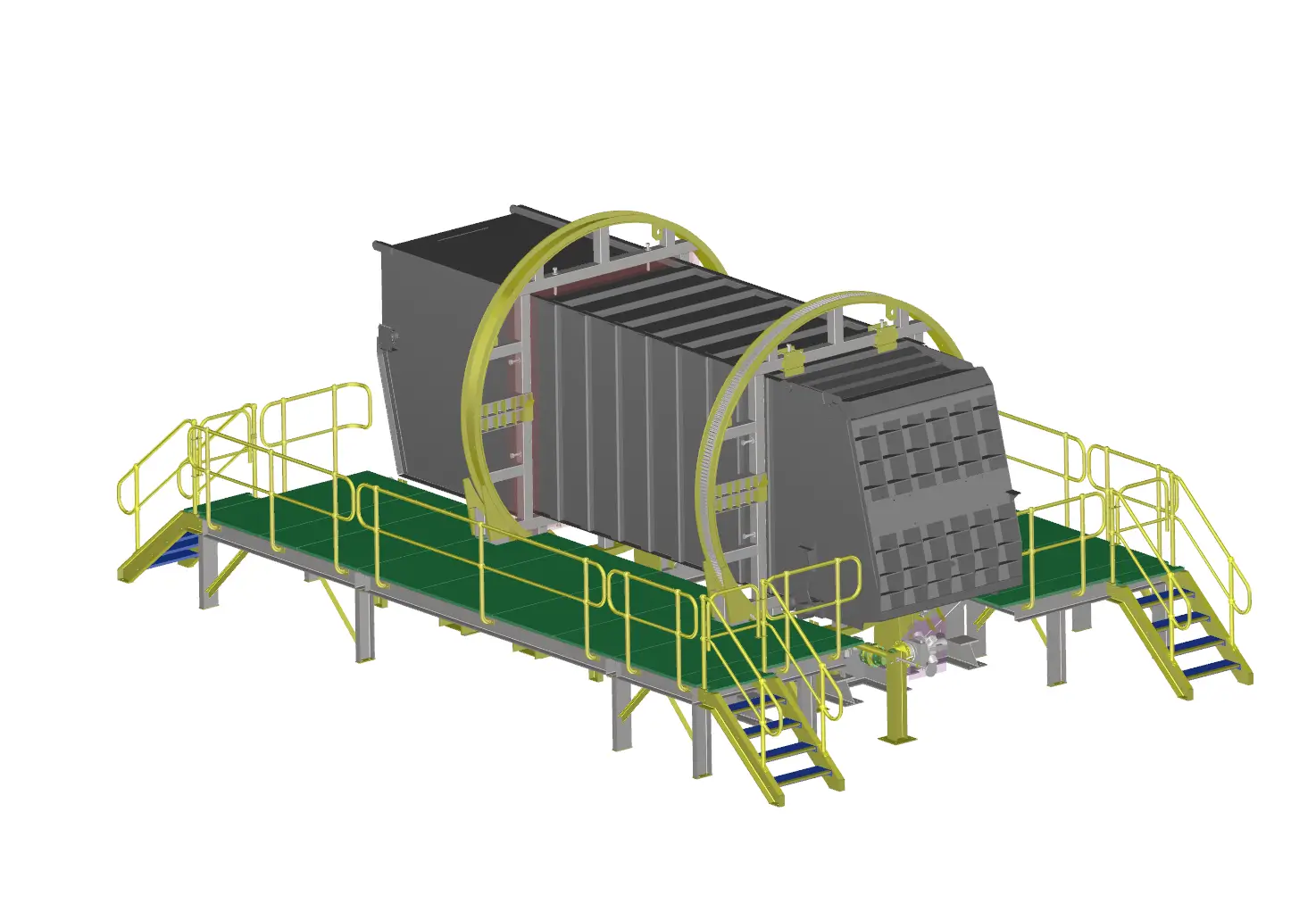
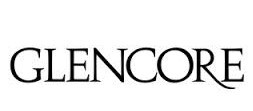
Conveyor Counterweight Design
Orana Engineering was approached by Glencore’s Oaky Creek Coal CHPP personnel to supply a cost estimate for development of modified winch systems for its CV15 and CV16 take-up towers.
The scope of work included provision of mechanical, structural and electrical engineering and design drafting for inclusion of electric take-up winches to facilitate lowering of conveyor counterweights during maintenance activities.
Structural and civil checks were conducted to account for expected force changes caused by additional sheaves and electrically driven winching effects on the structures when compared to the existing gravity take-up applications. The installation was configured and commissioned into the DCS control system by Orana Engineering's control systems engineers.
In addition to mechanical and electrical detailed design drawings, Orana Engineering provided equipment recommendations and specifications, bill of materials and a Safety In Design Report upon finalisation of the design development cost estimate.
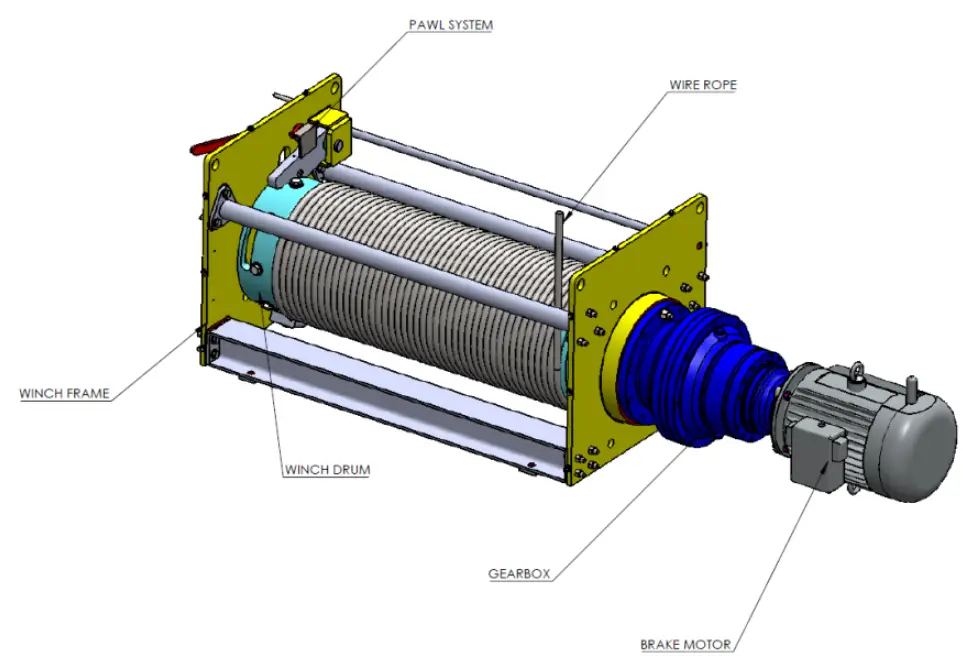
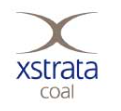
LOM Raw Water Supply Plan
Raw water pressure problems within the longwall and development mining areas at Xstrata Coal's Oaky No.1 Underground Coal Mine had resulted in numerous production delays. At the client’s request, Orana Engineering undertook a Life of Mine (LOM) study to develop a raw water supply plan based on strategic booster pump positioning.
Hydraulic modelling was subsequently completed by Orana Engineering based on the Raw Water Supply Network LOM Study and taking into account the effects of firefighting demand pressures, flow rates and water hammer.
Results were summarised in a pump positioning flow sheet and a pump positioning plan to illustrate recommended current and future booster pump positions required to achieve minimum raw water supply pressures and flow rates.
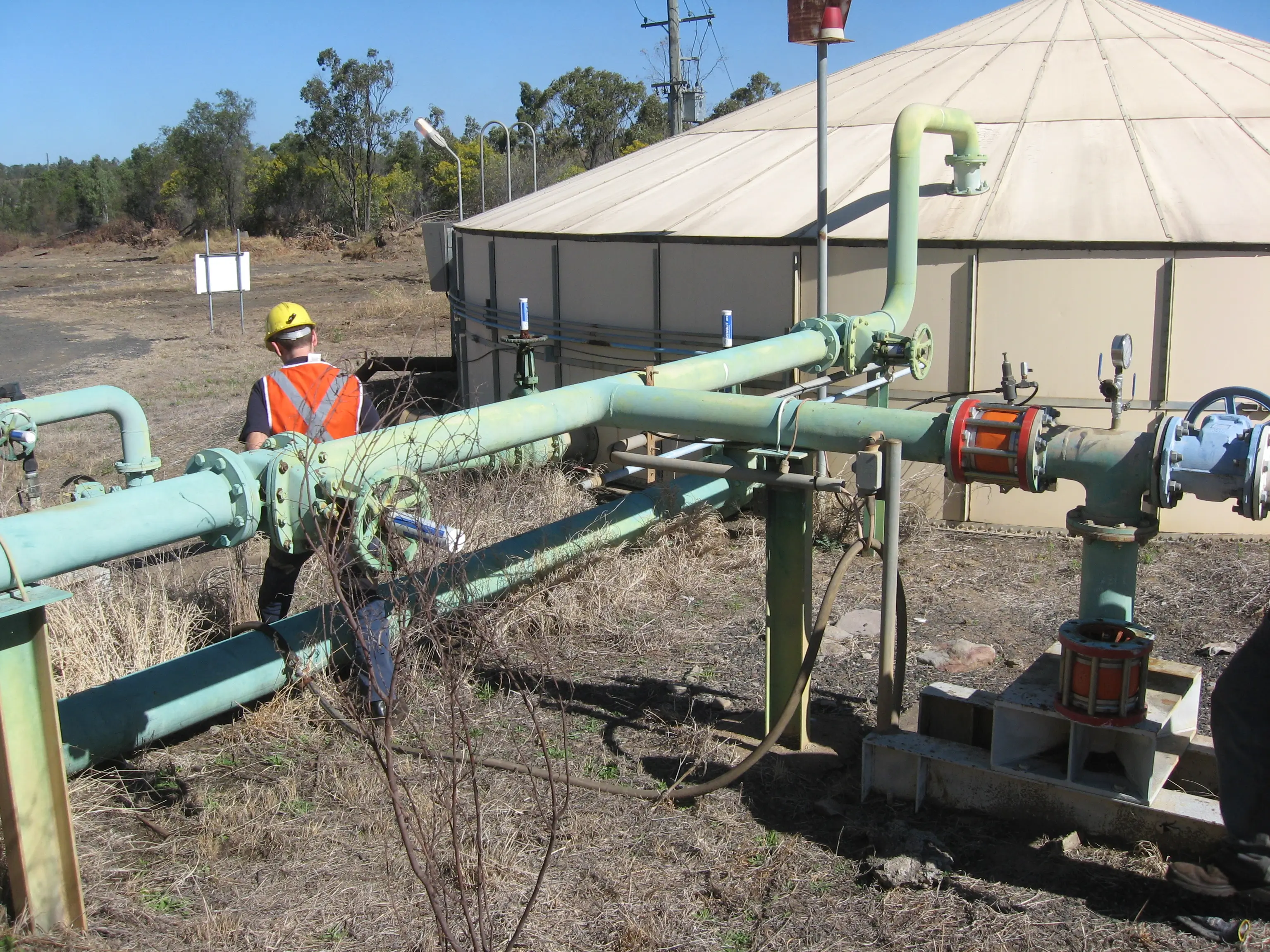
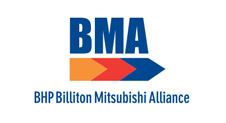
Reagents Tank Farm Rectification
Due to the existing system not being compliant to site standards, BMA Saraji Mine had constructed a new reagents system for the supply of diesel and MIBC into their CHPP. Following construction, several attempts were made to wet commission the system however these were unsuccessful due to multiple problems identified by the client.
Orana Engineering was requested to undertake a complete design review of the reagents system, to outline problems with the design and to provide a scope of work to rectify these such that wet commissioning could be completed.
At the conclusion of the review a bill of materials for the commissioning scope of work was provided, detailing procurement specifications for required mechanical equipment and spares.
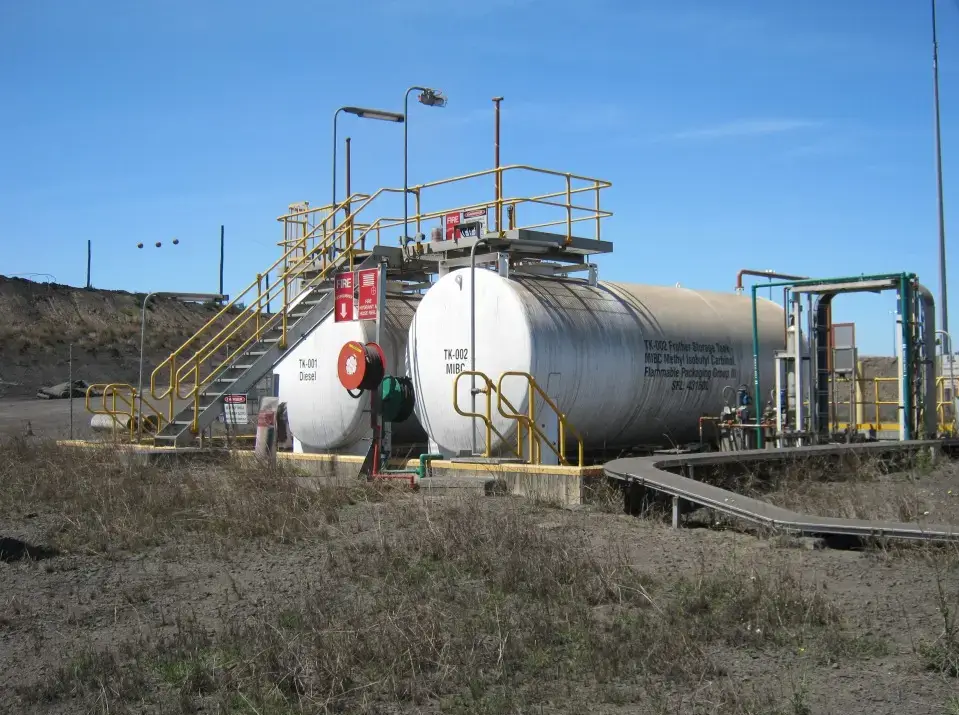
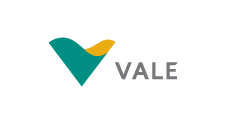
Mine Dewatering
At the request of Carborough Downs Coal, Orana Engineering initiated an investigation into an upgrade of dewatering and sump transfer systems for multiple underground and surface mining areas at the then Vale-owned mine. Existing pumping systems were deemed not fit for purpose and the client required options for solutions capable of handling projected maximum rainfall and underground water-make intensities and preventing ingress of water to mine workings during such events.
In addition, Orana Engineering was requested to formulate a concept design for dewatering of underground workings during longwall mining operations and to offer alternatives to the existing system.
At the conclusion of investigations, the client was provided with various concept designs for both surface and underground dewatering options along with equipment recommendations and budget estimates.
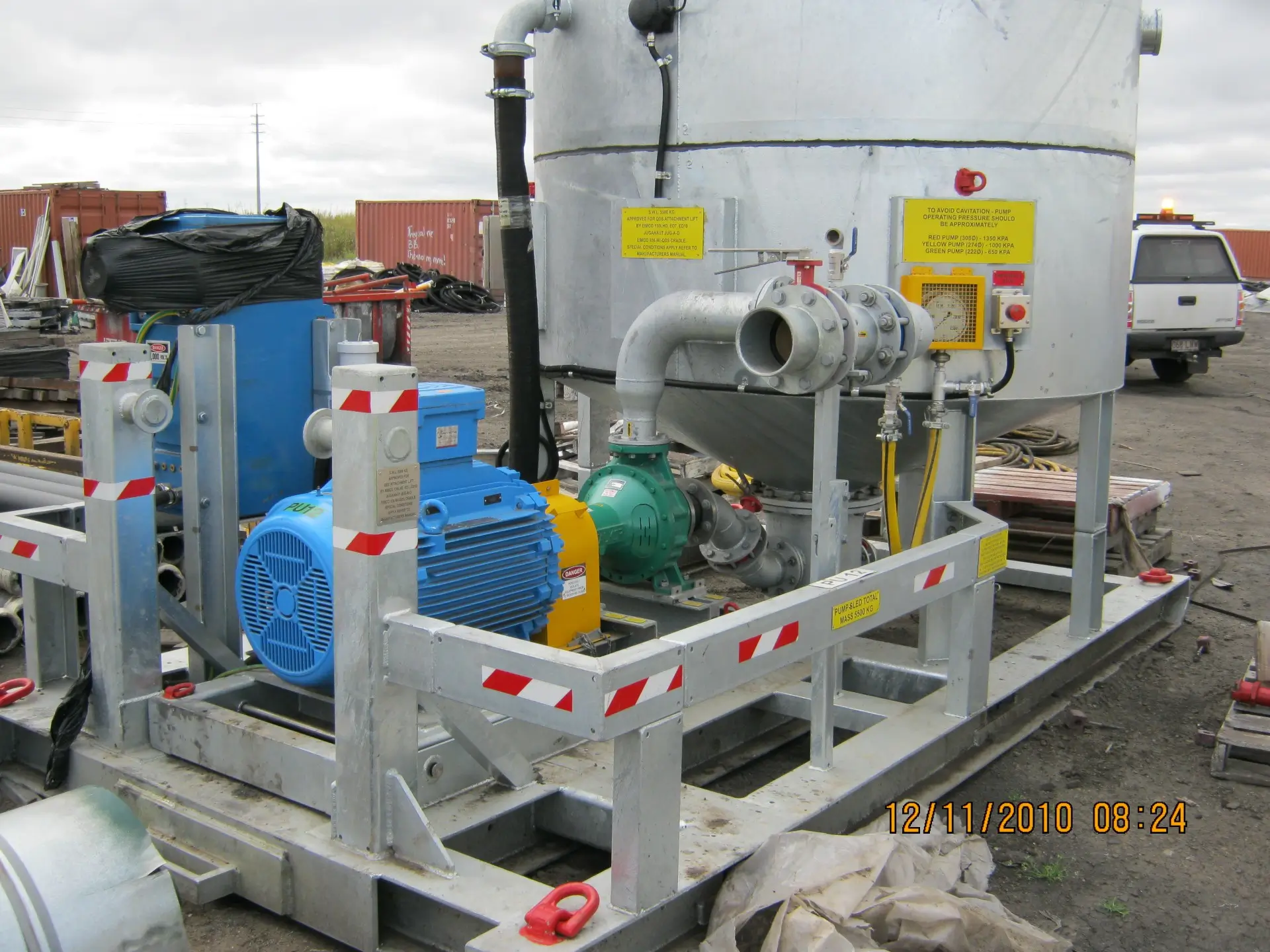
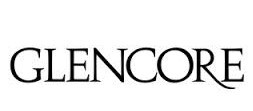
CHPP Samplers
Orana Engineering provided client engineer and project management support for the design and installation of a new product coal sampler at Glencore's Collinsville Mine CHPP. The scope also included civil engineering support and design drafting for the concrete footings which were out of scope for the sampler supplier.
Orana Engineering's project manager provided onsite support as required to deliver the multidisipline design and installation taking into account the requirements of site stakeholders in the brownfield site.
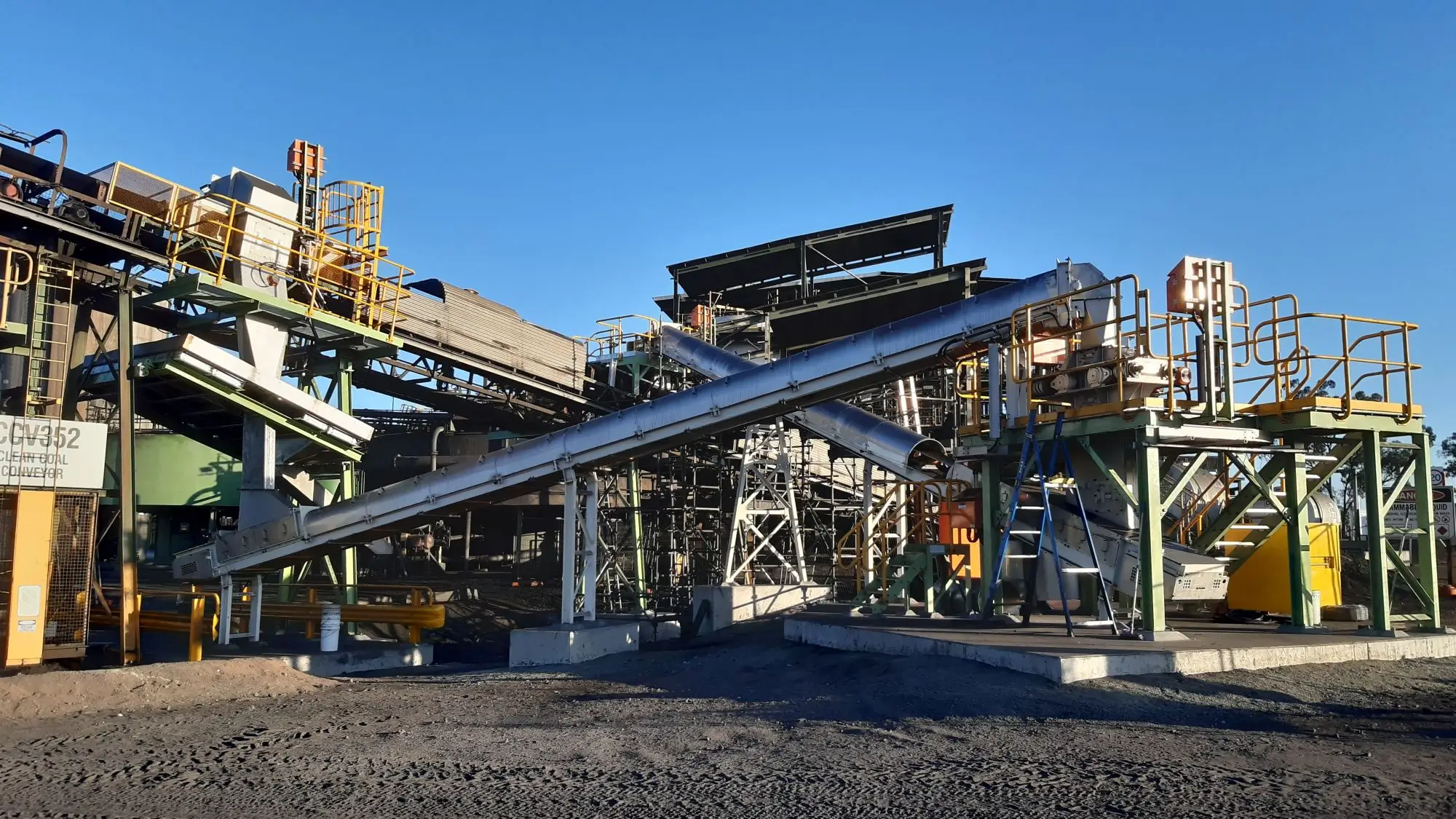
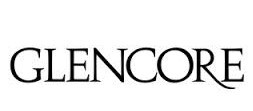
Tertiary Crusher Upgrade
Orana Engineering was called upon by Glencore's Collinsville Open Cut Coal Mine to provide engineering, drafting and project management for an upgrade to its tertiary crusher and supporting structure, involving multiple site visits to assist with on-site aspects of the construction phase.
The basis of design included engineering and drafting to understand and develop the FEED and scope for the capital project, designing of the support structure to install the replacement tertiary crusher and provision of package management for the entirety of the project.
Some of the primary deliverables for the project included 36x IFA / IFC drawings for the tertiary crusher structure upgrades, a critical spares list (including liaison with vendor), fabrication scope of work for tendering, a Change Management document, and a Risk Assessment.
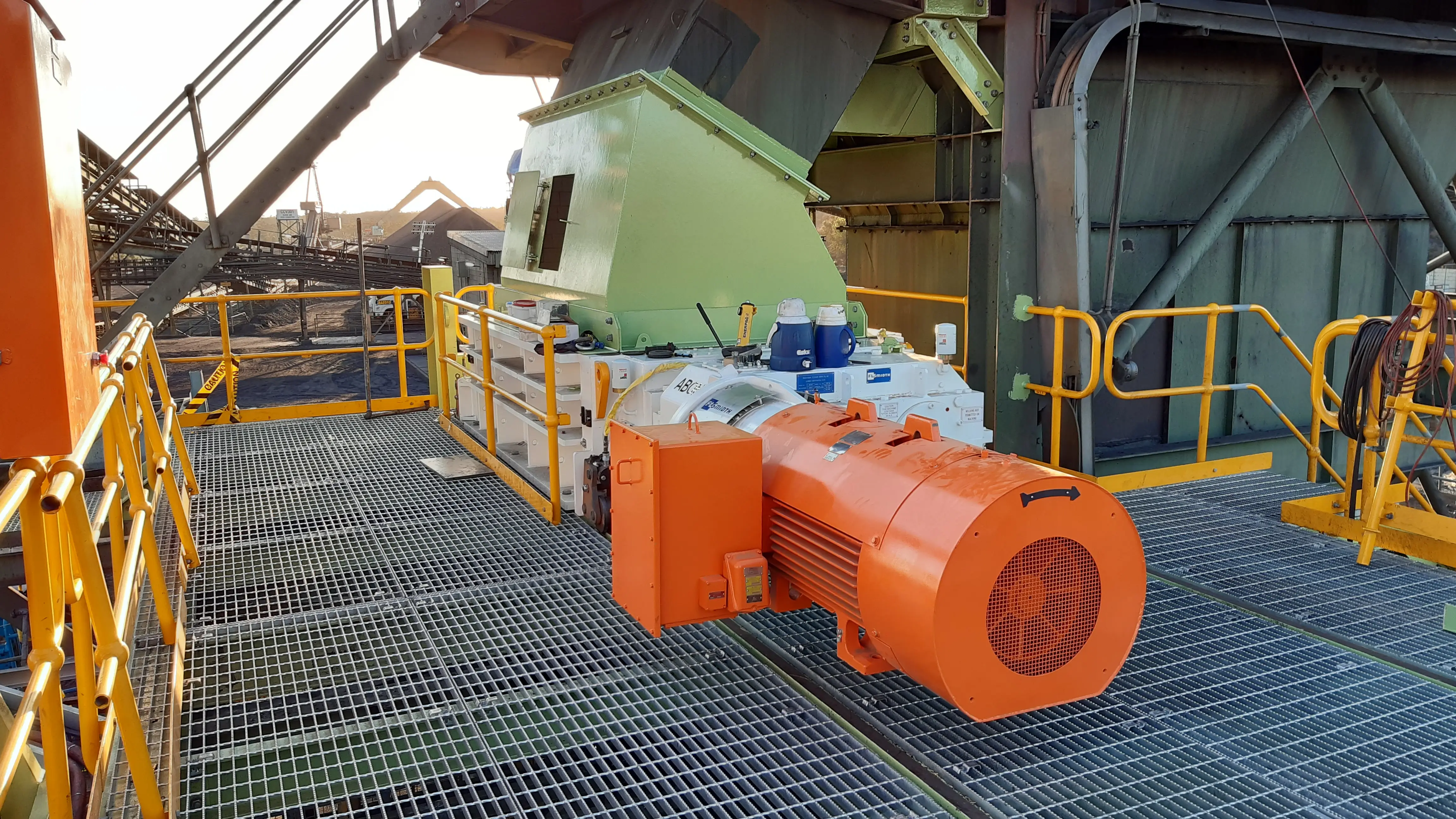
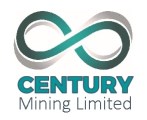
PPP027 Plant Feed Upgrade
Century Mining’s zinc tailings treatment operation is situated in north-west Queensland and is the largest tailings retreatment operation in Australia. Century sought the services of Orana Engineering in providing engineering support for its PPP027 Plant Feed Upgrade Project.
The project scope encompassed multidisipline engineering design for the upgraded plant feed pumping system including Weir Warman pumps. The client also requested a mechanical engineering review into combined use of poly lined, rubber lined and UHMWPE piping supported by Orana Engineering’s liaison with product vendors. Electrical design and site based support was delivered by Orana Engineering to suit the requirement of the project resources and timeline. Civil and structural engineering design was completed for the underground services and concreted area and footings.
.webp)
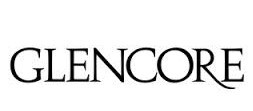
Yard Machine Upgrades - 3D Scanning
Glencore's Collinsville Open Cut Coal Mine requested the assistance of Orana Engineering in conducting 3D laser scanning of its stockyard mobile equipment comprising raw, clean and bypass coal stackers as well as a raw coal reclaimer.
Scanning was carried out during a four day shutdown, utilising Orana Engineering's Faro 3D Laser Scanner. Upon return from site, post-processing of files was completed and scan data prepared for issue to the client.
At the conclusion of the assignment, scan data was provided in a format suitable for interrogation by others in 'issued for use' format.
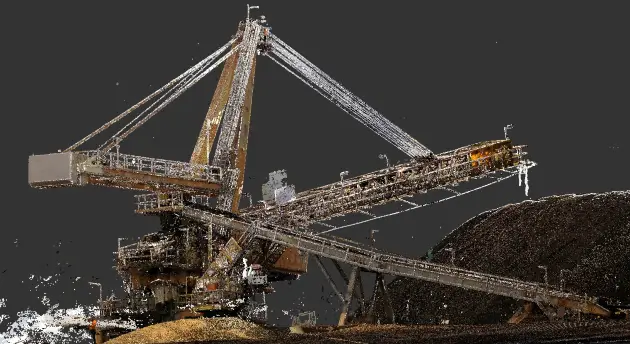
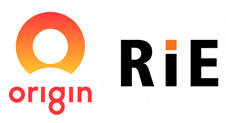
Combabula Bore Pump
Prime Pump Company was contracted by Origin Energy and Laing O’Rourke to supply an upgraded bore pumping system at Origin’s Combabula site. RIE Services was contracted by Prime Pump Company to supply and install electrical components for the upgrade, with Orana Engineering subsequently engaged by RIE Services to complete a fault protection study on the new installation.
Using SKM Power Tools for Windows software and manual calculation techniques for verification, together with information from RIE and Prime Pump Company, Orana Engineering produced an HV/LV model calculating fault levels and completing a protection co-ordination study.
From the study it was recommended a new circuit breaker be introduced to protect the transformer, variable speed drive and supply cables.
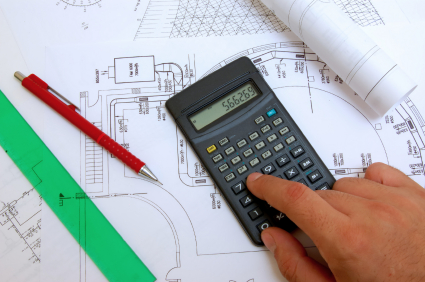
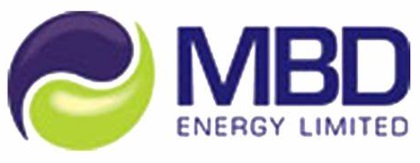
10M TAGS Sled
At James Cook University, MBD Energy operates a research facility investigating methods of cultivating and harvesting algae. To facilitate greater control of the algae agitation sleds, Orana Engineering was engaged to design and commission mechanical, electrical and control systems that would enable agitation sled velocity and frequency of travel to be automated.
The system was designed and implemented by Orana Engineering utilising Allen Bradley Powerflex VVVF drives and a Controllogix’s PLC with an RSView SCADA interface.
Orana Engineering was able to help MBD Energy improve the efficiency and quality of their research results by providing technical knowledge and assistance through our control systems, electrical engineering and mechanical engineering services.
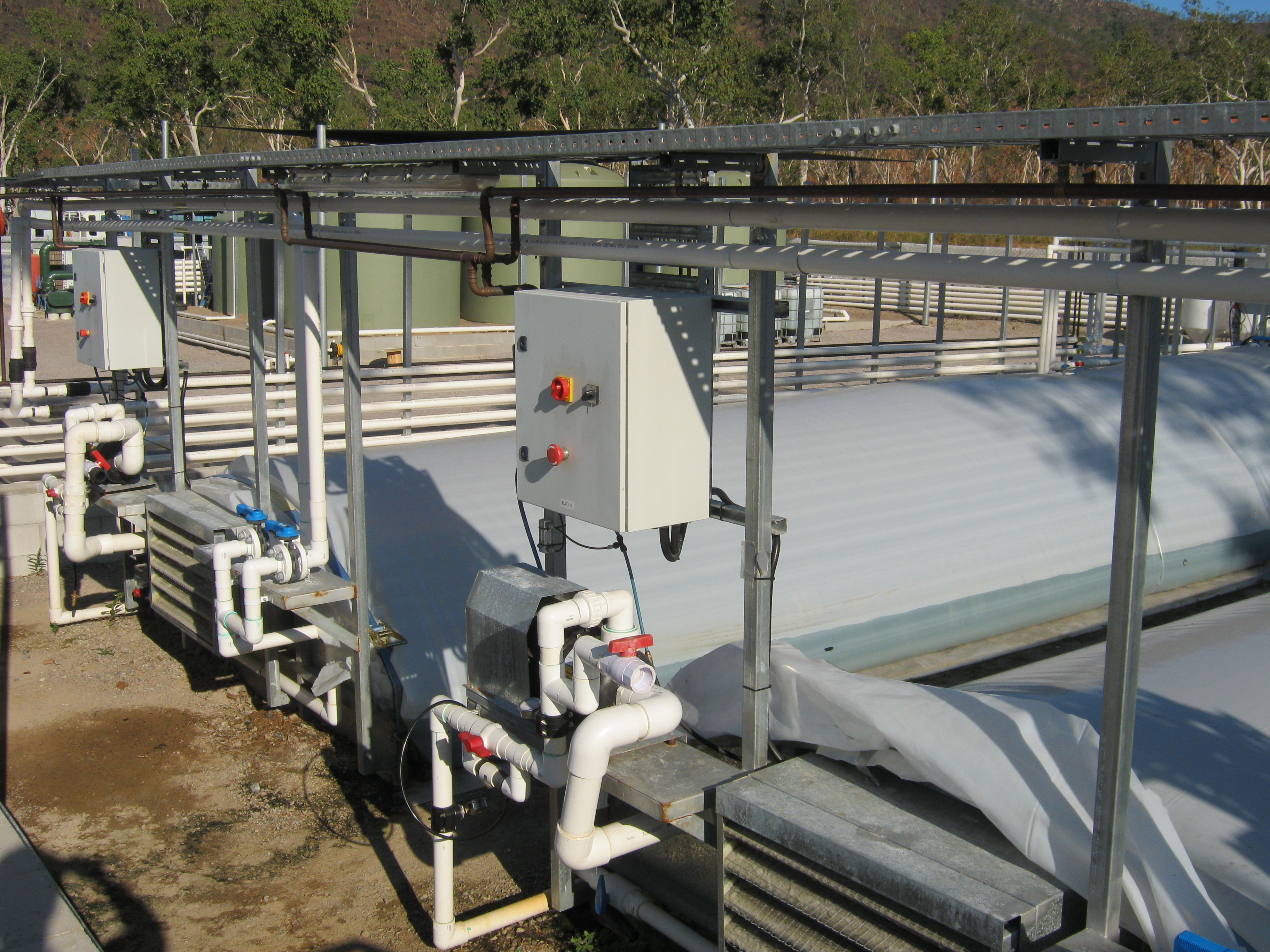
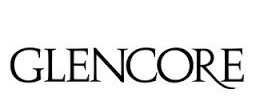
22M Flyover Conveyor
Oaky Creek Coal engaged Orana Engineering to perform electrical and control system design aspects of a 22M Flyover Conveyor to provide an interface between two existing conveyor systems.
Orana Engineering’s brownfield engineering expertise was drawn upon to resolve complexities in interfacing two different coal streams, powered from separate substations and controlled from independent process control systems. Should one system need to be shutdown it was necessary that the other system was not impacted.
The electrical engineering scope included powering the conveyor and transfer systems and providing lighting designs and power distribution. Control system engineering included selection and specification of instrumentation, specification of control system hardware and development of a functional specification.
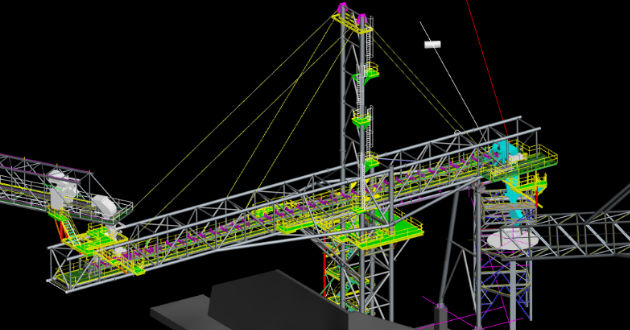
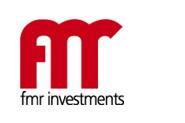
Ball Mill No. 2 Recommissioning
Eloise Copper Mine required recommissioning of their No.2 Ball Mill. During recommissioning it was identified that a means of relocating grinding media to the feed chute needed to be designed and engineered, with RPEQ certification. Orana Engineering was contacted to assist and a monorail, complete with electric hoist and trolley, was identified as being the practical solution.
Challenges presented themselves while locating the monorail within the existing structure, however Orana Engineering was able work within the constraints of the existing structure to meet client requirements. All elements of the structural engineering review and design of the monorail to were taken into account.
RPEQ certified fabrication and installation drawings were produced, ensuring the upgraded structure was fit for purpose.
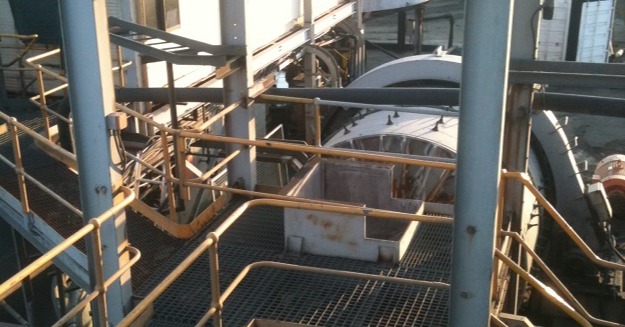
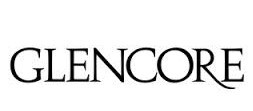
Crane Lifting Beam
The mother beam of the 40T ship loading crane at the Port of Townsville was nearing the end of its 30 year service life. Xstrata Copper engaged Orana Engineering to redesign the beam based on the existing beam and to incorporate changes in compliance with latest regulations.
After fully modelling the mother beam using Autodesk Inventor, RPEQ approved shop detail drawings were produced. Electrical monitoring systems were introduced to enable crane operators to confirm when the mother beam was fully engaged with various attachments, and control wiring to the beam was redesigned to include two cable drums whereas the original had three.
Mechanical redesign included a failsafe back-up locking system and design improvements highlighted by feedback from maintenance personnel.
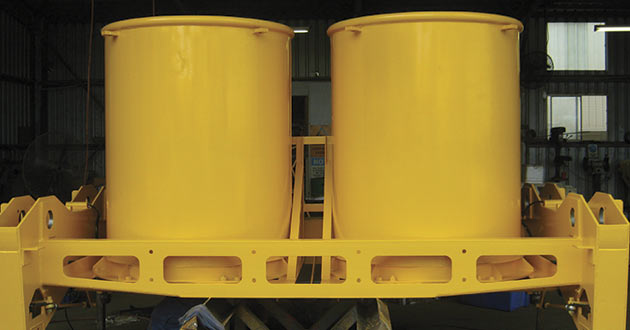
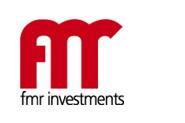
Crusher Circuit Upgrade
Eloise Copper Mine purchased a Metso dual deck vibrating screen to replace an existing smaller screen and a second Omnicone cone crusher to provide a secondary crushing circuit for increased production and efficiency. Orana Engineering was engaged to develop a design solution and detailed drawings for the secondary crushing circuit which utilised as much existing equipment as possible.
Orana Engineering was able to provide an efficient, practical design solution while minimising the associated design costs to provide site personnel with information required to refurbish and install the conveyor equipment necessary for the crushing circuit.
Orana Engineering successfully completed the design within a tight project time frame and produced in excess of 100 detailed drawings.
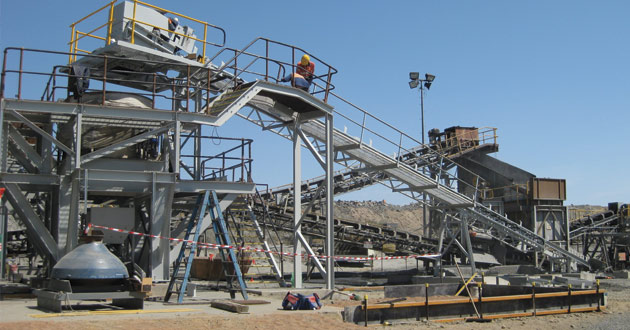
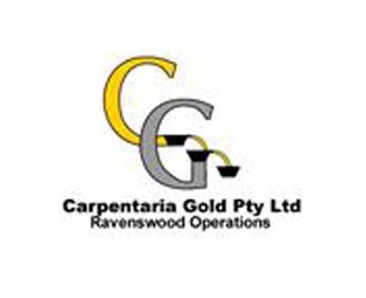
Cyanide Tank Upgrade
Carpentaria Gold identified that bunding around their Ravenswood cyanide storage tank was inadequate. Sodium Cyanide, used in the gold recovery process, is potentially lethal to humans and animals and detrimental to the environment. It is necessary to ensure it can be safely contained in an emergency.
Orana Engineering provided an innovative solution comprising a smaller tank fitted inside the existing tank. The design minimised loss of storage capacity by providing a smaller tank for primary storage whilst maintaining the existing external tank to act as the bund.
Utilising the existing tank as a bund, Orana Engineering delivered a design that met the client brief while re-using the majority of major tie-in points and providing improved access for maintenance.
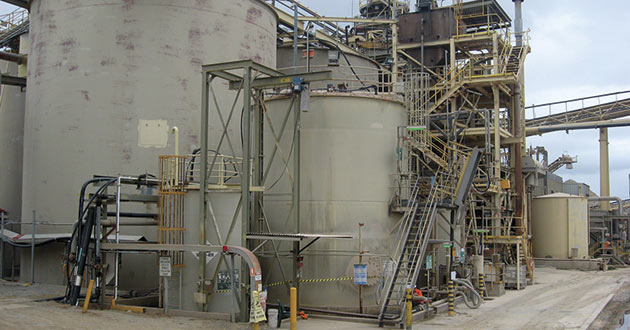
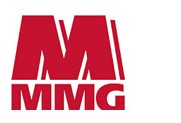
FB-028 Tank Lifting Beam
During an upgrade to the concentrator at MMG’s Century Mine, Orana Engineering was engaged to design a lifting beam for installation of a new flotation cell. The lifting beam design was to provide adaptation between lifting points on the tank and the crane, providing stability during lifting and protecting the integrity of the tank.
Structural considerations involved hand calculations and modelling in SPACE GASS based on client requirements and relevant Australian Standards. Orana Engineering's design utilised available structural members on site, providing cost benefits to the client.
Orana Engineering design staff created a 3D model in Autodesk Inventor, producing a fabrication drawing for the beam which also detailed the sling configuration for use during the lifting process.
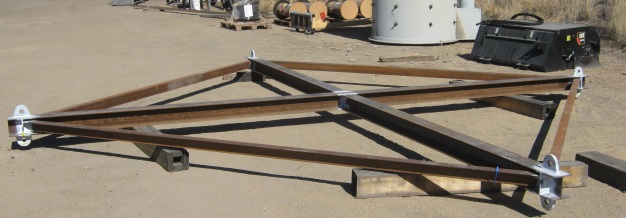
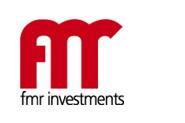
Flotation Cell Upgrade
To increase the efficiency of their concentrator, Eloise Copper Mine enlisted Orana Engineering to provide engineering and design assistance with installation of three copper concentrate scavenger cells within the existing plant.
3D models created by Orana Engineering designers were used to visually communicate solutions for new and existing equipment locations and structure arrangements. Detailing of these concept models enabled Orana Engineering to identify key tie-in locations within the plant for survey during the detailed design phase.
A multidisciplinary approach during detailed design ensured improved efficiency, with brownfield engineering challenges in relocating / connecting to existing equipment successfully achieved. Upon design completion the client was provided with an installation drawing set and scope of work.
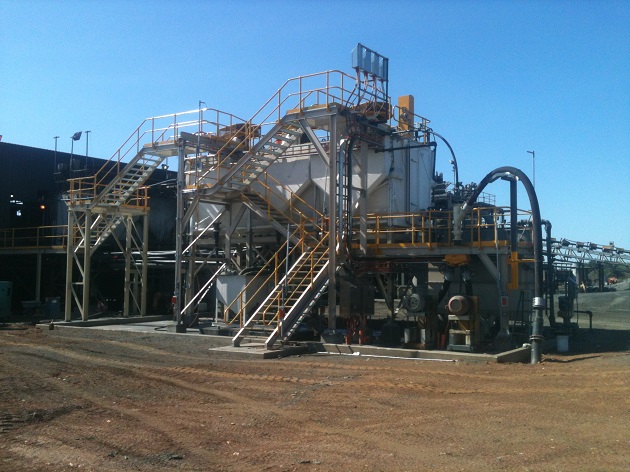
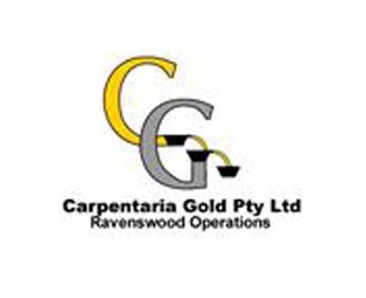
Gold Slurry Sampler
Orana Engineering was engaged to design new sampling equipment for improved sampling effectiveness at Carpentaria Gold’s Ravenswood operations.
A site visit was undertaken by Orana Engineering design staff to accurately record critical data. This enabled designers to produce a detailed 3D model which was used extensively during interactions with the client and ensured a fluent understanding of the project scope by both parties throughout the design process.
Orana Engineering was able to integrate new sampling equipment into the existing plant whilst minimising any impact on the operation. Various challenges were overcome with the result being successful delivery of drawings for fabrication and installation of equipment, allowing improved sampling and production reconciliation whilst minimising impact to operations.
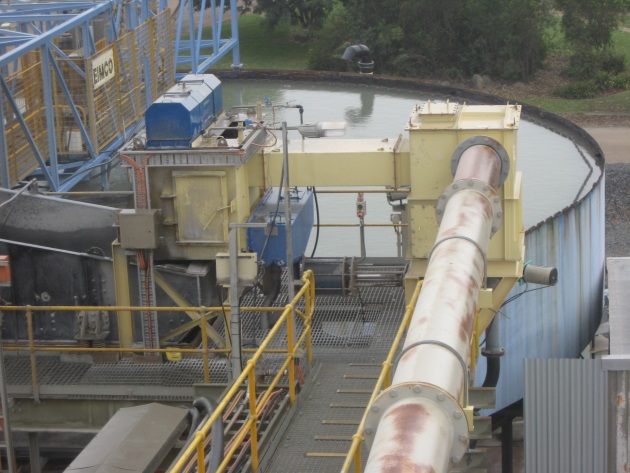
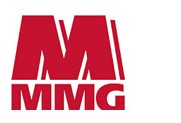
Heavy Vehicle Washdown Facility
MMG's Karumba Port Facility engaged Orana Engineering to design a heavy vehicle washdown facility to assist with management of concentrate for site vehicles and machinery. The time frame was short due to operational requirements, such that Orana Engineering worked from concept to IFC drawings in just seven days.
The design needed to accommodate a number of different vehicles from fully laden container trailers to a 30 tonne forklift, whilst also ensuring ease of facility maintenance and capture of runoff for environmental compliance.
Concept sketches were prepared, from which a detailed design was developed to meet client requirements. Through effective communication with the client Orana Engineering was able to deliver the design in a compressed timeline, to specification and budget.
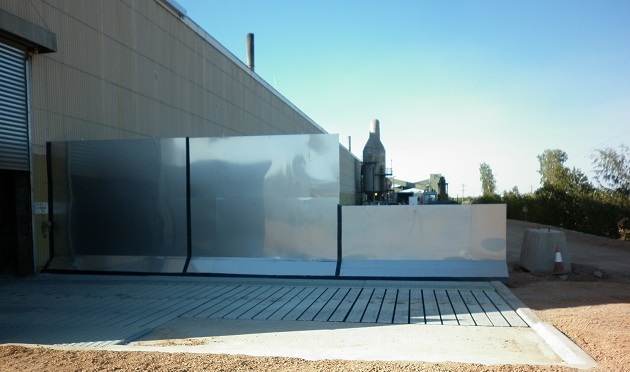
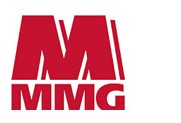
Inner Bypass Valves
Orana Engineering was engaged by MMG's Century Mine to design an upgrade within the concentrator for increased flow from a flotation cell to a tailings trough.
Orana Engineering conducted a concept investigation of available options to increase the flow rate. Results were presented for a range of design and operating conditions, and a preferred option was selected for detailed design.
Orana Engineering design staff created a 3D model of the new pipeline using Autodesk Inventor. The 3D model was used to produce fabrication drawings for pipe supports, new platform and new pipe bridge. Drawings also included isometric pipe spool drawings and revised P&ID drawings.
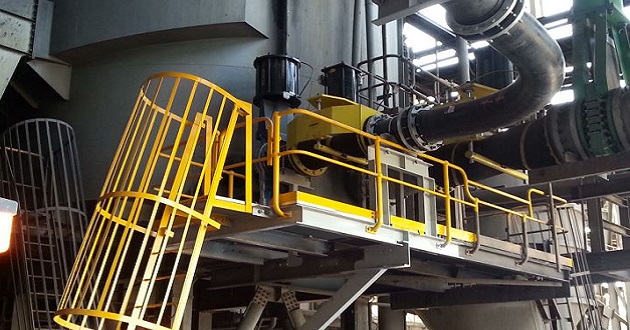
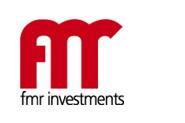
Jaw Crusher Platform
The maintenance department of Eloise Copper Mine contacted Orana Engineering with a requirement for design of an access platform for their jaw crusher, including engineering certification and drafting. The client provided site measurements and a basic concept of the design they were looking for.
Being a brownfield engineering project, the design had to consider the surrounding area and existing structures to minimise modifications. Autodesk Inventor was used to create a basic 3D model of the area. Once the physical data was established the detailed design of the platform was able to be performed efficiently.
Orana Engineering was able to produce both detailed shop drawings for fabrication and site installation drawings, all of which were provided with structural engineering certification.
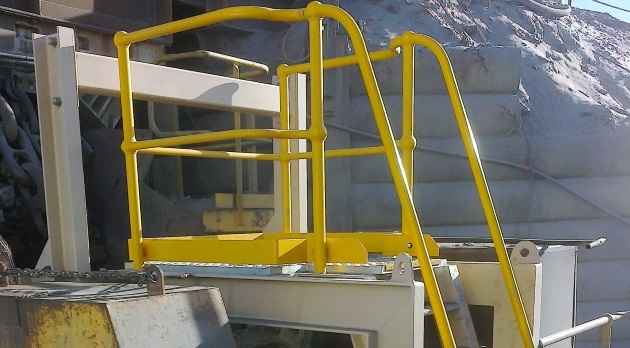
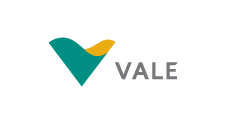
MG07 Conveyor – Chamber Design
Carborough Downs is an underground operation utilising conveyors to transport mined coal to the surface. As new longwall headings are mined, new conveyor installations are also required. Orana Engineering was engaged to complete a drive-head chamber design, ensuring adequate sizing for installation of conveyor equipment.
During initial mining of the chamber, a coal seam fault line was discovered. Carborough Downs requested that Orana Engineering develop a chamber design that maximised product mined through the fault area, while working within conveyor installation constraints. Using AutoCAD, Orana Engineering produced several design options and sketches for client approval and reference during mining processes.
Orana Engineering provided final chamber excavation drawings, which were developed into mine designs and sequence plans, by site mining engineers.
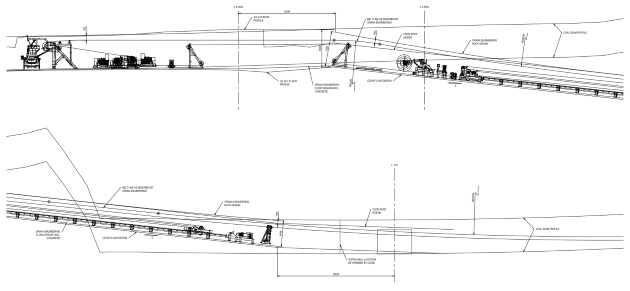
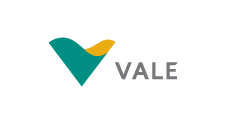
MG07 Conveyor – Civil Design
Carborough Downs is an underground operation utilising conveyors to transport mined coal to the surface. As new longwall headings are mined, new conveyor installations are also required. During installation of conveyors in an underground environment it is vital that the civil design is detailed accurately as this is the basis for locating and installing conveyor equipment.
Orana Engineering was engaged to complete this design and used AutoCAD to develop a civil design that met the client’s constraints and constructability requirements. From this design Orana Engineering produced a drawing set detailing civil aspects of the conveyor design, including floor / rib trimming, equipment hold-down details, configuration of concrete reinforcing and overall grade of concrete.
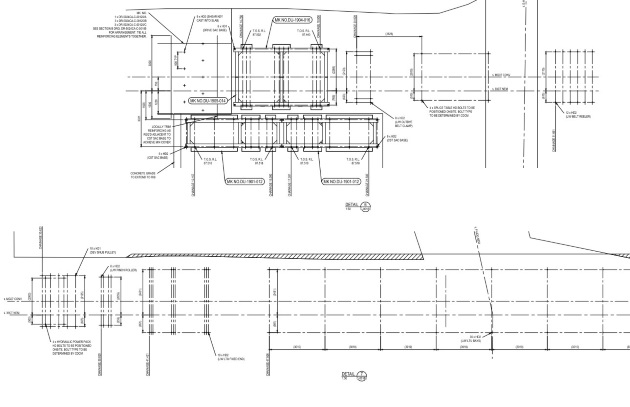
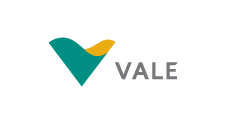
MG07 Conveyor – Development Conveyor
Carborough Downs Coal Mine is an underground operation utilising conveyors to transport mined coal to the surface for processing. As operations progress and new longwall headings are mined, new conveyor installations are also required.
Carborough Downs engaged Orana Engineering to complete a mechanical arrangement design for configuration of conveyor equipment. The design had to consider several factors, including meeting required operating capabilities, ensuring unimpeded access along travel roads and maintaining minimum belt curves.
Using AutoCAD, Orana Engineering developed a mechanical design that met client constraints and constructability requirements. From the design, a drawing set was produced detailing mechanical aspects of the conveyor design, including equipment configuration, and extensive details for selection and installation of conveyor structures, whilst minimising curves.
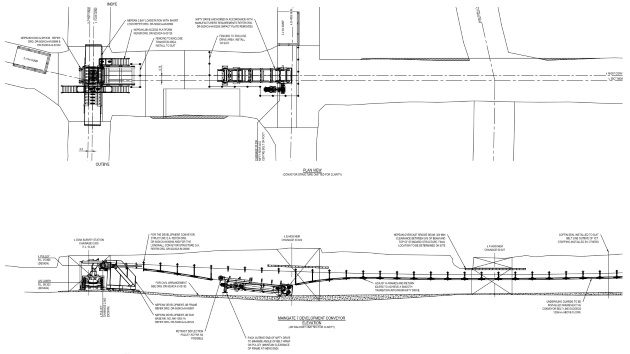
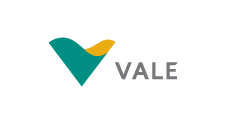
MG08 Development Conveyor
Carborough Downs Coal Mine is an underground operation utilising conveyors to transport mined coal to the surface for processing. As operations progress and new longwall headings are mined, new conveyor installations are also required.
Orana Engineering was engaged to design a new longwall drive-head chamber and conveyor installation, initially providing a drawing set detailing required drive-head chamber dimensions to suit the conveyor installation.
Using AutoCAD, a civil design and conveyor equipment arrangement was produced. The conveyor design had to consider several constraints, including available equipment, transfer tie-in to existing trunk conveyor, maintenance access, drainage, minimum clearances and belt curves.
Upon layout approval, AutoCAD drawings were produced detailing civil and mechanical design aspects, enabling site engineers to complete installation with efficiency while ensuring regulatory compliance.
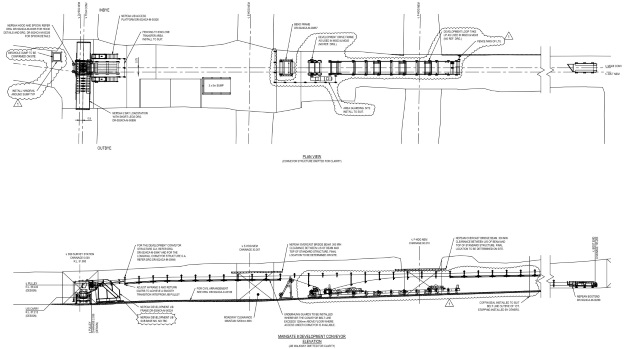
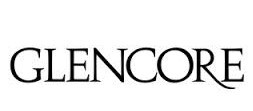
MIBC & Diesel Upgrade
The purpose of the Reagent System Upgrade at Oaky Creek was installation of new reagent storage tanks, discharge / delivery pumping systems and automated flow control distribution manifolds for the delivery of each reagent to the nominated process connections.
Orana Engineering performed mechanical, electrical and control systems design, drafting and engineering for the project. The primary deliverables included scope of works, construction drawings, functional specification, BOM, spares lists and equipment / instrument data sheets.
Orana Engineering managed the onsite commissioning of the system and provided a system handover to operations for implementation. An Operation & Maintenance Manual and Hazardous Area Dossier were provided on project completion.
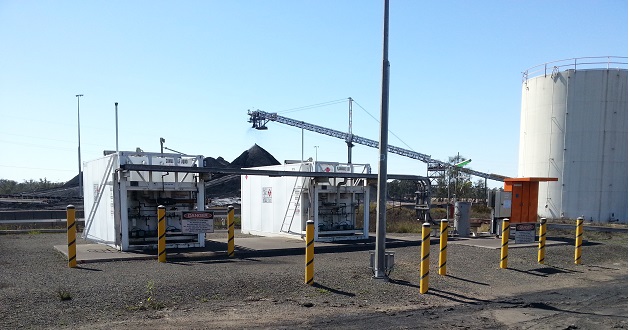
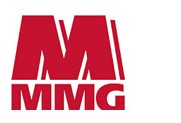
Mill Gear Box Frame
The IMT project team at MMG’s Century Zinc operations enlisted the assistance of Orana Engineering to produce a set of fabrication drawings for an existing gear box frame that required replacing. The frame had been in operation for some time, however there were no detailed drawings available for construction of a replacement unit.
The design staff at Orana Engineering created a detailed 3D model using client-supplied photos and sketches, enabling designers to produce 2D fabrication drawings for approval. A review of the drawings was conducted by the client to confirm the layout and accurate alignment with the existing installation on site. Following minor adjustments, As-Built status drawings were reissued to the client, accurately capturing detail of the existing frame.
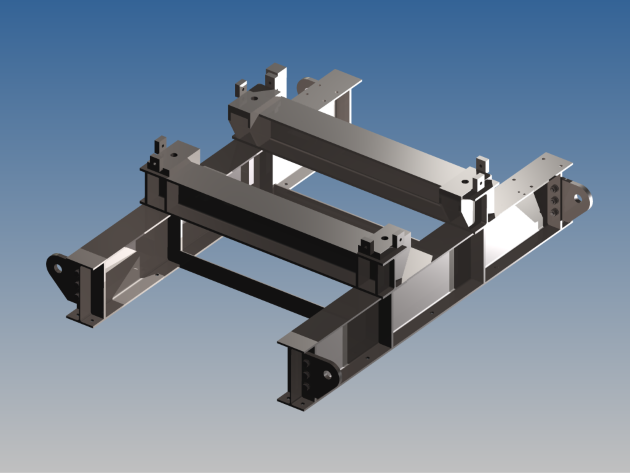
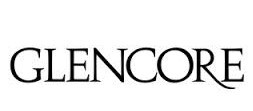
Onsite Accommodation Camp Services
Orana Engineering was engaged by Oaky Creek Coal to assist in design and construction of onsite camp accommodation, including an HV substation for power and potable water supply.
The brief included mechanical, electrical and control systems design, drafting and engineering for the project. Deliverables included scope of works, construction drawings, functional specification, drawing and equipment registers, commissioning and operating spares lists and equipment and instrument data sheets.
Orana Engineering provided PLC configuration and commissioning assistance for pump control, acted as Client Representative during construction, managed onsite commissioning of the system, and provided a handover to operations for implementation.
Operation & Maintenance Manuals for potable water storage and the HV substation were provided upon completion.
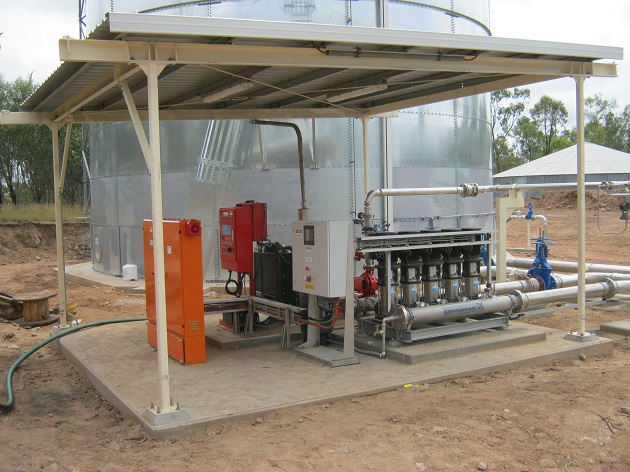
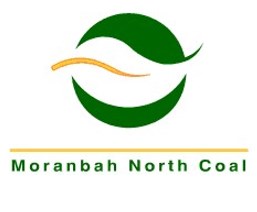
Reagents Lightning Protection
To ensure the CHPP reagent tank farm lighting protection systems complied with Australian Standards, Moranbah North Coal requested Orana Engineering to undertake a review and design an upgrade of the lightning protection systems for the tank farm area.
With the area encompassing fuel storage tanks, it was classified as having structures with "explosive or highly flammable contents" and was therefore required to comply with AS1768:2008 Lightning Protection. Orana Engineering’s audit of the installation and its lightning protection systems confirmed that an upgrade of the facility was needed to comply with current lightning protection standards.
Utilising its team of detailed drafters Orana Engineering created a set of drawings detailing the work required to comply with AS1768:2008 Lightning Protection.
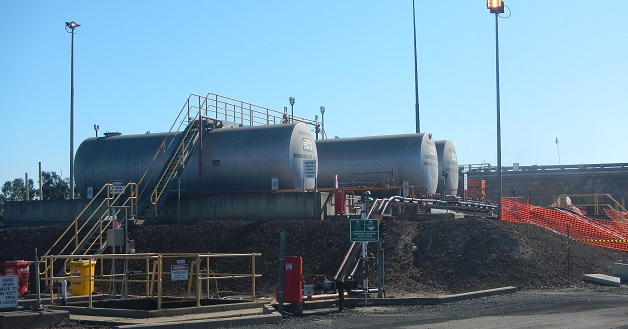
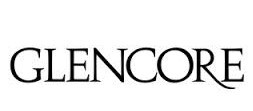
Redraw Dragline DL007 Drawings
To improve the maintainability of plant electrical systems and personnel safety, Hail Creek Mine employed the drawing revision services of Orana Engineering to redraw electrical power, control and termination diagrams associated with its Dragline 7 into AutoCAD format.
Having electrical drawings in CAD (computer aided design) format, is one of the most efficient ways to capture site electrical modifications, installations or as-building changes for ready access by site personnel involved in maintenance and operations.
Working closely with site contacts and onsite electricians, Orana Engineering was able to accurately reproduce 247 electrical drawings into AutoCAD for Dragline 7.
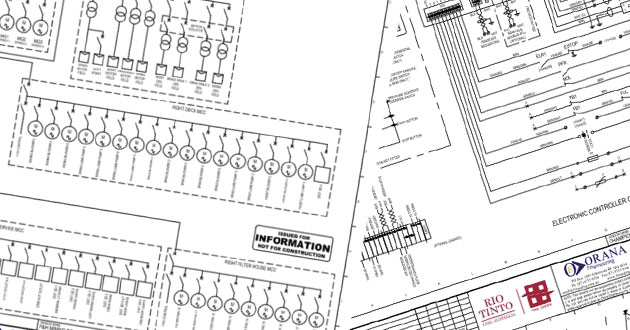
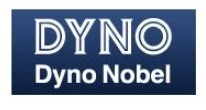
Redraw Electrical Drawings
To ensure plant maintainability and personnel safety, Dyno Nobel employed Orana Engineering to redraw its low voltage and high voltage single line diagrams, while also confirming their accuracy and functionality.
Through the use of client photos, documentation and discussions Orana Engineering was able to accurately redraw 52 low voltage single line diagrams as well as 6 high voltage single line diagrams.
During the redraw process Orana Engineering identified that a larger size drawing template was required to ensure critical information was easily readable on a single drawing. An A0 size drawing template was designed to meet Dyno Nobel's drawing standards with the template providing links for the document management system to easily access drawing metadata.
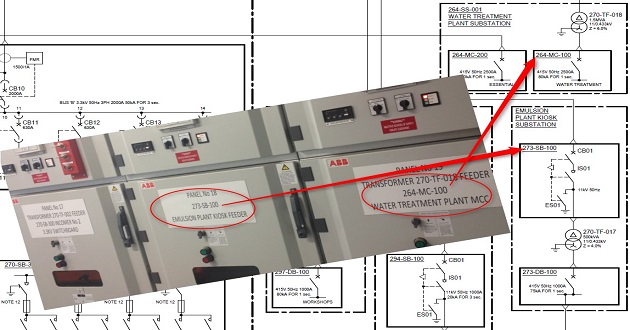
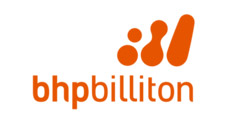
SAG Mill Cover
BHP Billiton Cannington Mine, is a significant miner and exporter of silver and lead concentrate. Orana Engineering was engaged to provide workshop fabrication drawings for a replacement cover to address corrosion issues around flanges and access openings on the existing SAG mill trommel sump cover.
Following a site visit to obtain measurements, photos, drawings and documentation, the Orana Engineering design drafting team created a detailed 3D model of the existing structure incorporating new components to produce a set of detailed shop fabrication drawings, while also revising multiple existing drawings. These drawings were reissued for construction after receiving client approval.
The new cover sections and access panels improved the safety of trommel operation while also reducing inspection and maintenance time.
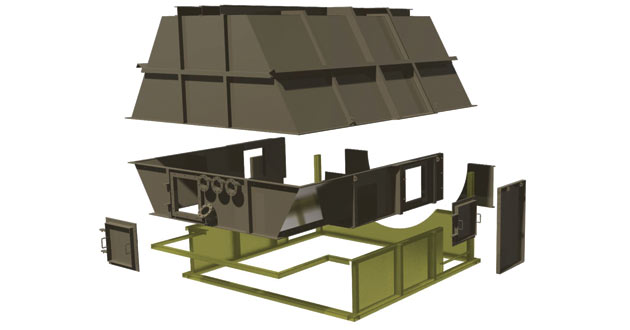
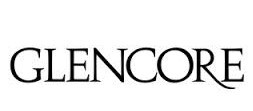
Sewage Treatment Plant Refurbishment
To increase productivity and maintain compliance with legislative standards, Glencore Oaky Creek Coal employed the services of Orana Engineering to design and manage the electrical aspects of an upgrade to their existing sewage treatment plant.
The project was managed on-site by others, with Orana Engineering providing electrical engineering, design, project management and construction / commissioning assistance.
Upon completion of installation, Orana Engineering updated all drawings to reflect any changes made, thus providing Glencore Coal with as-built drawings which will make any future maintenance or fault-finding work more efficient and cost effective, as well as providing legislative compliance.
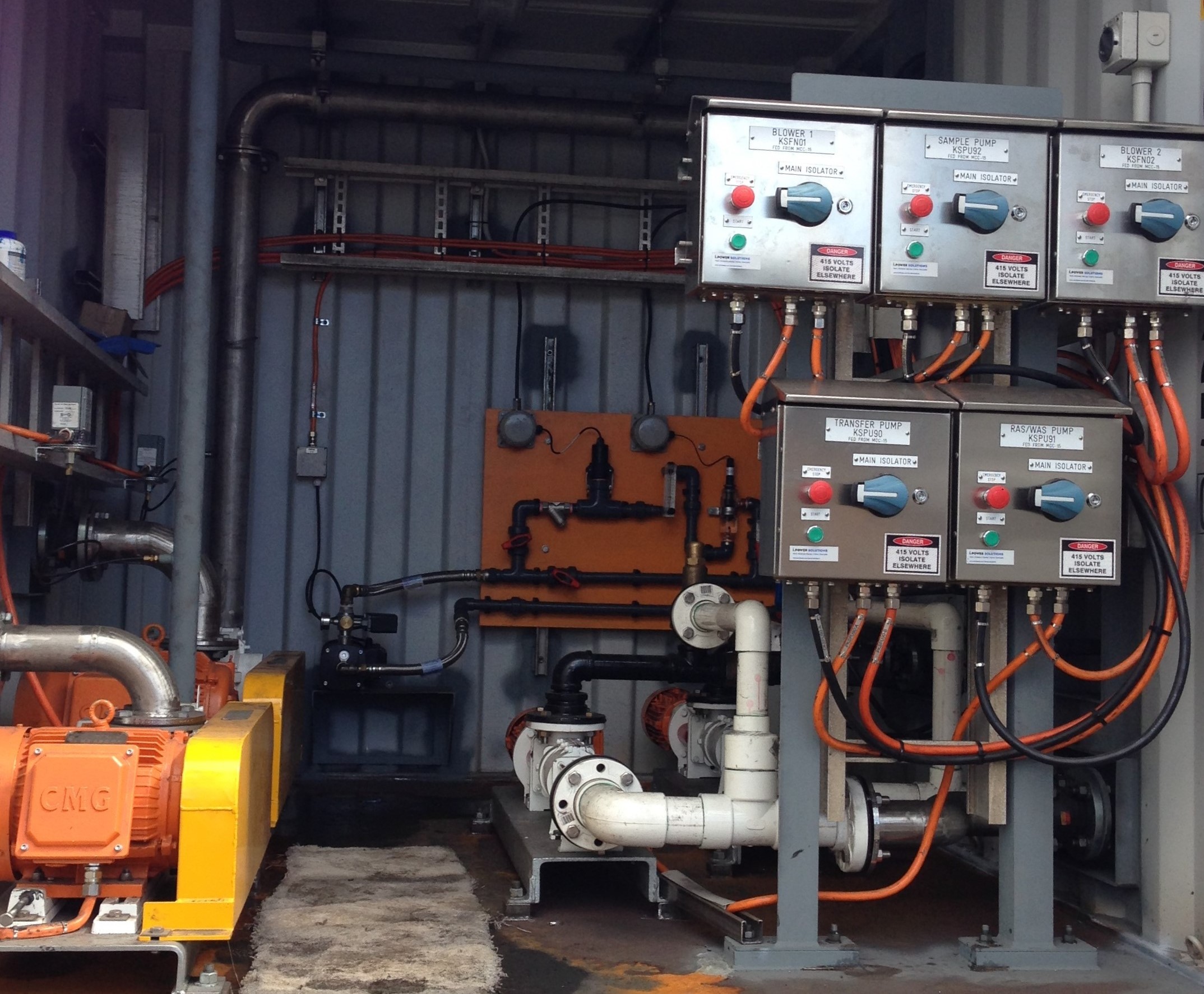
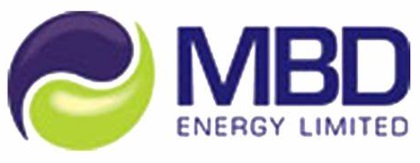
Tank Farm Upgrade
Melbourne Bio Diesel’s James Cook University research facility required an elevated level area for installation of fresh sea water storage tanks. Orana Engineering was requested to design a solution that increased efficiency with tank drainage and improved safety around the tanks.
A site visit was performed to gather measurements of the nominated tank farm area. This included identifying trees requiring removal and determining required tank heights and current ground levels. From the information gathered Orana Engineering used AutoCAD to model ground levels and the amount of fill required to lift tanks to a suitable level for gravity drainage. The design incorporated a conical base on each tank for drainage and the introduction of buried control valves accessible via covered pits.
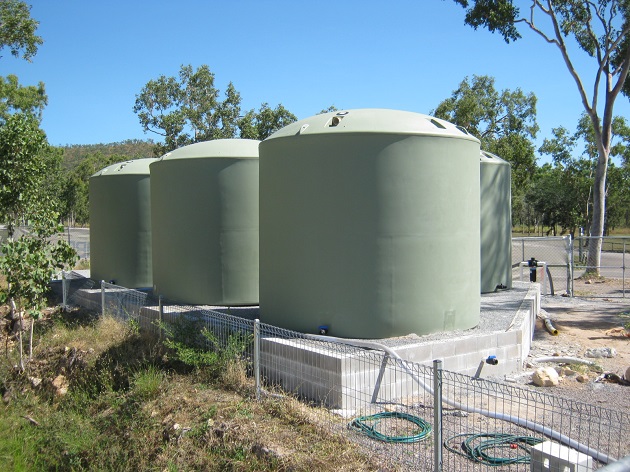
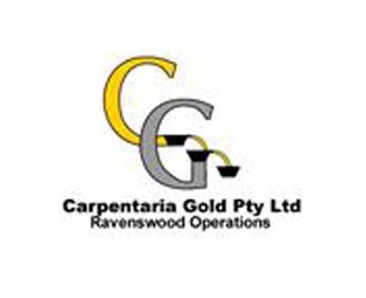
Tank Static Line
Management at Carpentaria Gold’s Ravenswood Operation enlisted Orana Engineering to design a fall arrest system that could be easily removed and repositioned above multiple leach tanks, allowing for safe removal and servicing of tank agitators.
From a site visit, Orana Engineering identified the need for an arrangement that could be easily disassembled and relocated to each leach tank. The design was challenging due to the varying nature of access structure members above tanks.
Orana Engineering designers proposed an assembly utilising a common set of supporting columns with struts of varying lengths depending on the work location. A full set of shop fabrication and assembly drawings were issued with the final design providing safety for personnel working above open tanks.
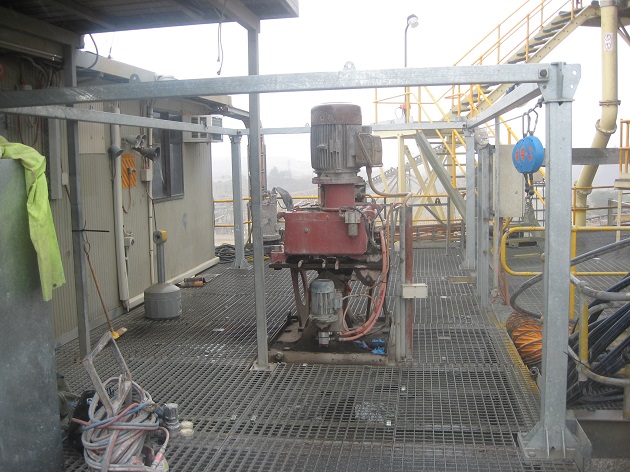
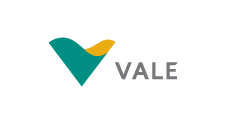
TC04 Trunk Conveyor Extensions
Carborough Downs Coal Mine is an underground operation utilising conveyors to transport raw material to the surface for processing. As operations progress new trunk conveyor extensions are required.
Orana Engineering was engaged to assist with the process of extending an underground trunk conveyor. This involved using survey data of the conveyor heading and designing a suitable belt profile, utilising minimum conveyor curves identified in the conveyor power and tension analysis.
Orana Engineering produced a set of drawings detailing the belt profile, conveyor structures and locations for roof bolts that the structures would be suspended from. These drawings enabled site engineers to complete the conveyor structure installation and conveyor extension with minimal risk of error and conveyor tracking problems.
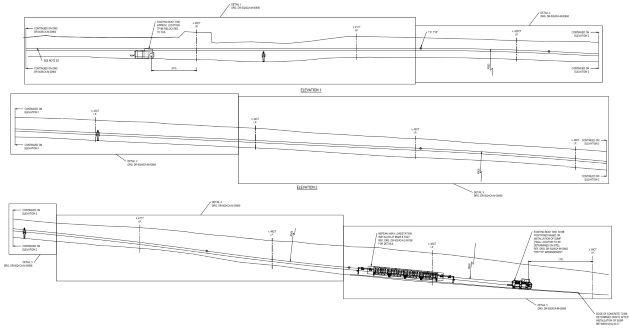
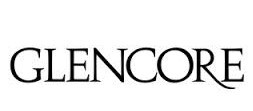
Tippler Refurbishment Feasibility
Glencore Port Operations in Townsville operate an export facility for minerals concentrate and refined copper within the Port of Townsville precinct. The concentrate in-loading rotaside tippler was identified as being at end of life and a feasibility study was commissioned to review a like-for-like replacement option for refurbishment of the tippler.
To facilitate feasibility-level costing, Orana Engineering was asked to provide electrical engineering and mechanical engineering assistance with provision of a concept design for the proposed refurbishment and upgrade.
By working closely with Glencore, and other consultants engaged on the project, Orana Engineering was able to contribute as part of a collective "owners engineering team" to the feasibility assessment of a significant engineering project in the Townsville Region.
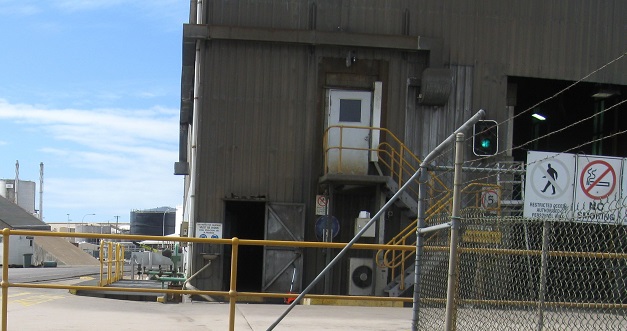
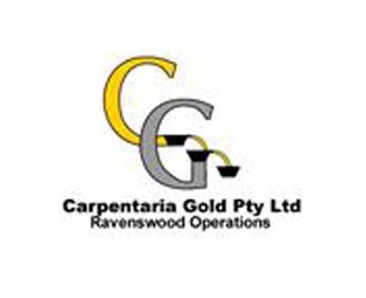
TK102 Bypass Piping
When tasked with a major repair to one of their leaching tanks, personnel at Carpentaria Gold's Ravenswood Operations enlisted the assistance of Orana Engineering to develop a solution that would allow process operations to continue whilst leaching tank TK102 was out of service.
A site visit and discussions with the client suggested the installation of a bypass line around TK102. By utilising site information, Orana Engineering designerswere able to detail a new bypass line through the existing processing plant area. This involved minor modification of existing structural steel and addition of pipe supports for the new HDPE bypass pipeline.
Bypass piping was successfully installed during normal operation with only tie-ins needing to be installed during a single shut down.
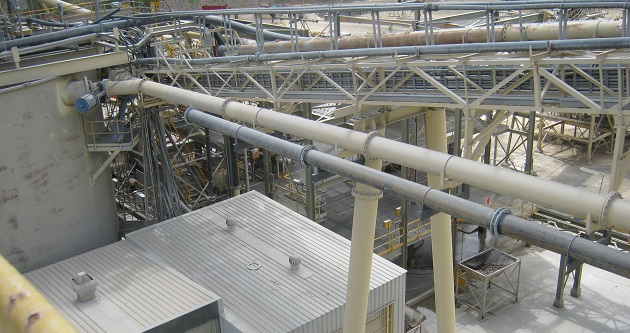
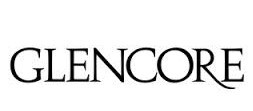
UG Conveyor Installations – MG32 Tripper Chamber
At Glencore’s Oaky No.1 underground coal mine, transportation of vast quantities of coal over long distances requires significant power. Often drive-head power is insufficient or constrained by allowable belt tension and an additional drive or power source is required to meet operating capacity. Additional power is commonly sourced from a driven conveyor tripper installed along the conveyor with appropriate excavation for the tripper.
Using the client’s existing mine plan to position the new tripper chamber, Orana Engineering design drafting personnel worked with site engineers to assess required chamber dimensions while simultaneously minimising the excavation of material.
Orana Engineering used AutoCAD to produce a drawing set detailing the mining required, and an overlay showing future equipment installations within the new chamber.
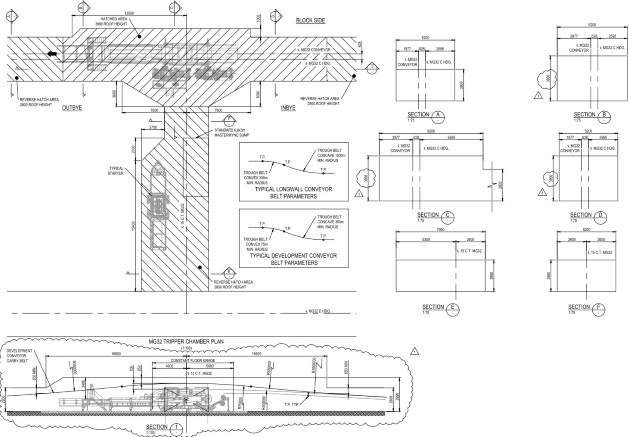
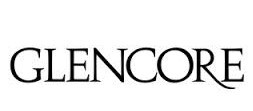
UG Conveyor Installations – MG32 Tripper Civil Design
Engineers at Glencore’s Oaky No. 1 underground coal mine engaged Orana Engineering to determine civil work requirements to install tripper equipment on the MG32 longwall conveyor. On completion of chamber mining, finished surfaces (rib and floor) may require modification for the installation of conveyor tripper equipment. The civil design must determine concrete grades for drainage, safe access and reinforcing for conveyor equipment, while minimising trimming and concrete required.
Manipulating “as-cut” survey data using AutoCAD, Orana Engineering design staff could accurately determine where tripper equipment could be installed with minimal trimming and concreting. A drawing set was produced detailing civil aspects of the tripper design, including chamber trimming, equipment mounting locations, configuration of reinforcing and relative concrete levels for drainage.
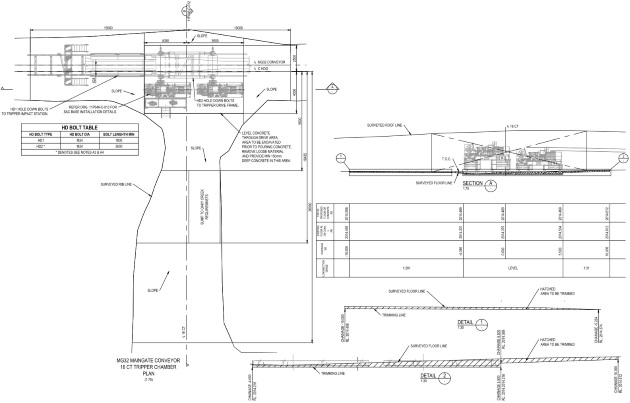
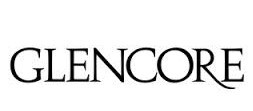
UG Conveyor Installations – MG32 Tripper Mechanical Design
Orana Engineering was engaged by Glencore to design and install a detailed arrangement of tripper drives, brakes, pulley frame and load station for the MG32 conveyor at its Oaky No.1 underground coal mine.
Mechanical design considerations included operating capabilities, unimpeded travel road access and minimum belt curves. The design was dependent on the civil installation previously detailed by Orana Engineering. Often equipment is simply re-located from previous installations with minor modifications. Orana Engineering has developed unique methods for completing this type of design efficiently and at reduced cost to our clients.
AutoCAD was used to develop a mechanical design, from which a drawing set was produced that detailed out the mechanical aspects of the tripper installation
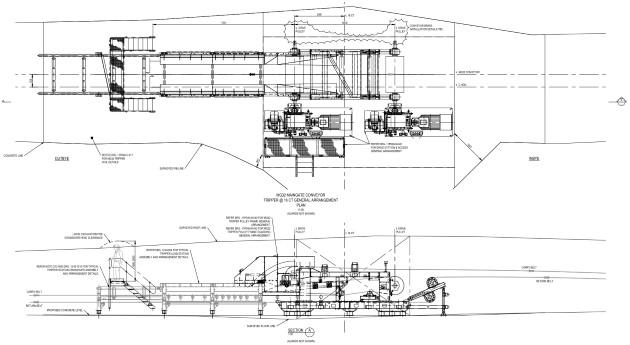
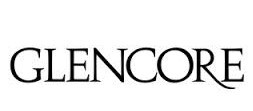
UG Conveyor Installations - MG Chamber Design
Mining millions of tonnes of material requires significant infrastructure and planning. Orana Engineering has been engaged on multiple occasions at Glencore’s Oaky No. 1 underground coal mine, to design new conveyor drivehead chambers to install equipment for longwall mining.
Using the client’s existing mine plan, Orana Engineering design drafting personnel worked in tandem with engineers to assess required chamber locations and dimensions, with consideration to the size and orientation of equipment to be installed and minimising the material to be excavated.
An AutoCAD drawing set was produced detailing the extent of mining required along with an overlay showing future equipment installations, enabling the client to efficiently complete chamber mining with a design suitable for future installations and minimal rework.
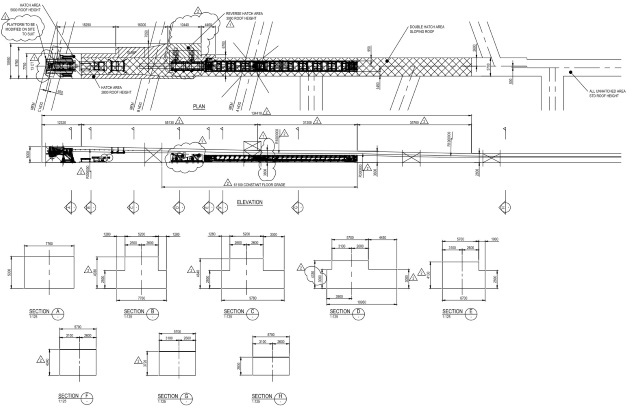
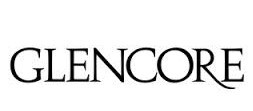
UG Conveyor Installations - MG Civil Installation
Engineers at Glencore’s Oaky No. 1 underground coal mine engaged Orana Engineering to determine civil work requirements to effectively utilise drive-head equipment in newly mined chambers for conveyor installations.
On completion of chamber mining, finished surfaces (rib and floor) may require modification for installation of the conveyor drive-head equipment. The civil design must determine concrete grades for drainage, safe access and reinforcing for conveyor equipment, while minimising trimming and concrete required.
Manipulating “as-cut” survey data using AutoCAD, Orana Engineering design staff could accurately determine where equipment might be installed with minimal trimming and concreting. A drawing set was produced detailing civil aspects of the conveyor design, including chamber trimming, equipment mounting locations, configuration of reinforcing and relative concrete levels.
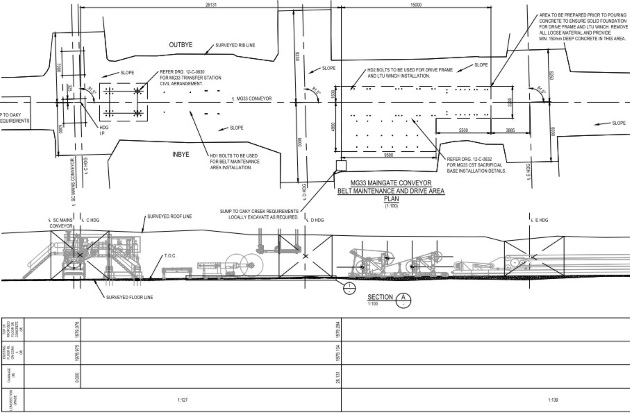
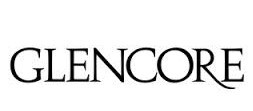
Underground Workshop Concept Design
Due to expanding operations, Glencore's Oaky North underground operations saw benefit in having an underground workshop and refueling stations to reduce vehicle travel times and increase efficiencies. Orana Engineering was engaged to provide concept design and estimating assistance for project approval.
From communications with our client, Orana Engineering prepared concept general arrangement drawings for consideration. Based on these concept design drawings, a project capital estimate and project schedule were prepared for Oaky North.
From the information presented by Orana Engineering, the client could accurately consider whether the underground workshop was feasible and ensure that appropriate budgeting and project planning was completed at the concept design phase to improve confidence in the project prior to execution.
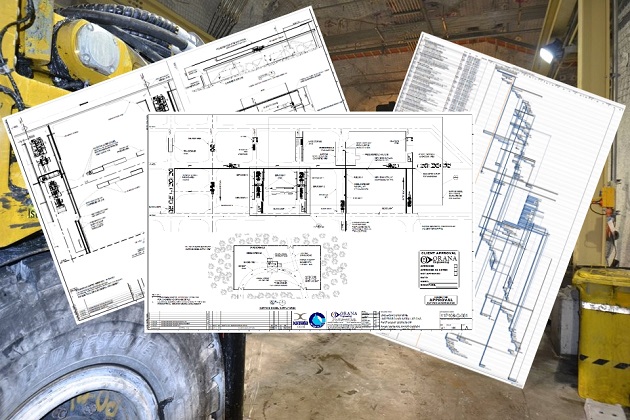
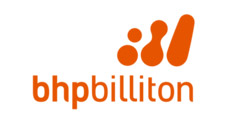
Wall Kit Drafting
BHP Billiton's Cannington Mine is a significant underground silver and lead mining operation in Western Queensland. Following completion of ore extraction from each stope, paste backfill is used to fill the open void and stabilise the area. This is achieved by constructing a fill wall which provides stability for areas being backfilled, eliminates intrusion, and allows a higher density of backfill.
Wall construction kits supplied to Cannington contained no documentation detailing the kit components. BHP Billiton engaged Orana Engineering to confirm the components in these kits.
Using measurements and sketches obtained from site, Orana Engineering design drafting personnel utilised AutoCAD to create a drawing set detailing the components required and fabrication details for each construction kit.
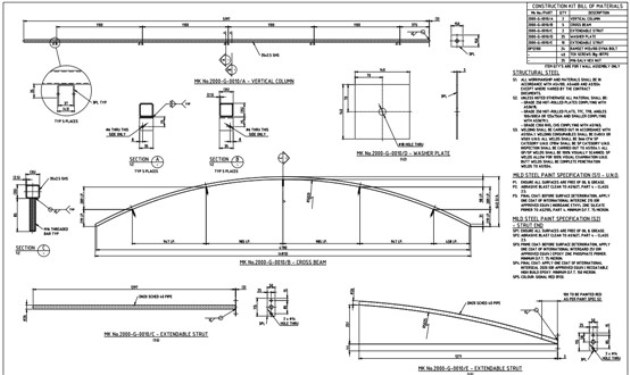
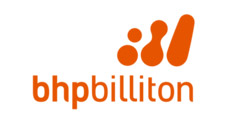
Water Polishing Plant Access Platform
BHP Billiton Cannington’s Port Storage Facility operates a water polishing plant for treatment of stored water. The system requires regular maintenance for replacement of plant filtration rods, however with maintenance ports inaccessible from the ground, work platforms had to be arranged. To simplify this task and improve safety, BHP Billiton Cannington identified the need for a permanent access platform.
Orana Engineering was engaged to design a platform that allowed easy access to the maintenance port, while ensuring access to existing services was not compromised.
Orana Engineering utilised AutoDesk Inventor to model a platform that would not impact on the existing structure, services or access routes while ensuring safety for maintenance workers. Following model verification, shop detail fabrication drawings were produced.
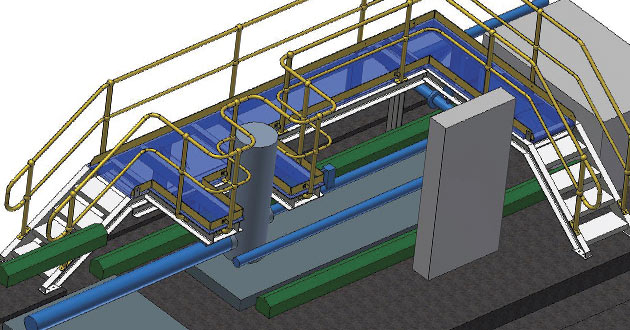
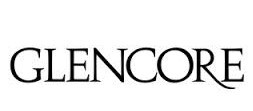
Yokogawa DCS Upgrade
Since 2005, Orana Engineering has provided 24/7 support for Glencore's Oaky Creek Coal control systems. At the CHPP a Yokogawa DCS installed in 1998 is used as the primary control system. With existing CentumCS Unix software no longer supported by Yokogawa, it was essential to complete an upgrade to the CentumCS3000 system.
Orana Engineering developed conversion tools to allow configuration data to be extracted from the CentumCS Unix platform and imported into the CentumCS3000 environment. These tools provided efficiency and accuracy for the conversion and delivered a significant cost saving.
The quality of conversion tools and simulation programs developed by Orana Engineering resulted in highly efficient site commissioning, completed without plant downtime.
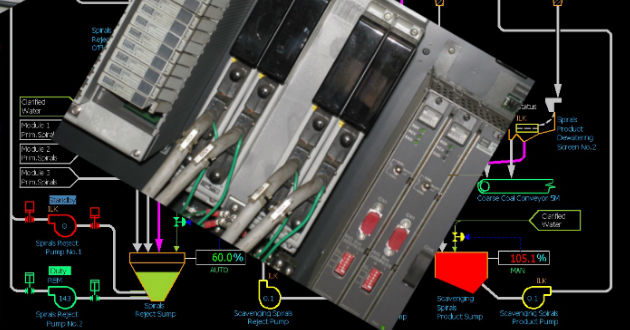